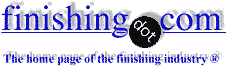
-----
How about iron plating instead on nickel plating between copper and EN?
I am interested in the possibility of iron plating vs. nickel sulfamate plating our component parts prior to high phos EN. Of course, cost is the primary motivator in doing so, but I have very little information or experience with iron plating. Our current process involves a cyanide copper strike over a copper pan that has copper tubing soldered to it, followed by a nickel sulfamate strike and a finish plate of high phos EN.
Jerry WendtPlating shop employee - Manitowoc, WI
June 23, 2008
Hi, Jerry. It's good to see people investigating alternatives considering the high cost of nickel. But iron plating is a difficult process of limited applicability, partially due to iron's propensity to move to different oxidation states incompatible with proper plating.
Is there a reason you can't "jump start" the electroless nickel directly onto the copper?
Regards,
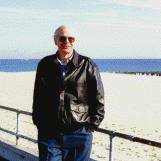
Ted Mooney, P.E.
Striving to live Aloha
finishing.com - Pine Beach, New Jersey
June 24, 2008
First of two simultaneous responses --
Years ago, we plated a copper heat sink with a Woods Strike, followed by a heavy build sulfamate nickel for dimension and EN for chemical resistance. We used the Woods strike because it helped and it was in the plating line. Avoids the cyanide step.
James Watts- Navarre, Florida
June 25, 2008
Second of two simultaneous responses --
I realize that this could be done, but I think the culture shock might be too much for many of the longtimers to get past. I may have to try this but my concern is the amount of current it will require to accomplish this on a repeatable basis. Our square footage can vary from 0.05 sqft/gal to around .25 sq ft/gal. pretty low loading rate for EN. Any suggestion on where to start?
Jerry Wendt- Manirtowoc, WI
June 26, 2008
First of two simultaneous responses --
The most common iron plating solution contains hydrochloric acid and operated at high temperature.
There is a sulfamate iron plating process. It is similar to sulfamate nickel, except that iron is easily oxidized to ferric that can precipitate if the pH gets too high. And there can be a ring of iron around the inside of the tank at the solution level. Particles can cause roughness, but can be controlled if good control of the solution is practiced and adequate filtration is used. However, iron does not have the corrosion protection that nickel has.
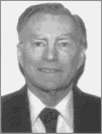
Don Baudrand
Consultant - Poulsbo, Washington
(Don is co-author of "Plating on Plastics" [on Amazon or AbeBooks affil links]
and "Plating ABS Plastics" [on Amazon or eBay or AbeBooks affil links])
June 27, 2008
Second of two simultaneous responses --
It takes virtually no current at all, Jerry. In fact, I have been told that all you really need to do is connect iron to the rack, although I've never actually seen that done and don't really understand how it would work. But as for the "sparking" to jumpstart electroless plating on non-catalytic substrates, I've never actually "studied" it; rather, all I've seen is the plater momentarily attaching the rack with an automobile jumper cable, with the other end of the cable connected to a handy busbar.
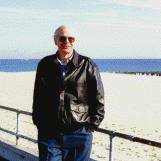
Ted Mooney, P.E.
Striving to live Aloha
finishing.com - Pine Beach, New Jersey
June 28, 2008

Q, A, or Comment on THIS thread -or- Start a NEW Thread