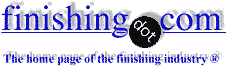
-----
Reduce CO2 content in inlet mix bed polisher
July 1, 2008
Q. Thanks for your attention,
My question is: our plant has 3 mixed bed polishers (MBP). 2 online, and 1 standby.
There is cation and anion resin in mixed bed polisher, both of them used in one vessel.
My problem is our MBP always service under 24 hours, with end conductivity more than 0.2 mS/cm. It make always reagent and uses more chemical.
The impact is we must replace all resin in one vessel with new.
But it's not giving best solution. Service time of the MBP back to under 24 hours.
We have made laboratory analysis and the result is there are 10.63 mg/l as CaCO3 (design 2.22 mg/l as CaCO3).
So what should we do to reduce CO2 content in inlet of our MBP?
Is there any treatment for reduce that CO2 content?
I hope you will send me the answer, thanks for Your kindness.
Lelywaty
employee - Bontang, East Kalimantan, Indonesia
A. I seriously doubt if CO2 is your main problem. It is more likely the high amount of calcium in your makeup water, i.e., no calcium, no calcium carbonate.
I would strongly look at using a Reverse Osmosis [RO], unit in front of the DI line.
Lacking that, I would put a single resin tank in front of the mixed bed tanks to remove the calcium. It is cheaper and easier to regenerate.
A water softener may work as it replaces calcium with sodium ions which may or may not work, depending on your exact resin.
- Navarre, Florida
July 3, 2008
July 15, 2008
Q. Dear sir,
First I want to say thanks a lot for your responding, but I'm sorry there is a mistake with my email, actually laboratory analysis shows there are CO2 9.35 mg/l (9.35 mg/l = 10.63 mg/l as CaCO3, with design 2.22 mg/l as CaCO3). So CO2 content in makeup water of Mix Bed Polisher (MBP) is out of design. I'm sorry for this mistake.
It's right that my main problem is CO2.
Can I have explanations how to reduce CO2 content that out of design in inlet of our MBP?
Because as I know RO used for reduce TDS, that can't reduce CO2.
My next question is: How about if I used degasifier, it is enough to reduce CO2?
Can I have explanations about degasifier?
I hope you will send me the answer, thanks for Your kindness.
- Bontang, East Kalimantan, Indonesia
A. First, I think that you are not correct to say that the CO2 is the problem. A MBP will drop to .2 mSm by the DI bed having absorbed more of either the cation OR the anion and those normally come from dissolved salts in the water, sometimes incorrectly referred to as hardness. Hardness of the water is a factor. Also, the amount of water that you put thru the system is a bigger factor than the time.
Now, for a solution to the CO2 problem. Put an appropriate tank in front of the DI system and bubble nitrogen thru the water at a slow rate and maintain a N2 head on the tank rather than air. Your CO2 will virtually disappear. High pressure tanks with pressure reduction will work very well. In my area, liquid nitrogen in a large SS dewar is more cost effective.
It does not take a high flow rate. You can put a flow meter on it, or just learn what bubble rate works. You can slow the rate down considerably at night or whenever the system is not in operation.
- Navarre, Florida
July 15, 2008
A. Hello
I am a new visitor and I am a student.
In answer of question about CO2 problem: use of degasifier column is better, and it is not necessary to use nitrogen for desorption of CO2. You can use a simple blower for it.
student - aleshtar, lorestan, iran
May 30, 2016
Q, A, or Comment on THIS thread -or- Start a NEW Thread