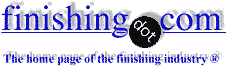
-----
Chemistry of Hard Anodizing
August 3, 2008
Hi, I'm a pure applied chemistry graduate (or was a few misty years back) and I've been asked to explain aluminum hard anodizing to atom detail for an uncle who runs a machine shop. So! I'm learning as quickly as I can. I'm trying to answer in detail why hard anodizing has to be cooled. If anyone could tell me if the following makes sense It would help a lot.
When hard anodizing the acid concentration is kept high to create pores on the inside of the oxide (facilitating ion transfer), however the temperature is kept very low to slow the dissolution of the outside layer of oxide (allowing for a thick layer to build). The voltage has to be ramped up as quickly as possible to create a hard layer as ramping up slowly would allow the pores to become too large making the oxide softer (which may have its own applications).
Is this the correct reason for cooling? Does ramping still exist in practice or is a single high voltage used?
Thanks so much for any help. keep keeping it real finishers =).
Anodizing Apprentice - California
August 4, 2008
Hi, John. We know that 20 x 30 = 600, and 30 x 20 = 600, and that in mathematics it doesn't matter what order you put the factors in. But when it comes to anodizing and other electrochemical processes, this rule doesn't hold. You are not free to anodize for 20 minutes at 30 ASF just because you successfully anodized for 30 minutes at 20 ASF. Rather, for reasons that are complicated, and in some cases maybe not even fully understood, there are acceptable ranges for all parameters. You can't anodize slower than the acceptable range because the acid will eat away the anodized film faster than you create it. You can't anodize faster than the empirically-derived acceptable range because the part will "burn" (the aluminum will actually become too hot for the reaction to proceed correctly). And if everything is not held within a very tight range, the anodizing will not be acceptable for one reason or another (it will flake, crack too easy, be too soft, get white spots, black spots, visible striations, discoloration, etc.)
So it has been found empirically that hard anodizing is best when done at a temperature of about 28 deg. F. It is largely a matter that the acid will dissolve the anodizing too fast if the acid is hotter, but not solely a matter of that. The cooling is required to keep the acid from being too aggressive, but also to keep the part from getting too hot (that's why good agitation is important).
To answer your question about "ramping", it is not some theoretical thing, it is what is done in practice every time. When a raw part enters the tank, if the voltage is not low, excessive current will flow and the part will burn. As the insulating anodized layer grows, the voltage must be raised or insufficient current will flow. In general, people don't ramp up "as quickly as possible to create a hard layer", they generally shoot for a consistent amperage, and ramp the voltage up to hold that amperage. That is not to say that no one ever targets a particular amperage/time profile, as opposed to consistent amperage, sometimes they do. Good luck.
Regards,
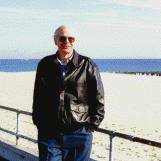
Ted Mooney, P.E.
Striving to live Aloha
finishing.com - Pine Beach, New Jersey

Q, A, or Comment on THIS thread -or- Start a NEW Thread