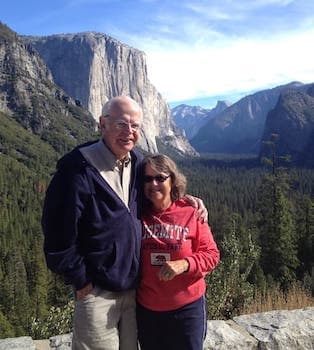
Curated with aloha by
Ted Mooney, P.E. RET
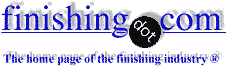
The authoritative public forum
for Metal Finishing 1989-2025
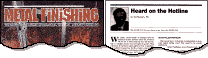
-----
Racking large rings for sulfuric Acid Anodising
Q. Hi, I'm tasked to determine a loading method for an Al 7057 ring of OD: 5.5 ft x ID: 4.9 ft x H: 3 ft for sulfuric acid anodising.
Loading in vertical method I would save up each tank take-up space as the width of each tank would be about 4ft as compared to horizontal loading method of each tank width to be of 7.5 ft. There are 13 processing tanks required. The latter method could ease in loading into and out from the tank.
I would like to know what is the general adopted practice in loading the above ring configuration.
Jimmy S. - Singapore
Special Process Engineer - Singapore
June 3, 2008
A. Hi, Jimmy. If you owned a jobshop with 4 ft tanks, I think it would be fine to take the job and rack the parts vertically; it's certainly eminently doable. But when you are custom designing a line for particular parts, fitness to purpose is a key issue and I don't think you should try shortcuts based on real estate usage. You know which is the best way to rack these parts for the best draining, minimum cross contamination, freedom from gas accumulation, consistent agitation, and good access for auxiliary cathodes if necessary. Symmetry is beautiful and nature will punish you in ways that are hard to predict if you ignore it :-)
If you take the shortcut you might spend the rest of your career there saying: "Boy, it would have been so much easier if . . ." :-)
Regards,
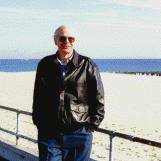
Ted Mooney, P.E.
Striving to live Aloha
finishing.com - Pine Beach, New Jersey
June 3, 2008
A. Another item to consider is where can you have contact points? The bottom , ID or OD.
Everything else the same, I would put it into the tanks in the horizontal direction, IE: OD vertical. If your power supply was large enough, you could build a rack that would allow for doing 2 parts at a time. This stuff has to be heavy, so I would run it 1 at a time.
In the USA, the tanks would have to be elevated or a good guard rail put up between the operator and the part, even if it is automated.
Also, in the USA, I preferred to use rotationally molded tanks of PP for the hot tanks and PE for the rest. I have used SS box beams for some tank support and painted 2 x 4 wood for others. The hot tanks also had painted 1/2" plywood walls for additional support when the tank was large and nearing allowable temperatures.
Reason, they worked well and were a LOT cheaper than any other tank.
(and I had a vendor that gave me great price breaks on large orders)
- Navarre, Florida
June 7, 2008
Q. Hi Ted & James,
Thank you for your sharing. Your advice will help on our assessment of the potential site for this part.
Hi Ted,
You pointed "Symmetry is beautiful...."; what is symmetry here referred?
Thank you,
Regards,
- Singapore
June 9, 2008
Q. Hi, Jimmy. By symmetry I meant that if the ring is racked in what you call "horizontal method", the part is everywhere the same except for perhaps some small gradient factors from the bottom of the ring to the top of the ring when in the plating tanks, which will be manifest immediately. Everything is identical radially as you go around the ring in the fashion of the hands around a clock. Any slice of the pie is identical to any other slice.
With the "vertical method" of racking, there is an outside bottom to collect gas bubbles near the bottom of the tank, an inside bottom to collect sediment near the bottom and which will drain poorly, an inside top to collect gas bubbles near the top, an outside top to collect sludge near the top, and every variation in between. And there is variation along the other direction as well, i.e., from the center of the part the edges of the part, etc. Vertical is certainly doable but in my opinion is not nearly as good.
Regards,
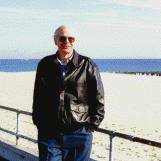
Ted Mooney, P.E.
Striving to live Aloha
finishing.com - Pine Beach, New Jersey
June 9, 2008
A. Jimmy
With racking the part horizontally, you could use air agitation. If racking vertically, air agitation will not be effective on the outer upper half. Mechanical agitation would work if the part was vertical. Something else to consider.
- Colorado Springs, Colorado
June 10, 2008
Q, A, or Comment on THIS thread -or- Start a NEW Thread