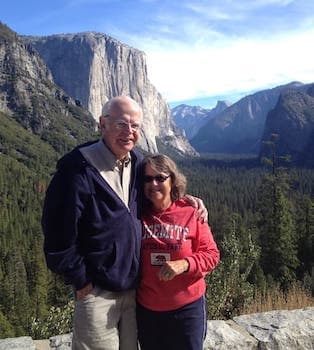
Curated with aloha by
Ted Mooney, P.E. RET
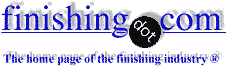
The authoritative public forum
for Metal Finishing 1989-2025
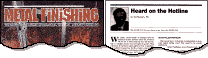
-----
Electropolishing SUS 304 Problem
July 30, 2008
We are a supplier of Chinese SUS 304 elbows to Canada and our client is having problems with electropolishing our products. The elbows are welded together with SUS straight pipe from a Canadian supplier and used in an automotive application.
The pipes are then electropolished by an experienced electropolishing company in Canada. This results in the straight pipes being perfectly polished and the elbows looking exactly the opposite. Severe surface
"Peeling" and dull areas all over the elbows as shown in the attached pictures.
We assumed low grade 304 but upon detailed testing found the Chinese SUS 304 material properties to fall within the standards.
C 0.092% / S <0.005% / Si 0.64% / Mn 1.04% / P 0.034% / Cr 18.24%
/ Ni 8.02%
The elbows are cold formed from straight pipe with a mild polish.
The welded pipes and elbows are soaked in a solution of 30% Nitric acid, 10% Ammonium Bifluoride and 60% water for approximately 2 hours prior to electropolishing.
The electropolishing company insists the Chinese SUS 304 material make-up is suspect and has never seen such a case after electropolishing.
I've searched many topics in your website and I was wondering if this is a possible case of "Pilgered Tube" or varying "Q" Factor? Would the "Q" Factor cause the voltage or current running though the pipe to fluctuate causing the problem?
Any suggestions of comments would greatly be appreciated.
304 pipe supplier - Kunshan, Jiangsu, China
A heat treatment may help to remove cold work stresses2000
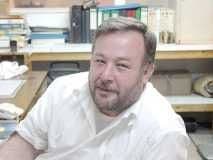
Khair Shishani
aircraft maintenance - Al Ain, UAE
August 12, 2008
Thanks for the reply.
Upon further study, the problem is actually coming from the heat treatment process. The elbows are heat treated to remove magnetism and cold working stresses.
We electropolished 2 elbows. One with heat treatment and one without. Interestingly, the elbows without heat treatment were electro polished fine. The heat treated elbow resulted in the same dull finish. The elbows are required to have no magnetism so heat treating is required unless anyone knows of other ways of removing magnetism from SUS 304 after it's cold worked.
Although we've narrowed down the problem, we can't get around it.
Any suggestions?
- Kunshan, Jiangsu, China
August 29, 2008
It's likely that the details of the heat treatment are inappropriate rather than the act of heat treating.
If it's to have it's normal corrosion resistance and mechanical properties, all 304 material has to be heat treated, and that applies to wrought pipe whether it's formed into pipe hot or cold, elbows that are coldworked into shape, components that are cast to shape, and so on. You may not see the straight pipe being heat treated, but it has been.
The only appropriate heat treatment for this material is heating into the range 1000-1100 °C and fast cooling (components of the section thickness that yours look to be would probably air-cool fast enough, but quenching into water is the normal cooling method). And 1100 is better than 1000!
If you use a lower temperature, although it may well remove the ability to attract a magnet, it will also cause undesirable and harmful metallurgical phases to form instead of having a microstructure of 100% austenite. Those other phases, dispersed in small quantity through the austenite, likely are what is causing your polishing problem.
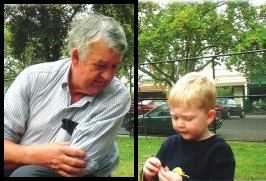
Bill Reynolds [deceased]
consultant metallurgist - Ballarat, Victoria, Australia
We sadly relate the news that Bill passed away on Jan. 29, 2010.
August 30, 2008
September 10, 2008
The heat treatment is performed at 1000 °C and air cooled.
We will try heating to 1100 °C and water quenching. I will post results.
Mr. Reynolds, thanks for your reply.
- Kunshan, Jiangsu, China
October 8, 2008
Success!
Followed Bill Reynolds' advice: heat treating at 1100 °C and water quenched.The elbows are being electropolished perfectly.
Thanks for the advice Mr. Reynolds and thanks to finishing.com
Jay Antonio
- Kunshan, Jiangsu, China
Q, A, or Comment on THIS thread -or- Start a NEW Thread