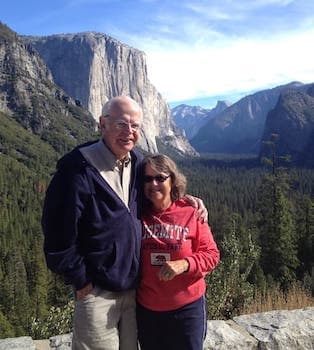
Curated with aloha by
Ted Mooney, P.E. RET
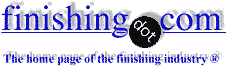
The authoritative public forum
for Metal Finishing 1989-2025
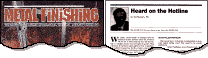
-----
Nitric Passivation of 17-4 Wire EDM surface
August 26, 2008
We are passivating 17-4 SS parts which have been wire edm'ed, which leaves a recast layer on the surface where the spark contacts the part. If we try to remove the recast layer by glass bead blast
(which we typically do to remove scale from heat treat) and then passivate in nitric (per ASTM A967 Nitric 2 and 4 - we do both), we end up with a very noticeable yellow tint on the wired surfaces. Many of our wired surfaces are too difficult to reach by brush/wheel methods to remove the recast.
We've also tried passivating the parts prior to bead blast
(ultrasonic clean, heat treat, wire, ultrasonic clean, passivate, bead blast, passivate again). This gives us a much better finish, but inconsistent results on copper sulphate
⇦ this on
eBay or
Amazon [affil links] tests, and I'm not sure if this is a legit way (much of my research on here seems to frown upon placing parts with heat scale into nitric).
Two main questions are: 1. is there any harm to passivating with heat scale on the part? 2. Does anyone have any recommendations to help with this (i.e., longer time in nitric, use nitric 2 first, then nitric
4 after, etc). We would prefer to not use any type of pickling operation, or introduce other chemicals (to keep products in-house).
Regards,
Engineer - Charlton, Massachusetts
As a follow up to this question, we've had some success leaving the parts in the acid longer (as much as an hour). ASTM A967 does not seem to state a maximum time, only a minimum. Would leaving parts in for double the minimum time cause any issues?
Any help on this would be greatly appreciated.
- Charlton, Massachusetts
September 12, 2008
Miles, you may want to run a test lot using a stainless media. Depending on the recast area to be cleaned of the spark contact, you may want to try a cut wire shot if you need to remove material or a conditioned cut wire shot if just a burinish "peened" clean up area is desired. The cut wire media will last 10,000x longer than the glass bead, so if a dedicated small blast cabinet can be set up, it may prove very cost effective.
Tim DeakinNorth Tonawanda, New York
September 21, 2008
Thanks for the suggestion Tim. Unfortunately, we are held to the glass bead media by customer requirements. I may look into the conditioned shot a little more though to see how well it removes the re-cast, and follow it with a glass bead blast for the final finish. Thanks.
Miles KB- Charlton, Massachusetts
September 29, 2008
We are looking for a method of passivating (or a non-reactive coating for) pharmacuetical grade silicate glass ampules for us that contain 1% H2S solution without phyiscal or optical degradation of the ampule or infrared absorption at infrared wavelengths in the 1000-3000nm range. Any suggestions?
Jean Berthold- Bacliff, Texas
August 14, 2009

this text gets replaced with bannerText
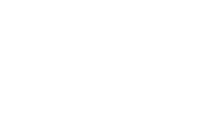
Q, A, or Comment on THIS thread -or- Start a NEW Thread