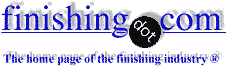
-----
Hardness required in nickel sulfamate deposits...!
June 12, 2008
Dear Sir,
We are using bright nickel bath to plate nickel onto stainless steel circular discs. But we recently decided to shift to Nickel Sulfamate bath because of lower plating times and higher current efficiencies. After taking the plating we found that the plating was low stress but we want a greater hardness in the plating. Could you please suggest any additions to the bath so that we can get nickel deposits with greater hardness. We are operating at 50C and the concentration of the bath is 200 g/l Ni, 30 g/l boric acid, pH is maintained between 4-4.5 Also someone has suggested the use of Potassium Bromide (about 0.05 g/l) to increase the hardness of the deposit, how far can this be useful I have my doubts? Please suggest ways to improve the hardness.
Thanks & Regards
Plating shop employee - Delhi, India
Hi, Anant. You probably know the things I am about to say, but your inquiry looked like a good springboard to help readers who review these threads as a learning tool. The reason you are able to get lower plating times and higher efficiencies with sulfamate is that it chemically allows a higher concentration of nickel than other baths. Stress and hardness are not the same thing, of course, but there is a strong correlation. Softness comes largely from a large open grain structure and hardness comes from a small tight grain structure. But this tight small grain structure is far more prone to be stressed.
In terms of operating conditions, higher plating rates (if achievable without burning) will usually lead to harder deposits, as will a small addition of saccharin. The ideal way to achieve hardness, however, may be to switch to a nickel-cobalt alloy bath.
Regards,
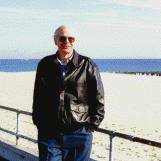
Ted Mooney, P.E.
Striving to live Aloha
finishing.com - Pine Beach, New Jersey
June 12, 2008
First of two simultaneous responses --
The idea of switching to Nickel-Cobalt alloy seems to be a good one. Could you please advise on the ideal composition of the bath for such alloy. Also I found out that Cobalt Sulfamate is not easily available in India, is there any other way to make additions of cobalt. In the meantime testing with saccharine.
Thanks again
- Delhi, India
June 14, 2008
Second of two simultaneous responses --
Add some sodium saccharin. The amount you need will be very low (less than 3g/l) but the hardness is very sensitive to the amount added. You do not give any information on what you need, so we cannot give you an amount
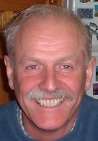
Trevor Crichton
R&D practical scientist
Chesham, Bucks, UK
June 15, 2008
Hi, Anant. Sorry, I'm not able to do that. I know some electroformers who have been working for years on these alloy compositions and (to my knowledge) they are not generic knowledge in the way that nickel sulphamate electroforming is. You can probably do a literature search and get some introductory information on results from different operating conditions, but I think you would need to either license the technology or do some development work; I don't think you'll find full operating conditions and compositions in the literature. Good luck and sorry.
Regards,
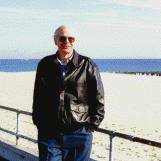
Ted Mooney, P.E.
Striving to live Aloha
finishing.com - Pine Beach, New Jersey
June 16, 2008
June 16, 2008
There are a number of references available for plating the alloy. It does require more testing to maintain the balance of ions so that it plates out the desired and consistent alloy. It is also dependent on temperature and current density. If I remember correctly, you use nickel anodes and add the cobalt salt to keep those ions up. A long time ago, I read an article where they varied the baskets of cobalt chips and nickel chips. I think that they even used different voltages/amperages also.
Here is another thought-Go to a pure cobalt plate which is even harder and has a nicer whiter color. It is more expensive but massively simpler.
Be extremely careful with saccharin. a tiny bit too much and the internal stress becomes horribly negative, to the point of flaking. But it works.
- Navarre, Florida
Nickel-cobalt alloy deposition has been around for many years. It is an interesting system because although cobalt has a higher redox potential, it is has a much higher rate of consumption. This s due to one of the intermediates produced in the deposition process. There are numerous ways of running the nickel-cobalt bath, but the simplest is to dose it with a soluble cobalt salt. You can use nickel and cobalt anodes, but you need different currents applied to them, to control the relative rates of dissolution. The bath needs very careful monitoring and process control, as the effects of cobalt can be quite dramatic.
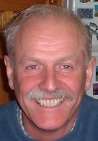
Trevor Crichton
R&D practical scientist
Chesham, Bucks, UK
June 17, 2008
Thanks, Trevor. Can you then point Anant to a particular article that would give him some operating parameters to start with? I see one from 1966 that sounds promising: "Electrodeposition of Nickel Cobalt Alloy: Process Variables & Physical Properties of the Deposits", by Endicott and Knapp, Plating & Surface Finishing, Vol. 53, pp. 0043 - 0060. I guess I overstated the proprietary nature of this process before checking the literature; it appears there are a good number of articles on it.
Regards,
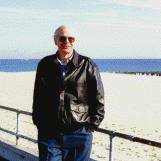
Ted Mooney, P.E.
Striving to live Aloha
finishing.com - Pine Beach, New Jersey
June 17, 2008
June 20, 2008
For general texts, I like Brenner's book
"Electrodeposition of Alloys"; it is a bit old now, but there is a lot of excellent and often forgotten information in it. NiDI also do some good monograps that are worth looking at - try "Electrodeposition from nickel sulphamate solutions"
- by RAF Hammond; this contains an excellent section on Ni-Co co-deposition. There is another NiDI monograph called "Additions to sulphamate nickel solutions" by Dr S Alec Watson that gives a good review of the background and some process details for Ni-Co alloy deposition. All of these are quite old (over 15 years and in some cases even older, but I make no apology for using them, because they contain a lot of information that is of great importance to the modern electroplater - it is all too easy to pick a solution off the shelf and use it, but when it goes wrong people don't know what to do because they haven't bothered to find out anything about its characteristics.
For those intent on just using modern sources, try Lupi and Pilone's paper in Minerals Engineering (p 1403, 14(11), 2001) or Marikkann et al in Journal of Alloys and Compounds pp.332-336, 438(1), 2007. A paper on Ni-Co pulse plating was published in Plating & Surface Finishing p274 vol 8-, 2007.
However, I would recommend going back to the basic literature to get a full understanding of what you are doing.
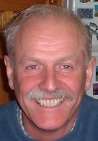
Trevor Crichton
R&D practical scientist
Chesham, Bucks, UK
Q, A, or Comment on THIS thread -or- Start a NEW Thread