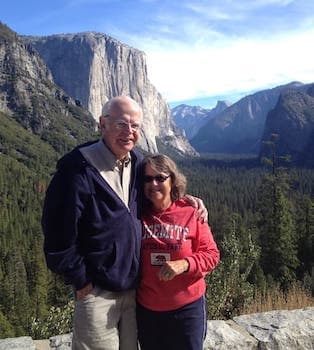
Curated with aloha by
Ted Mooney, P.E. RET
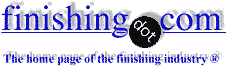
The authoritative public forum
for Metal Finishing 1989-2025
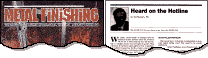
Thread 492/50
Anodized parts, part mark won't cure
July 3, 2008
We've had some problems lately bringing a new plating supplier aboard, one of which involves part marking. Nearly all of our parts require anodizing, most often in black or red colors, or colorless. After anodizing, the parts get marked with Markem type 7224 black ink which requires a 15 minute cure at 300°F.
Black and red dyed anodize parts are having no problem. On the clear anodize, after the curing process the ink will wipe right off without much effort. If we scratch up the surface to be part marked a bit, it will cure just fine. Obviously this is not ideal and it leads me to believe this has something to do with the seal.
Plating supplier tells me they are only using a dichromate seal on all of these parts, dyed or clear. We suggested trying a nickel acetate seal, plater says this won't help. Also have told me they have never seen anything like this before. I requested some various test panels (dyed/clear, sealed/unsealed) and all of them passed with flying colors. Yet we still find that the part mark will not cure on clear anodize and will always cure on colored; and the plater continues to insist there is no difference between the colored and clear processes.
Any help, experience, or advice would be fantastic, as I don't have many more ideas if the plater is going to continue to suggest that there is no process difference.
machine shop QA Mgr - Denver, Colorado
publicly reply to Domenic Sideri
In offering some advice I am assuming that when you say the ink does not cure, you really mean it is cured but won't adhere. If I'm wrong, and it actually does not cure, then the advice would be different!
I think that you are right that sealing is the problem. It is well established that good sealing is bad for subsequent adhesion of paint and inks. I know that the anodizer says that he is applying the same anodic film
thickness to colored and clear aluminium. But, has he check the thickness? Deep colors need a thick anodic film to get enough dye absorbed. A thinner film would seal more completely if the sealing time was short. A dye stain test should help here. Although I would normally advise a formal test, simply applying a marking pen and then washing off could provide useful information. Ask the anodizer to reduce the sealing time to see what effect it has. Though if you do this, consider the possible effect on corrosion resistance or other performance criteria.
I agree with your anodizer that nickel acetate would not help. It might do such a good sealing job that everything fails!
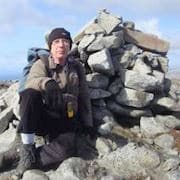
Harry Parkes
- Birmingham, UK
July 10, 2008
publicly reply to Harry Parkes
Q, A, or Comment on THIS thread -or- Start a NEW Thread