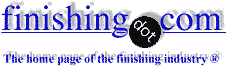
-----
WHY does this rust occur?
I work on a production line that welds structual (carbon) steel using a mig welder. After the I-beams are welded they are hung on a chain conveyor and run thru an open gas flame oven to help clean and prefheat before being painted. The steel is between 140-170 F prior to being painted using a waterbase primer, . The paint dries in about 10 minutes. My question is , "The weld and the area about 2 inches on each side of the weld eventually rust when exposed to moisture", What causes the rust along side the weld?, and can it be prevented w/o sacrificing the open flame.
Nick Nickelsencoatings tech - OKC, Oklahoma
June 30, 2008
Hi, Nick. The rusting in that area can probably be reduced by sandblasting the welds because the weld area is presently a galvanic hotspot due to stress. However, if I understand you correctly. you are doing no pretreatment at all? All areas of all of the components will rust quickly if exposed to moisture (although quickly is a relative term).
Regards,
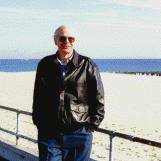
Ted Mooney, P.E.
Striving to live Aloha
finishing.com - Pine Beach, New Jersey
July 1, 2008
Thanks for the response Ted, but due to the volume of pieces I process sandblasting is not an option. The steel is normally only exposed from 10-30 days before erected and the rusting has only become a problem (probably alot more noticeable) since we changed from red ox primer to gray primer.
Nick Nickelsencoatings tech - OKC, Oklahoma
July 3, 2008
July 4, 2008
Hi Nick,
I think you have answered the cause of the problem yourself -
"the rusting has only become a problem (probably more noticeable) since we changed from red oxide primer to grey primer".
You may also have noticed that the rusting is worse since changing from a solvent based primer to a waterborne system - that is if this did occur. The red oxide primer would not show the noticeable difference in colour (rust/primer) that a grey primer would. Secondly, the RO primer may have contained anti corrosive pigments (most do) whereas grey primers are usually formulated only using titanium dioxide
⇦ on
eBay or
Amazon [affil links]
and black pigment, neither adding corrosion resistance properties to the material. Suggest to your purchasing dept that they request your paint supplier for a weather resistant coating, not just a primer.
Birmingham, United Kingdom
Both the red and gray primers are water-base acrylic emulsions. There were no rust inhibitors in the red and we have just started using one in the gray. I just wonder if the red oxide pigment in the one primer has some characteristics that combat the rust or inhibit the corrosion process?
Nick Nickelsencoatings tech - OKC, Oklahoma
July 8, 2008
January 20, 2009
I will reply to my own question and perhaps help someone else. The rusting that took place around the welds did so for several reasons; 1.The galvanic reaction(rust) that takes place when 2 different metal are welded and not treated. Since I used a waterbase primer the "water acted as a surperb conductive. 2. Mill scale in most cases is corrosive and did contribute to the rust and eventual peeling. 3. Red Oxide does offer rust inhibiting properties since it reduces the electrochemical activity of the surface ,i.e red oxide primers are better for resisting rust than gray primers.
Nick Nickelsencoatings tech - OKC, Oklahoma
Q, A, or Comment on THIS thread -or- Start a NEW Thread