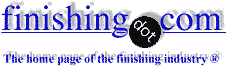
-----
Can Zinc-Nickel plating be applied to INSIDE of already ASSEMBLED pipe spool for seawater conduction?
PROBLEM: Firewater piping on Offshore Platforms needs to conduct SEAWATER. This seawater is from tropical waters where Oxygen content and normal salts make it highly corrosive, both inside the wet (and stagnant) 10" header section up to the deluge valve, and also in the usually dry smaller pipe circuits to the spray nozzles and hydrants, where alternating wet-dry cycles cause even harder attack conditions. To try to solve this corrosive damage, where the complete piping has to be replaced every 3 to 4 years (even using heavy pipe schedule and thickness), some people suggest using Zinc galvanizing
(electrodeposition type) to plate the inside of the pipe.
Please mention the possible advantages, disadvantages or plain difficulties of pretending to get adequate corrosion protection to the INSIDE of piping spools that are already assembled, for seawater inmersion. The idea some engineers suggested, is to try to get the plating to reach 25 to 30 micrometers with Zn-Ni or using Zn-Ni-Co MIL-P-85748 Spec, to be able to get 2000 hours of salt spray chamber test per ASTM B117.
(I believe that a pipe Spool, say 18 by 6 by 5 ft with a couple of 90 degree elbows and/or other pipe fittings is NOT going to be easy, not very expensive or even feasible); that the Zinc-Nickel or Zn-Ni-Co plating could even withstand the tropical seawater attack. But we need to analyze the real difficulties involved. your technical opinion will be highly appreciated. Then, a second question is: What is a better way to protect the seawater piping, since other alternatives like fiberglass reinforced pipe suffers from other shortcomings. TIA.
Project Manager, engineering - Mexico City, MEXICO
June 27, 2008
July 1, 2008
Plating on the inside of a pipe requires an internal anode which is not practical in your case.
One possibility would be to High phosphorous Electroless nickel plate it by pumping the solution thru the pipe. Because it would take about
3 hours and EN is temperature critical, the entire coil would need to be in a water bath or a heated room to about 190F.
If it were me, I would look into teflon lined pipe. It is not cheap, but it is durable and can be assembled with normal shaped pipe fittings. It is an off of the shelf product with virtually no special assembly tools or techniques needed.
- Navarre, Florida

Q, A, or Comment on THIS thread -or- Start a NEW Thread