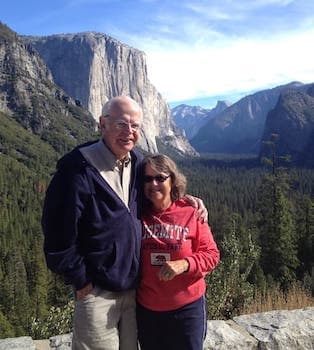
Curated with aloha by
Ted Mooney, P.E. RET
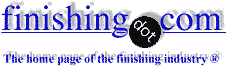
The authoritative public forum
for Metal Finishing 1989-2025
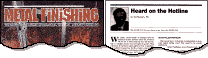
-----
General info on Autophoretic® coatings
2000
Q. I would like to learn more about Autophoretic® coatings. (I'd also like to learn how to spell it if I didn't spell it right.) I am evaluating some samples in salt spray right now and they are doing fairly well. I am looking for some good sources of information.
My company is a big user of hex chrome over zinc and zinc alloy electroplate, but hex chrome is going to be banned in the auto industry. We are looking at different alternatives and wanted more info on this one.

Tim Neveau
Rochester Hills, Michigan
A. Autophoretic® is a registered trade mark and product of Henkel Surface Technology. No I do not work for Henkel, the questions seem to be around their products.
The Autophoretic® coating is in competition with electrocoat process. The process is a waterborne organic coating process. Parts are immersed in the solution after normal cleaning and rinsing. There is typically 8 steps to the process including two rinses, one DI water after Autophoretic® and cure at low temperatures.
To give you a good comparison I would do what I had a gentleman in the Netherlands do. I had him contact Henkel and had them explain the Autophoretic® process and why it was wonderful and better than electrocoat. Then he contacted PPG or Valspar, I forget which, and had them explain their electrocoat process and why it was wonderful and better than Autophoretic®.
He found this to be very informative and gave him ideas for comparative testing.
Good luck!
Tyrone L. Caley- Jefferson City, Missouri
2000
Thanks!

Tim Neveau
Rochester Hills, Michigan
2000
2000
A. Autophoretic® coatings are a little different from e-coat in both the way they're applied, and in the usefulness of the coating.
Typically e-coat is good for both corrosion resistance and appearance, but not particularly good at resisting physical damage.
The strength of Autophoretic® as I see it is it's physical integrity, making it an excellent choice for areas like underhood components and other parts that don't need a class A finish.
My company doesn't sell it, but one of my customers that uses it. He's been using it for several years.
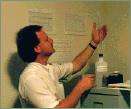
Jeff Watson
- Pearland, Texas
Q. Hello;
I own a business that specializes in restoring carburetors and fuel pumps for classic cars, trucks, and boats. Many carburetors originally came from the factory with a chromating (also called dichromating), which gave them a bronze/goldish appearance. Others came in other colors.This served for corrosion inhibition and appearance. However, the process involves and creates environmentally hazardous products.
I am interested in knowing if any dyeing/staining, etc process exists for steel, cast iron, and potmetal that will yield various gasoline resistant colors, while not creating or utilizing any environmentally harmful products. Thank you.
Hal Houghtonclassics preservation - Sand Lake, New York
2000
Q, A, or Comment on THIS thread -or- Start a NEW Thread