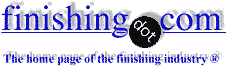
-----
Silver Plating - Anti-Tarnishing Specs or Standards
We are experiencing problems with a silver-plated electrical contact switch that is intermittent due to tarnishing. The supplier performs (and apparently passes) sulfidization testing using 3 ppm H2S at 40 degrees C for 96 hours.
My first question: is this a sufficiently stringent test? I have located several other test methods (e.g., EIA-364-TP65A and IEC-68-2-60) that recommend several corrosive gases (HS2, NO2, SO2 and Cl2) in the test chamber (though at much lower concerntrations
~10-100 part per BILLION range). They also recommend humidity levels of ~70% RH. Do multiple corrosive gases at low concentration but at high humidity induce tarnishing more readily than a high concentration of a single corrosive gas, H2S, with no humidity?
My second question: are there industry standards for anti-tarnish plating of electrical applications that are RoHS compliant we could recommend for this supplier? (I know some anti-tarnishing chemistry involves chromate, though I am not sure if it's Cr+6).
Thanks in advance!
OEM of electronics products - Framingham, Massachusetts
June 30, 2008
Bare, clean silver will tarnish. You can protect from tarnish with a dip in any hex aluminum chromate conversion chemical, and you can get lesser protection from a dip in a tri-valent chromate solution; but theh when you make and break contact a few times , you have scraped off the chromate, then, well, again, bare clean silver tarnishes.
Siver is a great "conductor" but a lousy contact for low voltage.
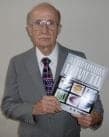
Robert H Probert
Robert H Probert Technical Services

Garner, North Carolina
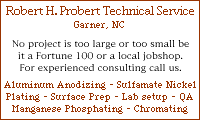
July 2, 2008
Q, A, or Comment on THIS thread -or- Start a NEW Thread