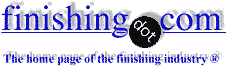
-----
Silver spray problems in the making of stampers for pressing vinyl records
July 9, 2008
Greetings, My name is Jay and I need some help with a silvering process used in making nickel stampers to press vinyl records. The silver appears to be slightly sticking to the lacquer when we separate the silvered father to start the matrix series process. This gives the father an uneven and rough surface that copied throughout the series and ends up as noise on the pressed records.
For those not familiar with the silvering process of a record, I will touch briefly to describe the process and where I believe I am having a problem. The original lacquer is washed in a soapy solution, rinsed with DI water, a wetting agent (saponin) is poured onto the part, DI rinsed, then the part is placed in a tub of stannous chloride solution (tinning solution), The part is then rinsed again with DI water and a silvering spray solution same as what they use to coat mirrors is sprayed onto the part.
That silvered lacquer is then put in a pre-plate bath that is nickel sulfamate 100F, Ph 3.95 to 4.10 and boric around
4 oz per gal. The bath is kept cooler to prevent any warping of the lacquered part prior to getting a good build up of nickel on it before the high amp plating begins. The part is plated at low amps, 4-8 for about 15 minutes then moved to a larger tank that is 140F, PH 3.95 - 4.10, boric 5.5oz per gallon. There is just enough wetting agent present to keep pits from forming due to hydrogen bubbles from the plating process. We finish plating the nickel to the silver layer overnight and end up with what we call the father of the plating series matrix.
When the father is separated from the lacquer, you will see separation marks on the lacquer. Under a microscope you can see tiny traces of silver left behind in the grooves.
Most times the silver looks like powdered sugar dusting the sidewalls of the grooves. This will end up sounding like hissing or crackling sounds on the record. SOmetimes I see actual chunks of silver left behind in the grooves, These will end up sounding like ticks and pops on the record.
It doesn't look like the silver layer is delaminating from the nickel. It looks more like when the silver was first applied the silvering spray did do a full chemical reaction and there is like a small 1st particle layer of non reacted silver that does not adhere to the rest of the silver as it is applied. From what I understand, the silvering chemicals are kept separate using a dual action spray gun and actually mix in mid air as they are sprayed out of the gun. Those chemicals in turn mix with the tin dropped out from the stannous chloride solution and form the silver layer. I think I can improve the sound of the record if I can get the silver layer to separate cleanly from the lacquer.
I have contacted the silver spray manufacturers but their applications are normally applying silver to something that is intended to stay on the part as a finished coating. I need to apply silver to a part and remove the silvered layer as a reverse image. The smoother the surface the better. I am thinking maybe we need some kind of a release agent or make the silver react better.
Does anyone have any ideas why the silver sticks, or can they explain this chemical reaction better so we can get an idea of where in the chain it is happening and how to fix this problem?
Thanks for any help you may be able to provide
Plating Manager - Canoga Park, California
I remember a client of mine who performs the same operations (electroforming the matrix for record pressing) utilizes a potassium bi(di)chromate dip for the purpose of a mold release. This is effective since it passivates the surface. I really do not wish to get into more detail because I would not want to give anyones "secrets" away.
Gene Packman- Great Neck, New York
July 14, 2008
First of two simultaneous responses --
Your actual silvering vendor should help you out but obviously is not doing it. I would try products from other suppliers that really understand your problem and sell you what you need, not what they want or have.
Guillermo MarrufoMonterrey, NL, Mexico
July 15, 2008
Second of two simultaneous responses -- July 15, 2008
As I understood the vinyl record industry, it was conventional to use silver spray to metallise the master and then electroform the nickel daughters from the mother master. In this process the silver remained adherent to the cut master and the nickel electroform was used to stamp the vinyl copies.
Am I correct in thinking you want to do a similar thing, but keep the silver as the top surface of the daughter stamper? This could cause problems; possibly with the silver surface being very soft and not lasting long, or with the oxidation of the silver to sulfides or oxides and also (possibly) the migration of silver into the nickel. I am not sure whether silver would migrate, but it is worth checking out.
To use silver as the press surface, you must get excellent release of the silver from the master, which is not very easy.
I used a similar process to that used in the record industry, but to metallise ABS with an adherent conducting coating. We too needed to have a good finish and found that one of the major problems was to get the correct balance of silver solution and reducer from the spray guns. If one was out of balance, the silver would be either too grey and oxidised or would be powdery and non-adherent because of too much reducer. It is essential to get a bright reflective surface and not to try putting too much down too quickly.
From your description, I reckon your problem is in the silver-reducer mixes, so perhaps you could give more information on the silver spraying process.
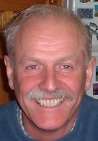
Trevor Crichton
R&D practical scientist
Chesham, Bucks, UK
October 3, 2009
Hey All
I am not sure if the answer to the silvering question has been found or the problem has been solved It is a little while ago, but it may help someone else
The description is close enough but I feel there are some gaps in there
So here is a short summary
1.It was common to spray the lacquers with a dilute solution of hydrochloric acid after the tin spray so as to stop the tin hydrolising The alternative was to mix tin and the acid just prior to use
2.Silver nitrate has to be AR grade as the normal stuff is not pure enough
3.Silver is to be mixed just prior to use
4.Dextrose and silver must flow out of the containers at the same rate into a non mixing spray nozzle If two guns are used the dextrose should be just above the silver Rotation is to be clockwise 14-18 inches from the face of the lacquer
5.Rotation speed is critical 78 RPM is ideal below that rivulet patterns appear above that centrifugal streaks
6.The silver always migrates to the master it is stripped in a 50/50 mix of ammonia
⇦ on
eBay or
Amazon [affil links] with peroxide (violent reaction)
7.The master is washed with acetone
⇦ on
eBay
or
Amazon
[affil links] Warning! Flammable!
to remove any particle of lacquer that may have remained It is than steam cleaned and air dried
8.Potassium Dichromate passivation is used after a very sort anodic clean The mother from this master is played back to hear clicks and pops DI water is used to wet the surface of the mother at play back A stanley knife blade can be used to remove them under a 60-100 x microscope the blade has the right angle to the cut, Need a steady hand
9.Egg albumin or fish glue can also be used as a separating medium
10.Stampers produced from a mother processed with the above steps are free of clicks and pops
In my view most of the clicks and pops are in the cut on the lacquer If lacquers are not kept under a constant temp after they are cut, a domestic refrigerator is fine, else they grow "horns" however fine These tend to accumulate more silver therefore more nickel in the electroforming process giving rise to unwanted noises on the final record
We have many "recipes" on the subject dating back to about 1962 and there are as many variations as there are recipes However we use a procedure that is a mixture of a few which work consistently Happy to post one we know it works if the issue is still not resolved
The things we learned and know over many years are:
A. Always mix the silver just in time
B. Everyone will tell you that tin as a stock solution last's forever It is not so about 7 days maximum in the refrigerator
C. Same for the D Glucose reducer 7 days max in the fridge
D. AR grades for all your chemicals
E. Depolarised Nickel anodes with no more than 5-8 g of N chloride in the bath, reasonable throwing power while keeping ductility up and tensile stress to a minimum
F. About 25% or less of what Barretts recommends for SNAP is enough add traces of it only if you see pitting around the fixing point Nothing else!
G. Preplating at the lowest setting available around 1 V for
10 minutes a further 15-20 minutes at 2 V and than build up
Cheers
- Melbourne Australia
March 9, 2011
Greetings,
Many thanks for the responses. We finally figured out the pre-plating current was too low at the start. I measured the current at the start of each part. We should be in the 5 Amp to 10 Amp start range. On a few parts due to poor connections we measured starting amps of 1 and 2. To me, that is dummy plating. So I have my silver layer and depositing a smut layer from the low amp dummy plating until the layer gets thick enough to raise the amps and start plating the nickel. We cleaned up all of the parts hangers, replaced all of the hardware on the racks and now we check each part as it is loaded for proper amps at the start of the cycle. Since we have established this procedure, we no longer see the silver deposit remaining on the lacquers after the silvered/nickel masters are separated from them.
Thanks so much for the responses.
Jay
- Canoga Park, California U.S.A.
Q, A, or Comment on THIS thread -or- Start a NEW Thread