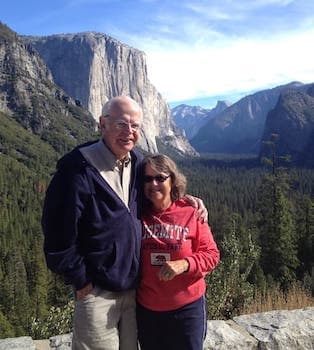
Curated with aloha by
Ted Mooney, P.E. RET
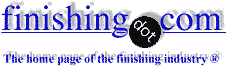
The authoritative public forum
for Metal Finishing 1989-2025
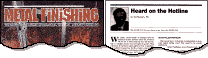
-----
Nickel plating of bus bars -- thickness questions, burned plating issues
Q. In a nickel electrowinning cell, the sulphate solution contains 3 g/L chloride. In an effort to protect the anode header bars from corrosion, it has been suggested to plate the cold-rolled steel with nickel. Header bars are 10 mm x 100 mm x 1400 mm. How thick should the nickel be plated? Is there another (perhaps more cost effective) option?
Jason BornsteinEngineering designer - Mississauga, Ontario, Canada
June 10, 2008
A. You need to have a non-porous engineering coating on the buss-bar. I would suggest that as a basic minimum, you have at least 5 microns.
- This will be sufficient to minimise attack of the substrate through pores, but may not be adequate for any mechanical damage that may be incurred during plant operation. For a safe thickness, I would suggest something around the 25-35 micron range. You may also benefit by using a duplex nickel, where the first layer is about 10-15 microns and the second is 15-20 microns thick.
- You would also benefit from looking at the plating specifications for the automotive industry, but unfortunately I do not have these to hand.
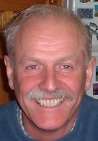
Trevor Crichton
R&D practical scientist
Chesham, Bucks, UK
July 28, 2008
A. I am not entirely sure what you mean by 'anode header bar'
If any part of the anode is in contact with the solution, the nickel plating will dissolve and plate out onto the cathode.
I would consider replacing the anode bar with copper. This will reduce the voltage drop and hence the running cost.
For electrowinning, I would expect the crude nickel anode to be suspended from a titanium hook or in a titanium basket. Most other materials will be attacked.
Presumably you are also collecting the anode slimes to recover any precious metals they contain.
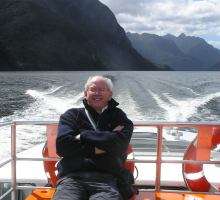
Geoff Smith
Hampshire, England
July 29, 2008
A. Geoff,
Look at the dimensions of his bar. Consider it to be a flight bar. Copper will not work. I am not aware of anyone that makes stainless steel bar that is filled with copper that would work for him, but that would be the way that I would go if I could find it.
- Navarre, Florida
August 1, 2008
A. Hi Jim. But we have both heard of titanium clad copper, which would deliver strength, while also offering good corrosion resistance and current-carrying capacity.
Regards,
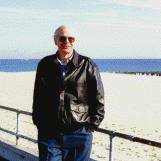
Ted Mooney, P.E.
Striving to live Aloha
finishing.com - Pine Beach, New Jersey
Dark burnt looking areas on Sulfamate Nickel plated bus bars
We're having a metal fabricator supply us with small copper (C11000) bus bars (.75"W x 4"L x .050" thick) that we require plated with Sulfamate Nickel per ASTM B689, Type 1, Class 5. Our fabricator has one of their sub-contractors perform the plating. Because we've specified Type 1, we're expecting a dull flat appearing plating. Although we've received varying degrees of brightness/dullness from different lots, they're generally towards the dull end of things.
My concern is that on some of the dullest lots, there's a small percentage of parts that have very darkened regions (1/4 to 1/2 of the surface area of the part). The darkened area appears fairly dark black, almost like an thin burnt organic film however it doesn't have any easily measurable thickness and doesn't have any different finger feel from surrounding areas.
The ASTM spec states that plated parts shall be "...free from visual defects such as...burned deposits...". Can anyone conjecture what I'm seeing and can it be classified as "burned deposits".
Thanks,
Gregg
Manufacturing Engineer - Redmond, Washington, USA
January 4, 2011
A. It sounds like the subcontractor has produced some pretty poor plating. I think you are probably right in thinking the bus bars have got a burnt deposit on them. If you know what you are doing, a good sulphamate nickel should be very easy to put down, so I would find an alternative supplier
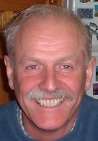
Trevor Crichton
R&D practical scientist
Chesham, Bucks, UK
January 5, 2011
A. Copper contamination in nickel sulfamate solutions does plate out (co-deposit) dark gray to black in low current density areas (which would also be low thickness because of low current). Seems the plater needs to electrolytically purify ("dummy") his contaminated solution.
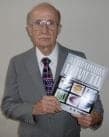
Robert H Probert
Robert H Probert Technical Services

Garner, North Carolina
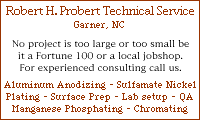
January 6, 2011
Electrolytic nickel plating vs. electroless nickel for bus bar?
July 24, 2014Q. Dear all,
I am working in a Low Voltage switch gear company
We usually use Tin-Plated Copper Bus-bar for most of our projects.
Now in a particular project, the requirement is for Nickel plating for Copper Bus-bar,
so my question is which Nickel Plating will be better for our application where current is around 500A?
a) Electrolysis Nickel plating or
b) High phosphorous Nickel plating
Regards,
Low Voltage Switchgears - Bangalore, India
A. Hi cousin Manoj. Unfortunately, when someone simply says that nickel plating is required, without giving a reason, it's hard to extrapolate which type of nickel plating would be better or what thickness is required.
On top of that, there is perhaps a translation difficulty here because I don't know whether option "a)" was meant to mean "electrolytic" or "electroless", whereas option "b)" pretty much implies electroless nickel plating.
As a general rule, electrolytic nickel is substantially less expensive, but is less corrosion resistant than phosphous-based electroless nickel plating. Good luck.
Regards,
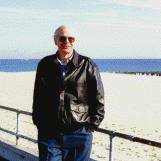
Ted Mooney, P.E.
Striving to live Aloha
finishing.com - Pine Beach, New Jersey
July 2014
September 29, 2015
Q. Hi, Can anyone clarify my question related to nickel coating on the entire Al bus bars? ...
How about the thermal handling capability?
Impact of temperature rise with and without Nickel plating?
Thanks in advance for your support,
Karthik Ganesan- Sweden, Ludvika
A. Karthik,
Regarding Ni plating on Al bus bars, this is discouraged unless absolutely necessary because typically the Ni does not improve electrical and thermal conductivity characteristics. Silver plating is better but not all situations can permit Ag.
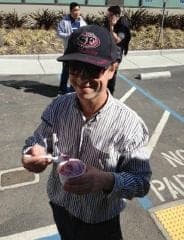
Blake Kneedler
Feather Hollow Eng. - Stockton, California
November 20, 2015
Q, A, or Comment on THIS thread -or- Start a NEW Thread