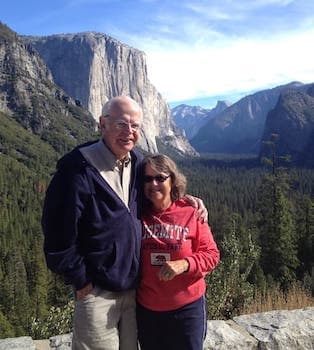
Curated with aloha by
Ted Mooney, P.E. RET
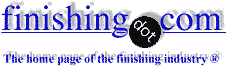
The authoritative public forum
for Metal Finishing 1989-2025
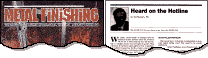
-----
Parkerizing, Manganese Phosphating
2000
I keep getting quotes that require "Parkerizing". What I do is Manganese Phosphating and Black Oxide.
When I do a search of Parkerizing on the net all I ever find is that its more like Black Oxiding. But then the mil specs compare a lot to the Manganese phosphating.
What "IS" Parkerizing so I can gain some knowledge on it and not have to turn some of these quotes down. thanks Chris
Chris Galligan- Oshkosh, Wisconsin, US
Parkerizing and Bonderizing are old established trade names for heavy metal phosphating. Bonderizing is typically prepaint and Parkerizing for wear resistance and corrosion resistance. Parkerizing can be manganese, massive iron or heavyweight zinc phos. Unless the contract calls for a specific phosphate type there is no reason why you shouldn't do it with your Mnphos. R
Roger BridgerWalterisation - Croydon UK
2000
First of two simultaneous responses--
Contact Henkel Surface Technology, formerly Parker, formerly Parker-Amchem. They will be able to tell you what their former products were or perhaps still are.
Tyrone L. Caley- Jefferson City, Missouri
2000
Second of two simultaneous responses--
Parkerizing is a Trade name owned by Henkel, a huge metal finishing material vendor. Hand guns used to be Parkerized. I have never seen a phosphate that was as fine grained and durable as that on some old 45 cal pistols. There probably is another step or two for the process. Parkerizing dates back to Parker chemical which became Parker-Amchem several years ago and Henkel about 3 years ago. Why not ring them up and get the specs from them.
James Watts- Navarre, Florida
2000
Parker Amchem was and still might be located in Horsham, PA
John Bernard- Chester, VA, USA
2003
Parkerizing is a simple process in which a micro-scopic layer of iron is removed and replaced with either a zinc or manganese ore. Either mineral is mixed with phosphoric acid and a few other chemicals. Then the concentrate is mixed with heated water ( typically 190 degrees ) and the conversion process takes place at this time. The glass or sand blasting process in only to give the part a smooth finish and to remove any excess grease or oils from the iron. There are several grades of parkerizing concentrates available, so you have to be careful which one you use. The key ingredient is the amount or zinc or manganese dioxides in the solution. These two ingredients are what gives the iron its distinctive gray to charcoal balck color.
Scott Owens- Taylors, SC, US
January 6, 2009
Q, A, or Comment on THIS thread -or- Start a NEW Thread