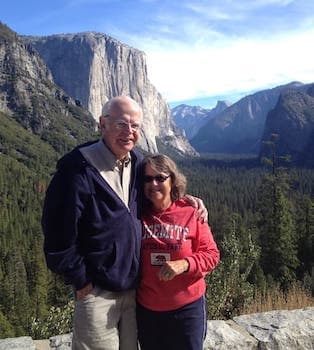
Curated with aloha by
Ted Mooney, P.E. RET
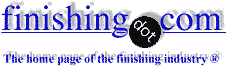
The authoritative public forum
for Metal Finishing 1989-2025
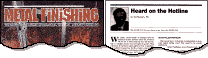
-----
Galvanizing buildup on MIG wire weld areas

for Engineers, Shops, Specifiers
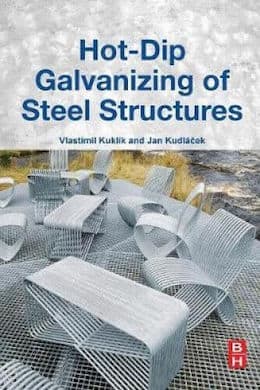
avail from eBay, AbeBooks, or Amazon
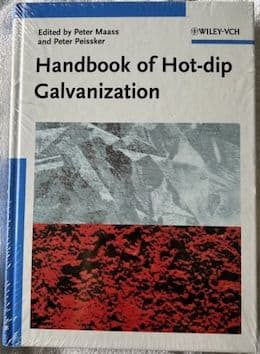
avail from eBay, AbeBooks, or Amazon
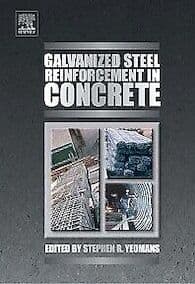
avail from eBay, AbeBooks, or Amazon
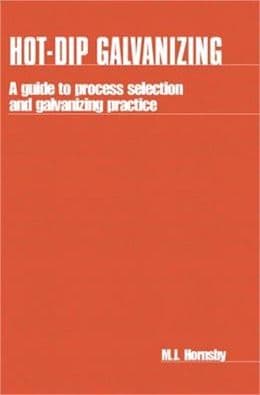
avail from eBay, AbeBooks, or Amazon
avail from Amazon
"User's Guide to Hot Dip Galvanizing for Corrosion Protection in Atmospheric Service" by NACE (1997 only rarely avail.)
avail from AbeBooks, or Amazon
(as an Amazon Associate & eBay Partner, we earn from qualifying purchases)
Q. We recently completed our first galvanized steel tube project. On our mitered corners we grind them flush or a number one finish. When we received the rail there was some buildup of zinc on the finished corners. The galvanizer told us it was due to the different content of silicon in the steel and the MIG wire. By lowering the silicon content of the wire it should alleviate the problem or most of the problem. Can someone please give me some input on this?
Thanks,
fabricator - Pilot Point, Texas
June 30, 2008
A. The thickness of a galvanized coating is dependent on several factors. The steel chemistry (particularly Si and P) is one of them. It's very common for the area above a weld to be raised after galvanizing even when ground perfectly flush before galvanizing.
Modifying the weld filler (MIG wire if MIG welding, electrodes if stick welding) to a low Si content wire can alleviate this, but most people don't bother.
The raised portion is only the coating thickness. The steel underneath is unaffected. If you were to strip off the galv, (acid for example), then you'll find the steel just as it was after grinding flush.
An alternative to finding a low Silicon wire (not easy, though low Si welding rods are available), is to file the extra coating off. This might be practical if there's only a small quantity of material, or if only certain parts of the item are critical. Use a smooth file and file parallel to the coating surface until you have a smooth joint as it was prior to galvanizing.
If you have many items to do, this might not be a cost effective method.
Galvanizing kettles are made of very low Si steel, and are welded with very low Si rods. It's these types that will not produce this effect.
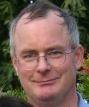
Geoff Crowley
Crithwood Ltd.
Westfield, Scotland, UK
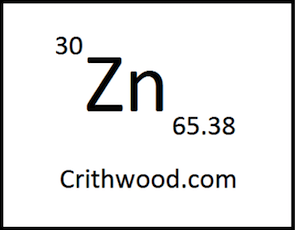
Q. We are fabricating tapered RHS posts which require a welded joint down the middle. This joint is ground smooth after fabrication. When it is hot dip galvanised the joint raises quite considerably. This is a feature of the galvanising process as the weld will take up a lot more zinc. We need to powdercoat these afterwards and the now-visible welded seam is not aesthetically pleasing.
We could grind down the welded joint after galvanising but we don't want to impair the galvanise protection. This problem was raised before on this forum and it was suggested that the silicon content of the wire causes this to happen and to get wire with low silicon. I'm not aware of availability of low silicon wire. Any thought on how you could overcome this problem?
Thomas McCormack- Westmeath Ireland
March 1, 2024
![]() |
A. This problem is seen frequently by galvanizers everywhere. ![]() Geoff Crowley, galvanizing consultant Crithwood Ltd. ![]() Bathgate, Scotland, UK ![]() A. Thomas, - Ballarat, Australia March 4, 2024 |
Thanks Geoff,
Agree that its important to match the wire with the material.We will try different wires and see if the results improve.
Thanks Andrew,
I have contacted my welding wire supplier but they are not aware of availability of low silicon but are checking it further. I expect that careful grinding down of the galv on the weld might be an option but its very time consuming and its easy to grind down too much.
Regards,
Thomas
- Ireland
March 14, 2024
Q, A, or Comment on THIS thread -or- Start a NEW Thread