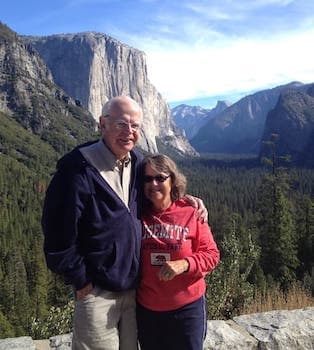
Curated with aloha by
Ted Mooney, P.E. RET
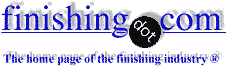
The authoritative public forum
for Metal Finishing 1989-2025
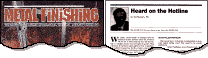
-----
Water immersion testing vs copper sulphate testing after passivation
Q. We are providing parts for interior in an aircraft and one stainless steel part exposed to cabin, not expected to be exposed to food or moisture, is machined and than passivated.
Our supplier suggests a copper sulphate
⇦ this on
eBay or
Amazon [affil links] test after passivation vs a water emergence test to save time. We have always specified water emergence testing after passivation and I wonder if I could accept deviating from this without any long term consequences.
Aircraft Interior Engineer - Garden Grove, California, USA
July 16, 2008
A. Both work well. There is normally a reason for selecting one over the other--Like the overhaul manual. An extremely sensitive test is the ferroxyl test. You probably have zero need for that.
I would do a split batch IE: a few parts from one process lot. I would even toss in a couple of unpassivated parts just to have a reference of each test. You may find that if it is a turned or ground part that the passivation is marginally necessary.
- Navarre, Florida
July 17, 2008
July 22, 2008
A. What grade of stainless is your part? I generally follow ASTM A967, which suggests not using the copper sulphate test for 400 series grades of stainless that contain less than 16% Cr. The reasoning is there is a risk of false failures. I use a hot water immersion test for such parts.
If you have a strong confidence in your process due to a history of a low failure rate in your immersion testing, and you're using a grade that's okay for the test, I don't see any real problem with switching.
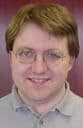
Ray Kremer
Stellar Solutions, Inc.

McHenry, Illinois
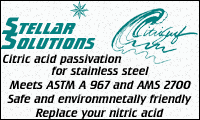
Water Immersion testing after passivation ASTM A380
August 22, 2013Q. Para. 7.2.5.1 states:
"Water-Wetting and Drying -- Formation of rust stains
may be accelerated by periodically wetting the surface with
preferably distilled or deionized water or clean, fresh, potable
tap water. The wet-dry cycles should be such that the sample
remains dry for a total of 8 h in a 24-h test period. After
completion of this test, the surface should show no evidence of
rust stains or other corrosion products."
But Para. 1.5 states:
"This practice provides definitions and describes practices
for cleaning, descaling, and passivation of stainless steel
parts. Tests with acceptance criteria to demonstrate that the
passivation procedures have been successful are listed in 7.2.5
and 7.3.4 and can also be found in Specification A967."
So when you got to ASTM A967 it states in water for 1 hour and allowed to dry for 1 hour. This cycle should be repeated a minimum of twelve times. (24 hours)
Which is correct 24 hours (12 cycles) or remain dry for a total of 8 h in a 24-h test period?
- Cypress, California, U.S.
A. Excellent question, Johnny. The main answer is that the two standards were written at different times, by different people, and for different purposes.
A380 is the older standard and involves mostly stainless cleaning but has a little bit on passivation. It does not actually require the use of a passivation test, but describes some anyway just for informational purposes, and mentions the ones in A967 similarly for informational purposes.
A967 was written as a direct replacement for the cancelled mil spec QQ-P-35 and uses the nitric baths and test methods from QQ-P-35 almost word for word. Passing one of the test methods on at least one part per lot is required for compliance to A967.
There are a lot of things between the two standards that are not in harmony with each other, and it is kind of an odd situation to have this kind of overlap between two different standards. The subcommittee has been working to bring them a little more into agreement, but there is always resistance to large changes to standards that are used by a lot of people, so mostly they are going to stay as they are as a matter of legacy issues.
If you are asked to comply to A380, you can do any test method you want, even one not listed, or none at all. If you are specifically asked to use the immersion test in A380, then do so. If you are asked to comply to A967, use one of the tests listed there, including but not limited to the A967 immersion test, or limited to it if it is specifically requested.
If you are not being required to comply to either standard and are just looking to run some tests for your own gratification, I would ditch the room temperature water immersion tests and run a boiling water immersion test in a few hours rather than 24.
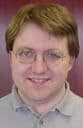
Ray Kremer
Stellar Solutions, Inc.

McHenry, Illinois
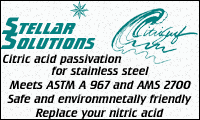
August 27, 2013
Q, A, or Comment on THIS thread -or- Start a NEW Thread