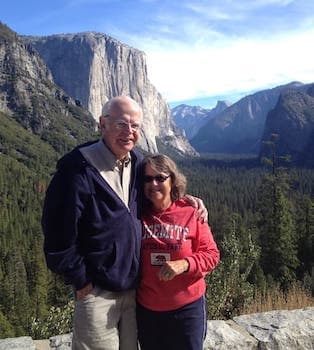
Curated with aloha by
Ted Mooney, P.E. RET
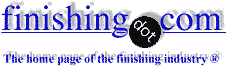
The authoritative public forum
for Metal Finishing 1989-2025
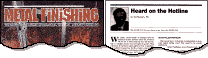
-----
Flash Rusting on CRS Profiles in a Zinc Phosphating Process
July 30, 2008
Dear Experts,
I am doing a commissioning on a new plant for a zinc phosphating process. The sequence is like this; Knock-off Degreasing, Degreasing, Rinse 1, Rinse 2, ZnPO4, Rinse 3, Rinse 4.
We use alkaline degreasing with bulit-in conditioning/activation on it, thus we eliminate the activation stage and convert it into Rinse
2. At first we ran at a speed of 1.5 m/min and having a pressure on of 1.5 bar at the ZnPO4 stage. We added half-liter of Accelerator/m3 of the tank and the Free acid is giving 0.9 points while Total acid is about 10 points. The problem we faced was that when we ran CRS profiles, it gave us flash rust, usually it occurs after Rinse 3 and it grows after Rinse 4, until it drys-off.
Can you explain to me about inter-stage drying, misting on ZnPO4 stage, and what if I use nitrites as sealer instead of Hex. Chrome to prevent flash rusting. The plant is also having a Final DI rinse but at the moment is not yet activated.
The water we use is having conductivity of 1200 micro S/cm and a pH of around 7.
Temperature in KOD, Degreasing and ZnPO4 is almost the same, around
55 deg. C
Best regards,
Sev
sales - Riyadh, Saudi Arabia
August 1, 2008
Hi Sev,
You don't say whether this line is spray or immersion, and this could have an impact on the solution to the problem. You also don't list the contact time in the phosphating stage, also important information.
Flash rust occurs in a phosphating operation when the conditions of the washer are ripe for corrosion. The hot, humid, acidic atmosphere that is present in a phosphating tank is a good environment for promoting corrosion, so this is why you have to run the line in optimal fashion.
Firstly, I would not combine the conditioner in the alkaline cleaner. The conditioner works much better in the rinse preceding the phosphating stage. You don't say whether this application specifically needs two rinses after cleaning. But if it doesn't, put the conditioner in Rinse 2 and your will get a better phosphate coating. The better the quality of the coating, the less chance that flash rust will form.
Secondly, is the phosphating bath being run according to the supplier's specifications? Your TA:FA ratio is about 11:1. For a spray application, I would run 12:1 to 18:1. This is a general range; the proper ratio is determined by the way the phosphating product is formulated.
Thirdly, is the contact time sufficient to deposit a uniform coating? If coating formation is incomplete, the flash rust may be occurring in locations where there is little or no coating.
Finally, is the accelerator concentration correct? Too little accelerator, and the bath is sluggish. Too much accelerator, the bath won't form any coating.
Also, your choice of sealer (presumed that it is applied after Rinse
4) will not matter if the flash rust occurs in Rinse 3.
Hope this helps.
- Naperville, Illinois
August 3, 2008
Thanks George!
By the way it is a spray application. We had already good results of phosphating and flash rusting was eliminated when increased the TA and reduced the FA, TA/FA ratio at about, 14/0.9 respectively. We also reduced the pressure from 1.5 bar to 0.8 thinking that misting in the spray helps create flash rust. We had maintained the contact time of 2 minutes in phosphating tanks.
We will try also to employ separate conditioning prior to phosphating and see if that will make a difference.
Regards,
- Riyadh, KSA
Q, A, or Comment on THIS thread -or- Start a NEW Thread