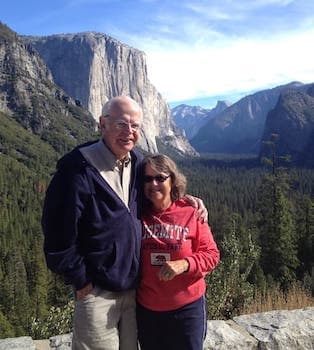
Curated with aloha by
Ted Mooney, P.E. RET
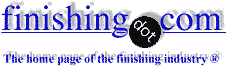
The authoritative public forum
for Metal Finishing 1989-2025
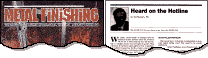
-----
Achieving of final tolerances of product after chromium plating
July 10, 2008
Hello,
my name's Janez and I work for automotive company. For one customer we are producing headrest rods. These rods are made from wire C9D EN
10016-2 and diameter of wire is 10,83 mm with tolerances ± 0,03 mm. After chromium plating we must have diameter 11 mm with tolerances
-0,05/-0,15 mm. For chromium plating we have next requirements: Ni
(min) 25µm and Cr (min) 0,4µm.
After chromium plating we achieve diameter 10,99-11,07 at the end of rods and sometimes also through entire lenght of rod. This isn't OK for our customer. Because of this I have some questions:
-what kind of parameters for chromium plating we must have, so we would achieve desirable values?
-what is a value for tolerance of chromium plating?
-how we define a diameter of basic material, so we could achieve desirable values?
Best regards
product designer - Novo Mesto, Slovenia
First of three simultaneous responses --
Nothing else counts except what your customer wants. Logic does not enter into the contest, but I see nothing illogical about your customer spec.
Your problem is very probably with the plater. The ends of the rod are very high current density areas and thus will plate a lot more than the middle. This is referred to as the dog bone effect. The solution is either thieves (robbers) or shields or a combination of both. It is very doable, but will take a bit of work to develop the racks if you do not have an experienced person doing it.
- Navarre, Florida
July 11, 2008
Second of three simultaneous responses -- July 13, 2008
hi , your problem is with the amount of nickel - if you need 25 microns on the part , you are very likely to have 2 - 3 times that amount on the ends (maybe more) because they are high current density areas . with a well designed jig / rack , with robbers for the end you will get a much more even finish .
also , beware that parts at the ends of the vat plate slightly faster than those in the middle .
don't over load the vat , and space the parts correctly and evenly
.
as for the chrome , there is only a flash , so I cannot see any problems .
try find a similar size test piece , and plate with your parts , so you can measure and record plating thickness and time it took (e.g., , if you got 12 microns in 15 minutes, you will know you can get 24 microns in 30 mins )
hope I've helped .
- Essex, UK
Third of three simultaneous responses --
Hex chrome has the worst inherent thickness distribution or throwing power of all chemistries. This means that under the same anode and cathode arrangement it will tend to build up thinner in LCD areas and to grow thicker at HCD ones than other baths like nickel, copper, tin, zinc, gold, etc. You have to fight against this undesirable property improving the control of the current distribution by means of auxiliary anodes and robbers. G. Marrufo-Mexico
Guillermo MarrufoMonterrey, NL, Mexico
July 14, 2008
Q, A, or Comment on THIS thread -or- Start a NEW Thread