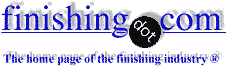
-----
Adverse conditions in Hydrogen generator diodes causing problems with metal corrosion.
June 21, 2008
Hello, I am an individual with limited technical knowledge, but I am over flowing with determination. With Gasoline prices soaring, I am taking on the challenge of making hydrogen on demand to assist with gas mileage. My goal is to overcome the obstacles I have seen so many others faced with. One of these challenges are heat build up and water pollution making their systems inconvenient to operate. I am looking for some advise in finding the best metal available for the electrical contact plates in the Hydrogen Generator. This is where the heat and pollution is coming from.
Producing hydrogen through electrolysis, (passing water between a negative and positive charge to separate the hydrogen from the oxygen), is creating a problem with the materials being used as the electrical contact plates. This process brings out the impurities of the metals I have been using. Trying to keep cost down, I have used aluminum, copper, stainless steel 300 series, tungsten and 99% nickel. The Tungsten held up well, but a 5x6 plate 1/16 thick cost approx.$300 and a total of 6 plates will be needed. The Nickel is holding up well but the test is on going.
It has been suggested I use the 904L stainless, or titanium. I have not priced either of these as of yet. I have already incurred a lot of expense doing the trial and error routine. I am hoping someone will know the best metal to use for this application without just purchasing more metal and hoping it works.
I am using 14 DC volts around 2 to 4 amps. The metal is submerged in water. I am using distilled water adding distilled vinegar
⇦in bulk on
eBay
or
Amazon [affil links] as electrolytes to bring the amps to the desired level.
Private inventor/user of metals/fabricator - Bolivar, Missouri, USA
The reason your metals are breaking down is that you cannot run more then 3.0 volts through your cathode and anode (you call these diodes). If you notice, only the positive (anode) is breaking down.
David
- denver colorado usa
July 31, 2012
Q, A, or Comment on THIS thread -or- Start a NEW Thread