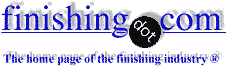
-----
Micro cracking of Cr plating on calendering roll
June 25, 2008
Hi! May I have you guys help to figure out the micro cracking of Cr plating ?
I have been treating Cr plating to calendering roll for plastic extrusion.
The process are Cu plating with 500um thick, Diamond turning to 100um depth and finally Cr plating 3~4um thick.
I could not find the micro cracking after Cr plating, but, the cracks became start with operation at 150'C and severe with time after time. This is what I have a difficulty.......
So now I'm considering "Baking heat treatment at 190'C, 12hrs" as a countermeasure. Because I think that accumulation of Hydrogen on the Cr plating could be one of the root cause.
I wonder this could be proper action to clear this kinds of micro cracking related to Cr plating.
BTW, I think somehow the induced residual stress of Cu plating after diamond turning might be one of the reason to explain the cracking with time during operation.
Could you guys let me get your suggestions or advices on this ?
Best Regards,
product designer - Korea
First of two simultaneous responses --
Your proposed heat treatment is OK but I doubt it will solve your problem. Chrome has an intrinsic high internal stress because it shrinks during deposition. This coupled with a ductility of less than 1% leads to cracks. Please remember that the coeficcient of thermal expansion of chrome is much lower than that of copper or steel, so it will suffer more. You need to induce a compression stress in the chrome plate by adjusting temperatures during your plating process. You probably also need to improve the adhesion.
Guillermo MarrufoMonterrey, NL, Mexico
June 27, 2008
Second of two simultaneous responses -- June 29, 2008
Dear Smith ,
I am afraid you have it wrong.
Firstly the micro cracks are never visible with a naked eye after H/c plating, nor do they show up after some time.
If you see some cracks after some time I am afraid you have not done it the right way.
1.Try grinding your rolls to a good Ra insted of turning. Turning leaves surface burrs which can hamper your chrome adhesion.
2.How thick is your chrome , 3-4 microns as you mentioned seems to be incorrect. If you are going above 100 microns try etching a little bit for better adhesion, and don't forget to regrind it to remove the surface irregularities.
3. Lastly as you know a picture speaks louder than words.
Try sending me a pic maybe I can feel you problem better and advice accordingly.
ALL THE BEST
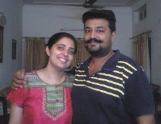
Vikram Dogra
Irusha India - Chandigarh, India
Hi.
All chrome over 2,5 µm is microcracking, because of the hydrogen in the plating steps. And that should it be also to protect the substrate from corrosion, by alots of chanels in the chrome, who make a big anodic corrosions protection for the materia substrat. One way to not get microcracked deposit if you can try to use pulse plating, there you get the deposit to avoid hydrogen in the migration to the substrat. I know that plating people have different knowledge about micro and macro cracking chrom deposit. What do you think you have?
Best regards,
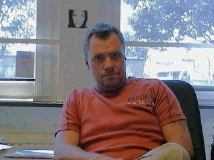
Anders Sundman
4th Generation Surface Engineering
Consultant - Arvika,
Sweden
August 8, 2008
Q, A, or Comment on THIS thread -or- Start a NEW Thread