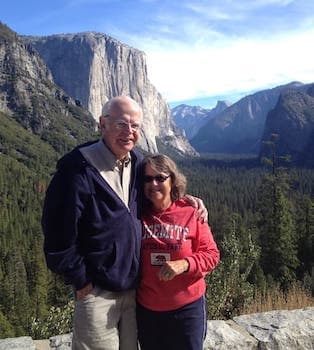
Curated with aloha by
Ted Mooney, P.E. RET
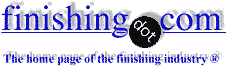
The authoritative public forum
for Metal Finishing 1989-2025
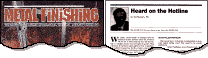
-----
Chromic acid anodize ramp-up time
May 30, 2008
I have been involved in the chromic acid anodize processing of parts for military and aerospace applications for the past 10 years. We process parts using the low voltage chromic anodize process ( 20 volts ).
We are having paint adhesion problems on our parts after chromic acid anodize. They are failing the wet tape test after paint. It is not a consistent problem. Three or four orders will pass and then one order will fail. When an order fails, all of the parts in that order fail.
When I looked at our processing of the anodize loads, I found that our line operators are ramping-up loads from 0 volts to 20 volts in
30 seconds to 1 minute. I installed a voltage data logger on the chromic anodize rectifier and found that the operator ramp-ups vary all over the place from 30 seconds to 6 minutes.
Our internal specs specify a 5 minute ramp-up from 0 volts to 20 volts (1 volt every 15 seconds) to meet the various Boeing and Lockheed specs we must meet.
What is the purpose of the 5 minute ramp-up to 20 volts for chromic acid anodize?
Appreciate any information you may have.
Finishing Shop Lab/WWTS Mgr - Denton, Texas, USA
Hi, Lee. The reason for ramp-up is that anodize coatings are insulative; the electrical resistance builds as the thickness builds. A voltage that is low enough to prevent burning at the beginning of the cycle would not be high enough to allow anodizing to continue later in the cycle. A voltage high enough to allow continued anodizing after buildup would burn the parts initially when there is no resistive film.
I think your rectifiers need ramp control built in.
Regards,
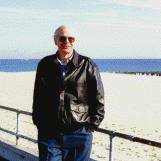
Ted Mooney, P.E.
Striving to live Aloha
finishing.com - Pine Beach, New Jersey
May 30, 2008
First of two simultaneous responses -- May 30, 2008
Another factor is the powersupply sizing. If you rapidly ramp up the voltage, it takes a massive amount of amperage for several seconds. Also, the racks frequently are not built for this amperage and heat up rapidly, wasting electricity.
A second factor to look at is the seal. Is it hot enough and long enough?
Third, are you painting "too soon" after anodizing?
It sounds like your crews need a bit of quality training with a week off, unpaid, for those that fail to follow written procedures and sign the traveler as having complied with procedures. It is tough love, but you can not certify parts if they do not.
- Navarre, Florida
Second of two simultaneous responses --
First,be sure the alloy you are working with should get 20 volts or 40 volts. Then if 20 vols, spend 20 minutes getting up to 20 volts, then stay in another 30 minutes. If it is a 40 volts alloy, spend 40 minutes getting up to 40 volts, then stay in another 30 minutes. After you reach the 20 or 40 volts set it on "voltage control", then during th next 30 minutes the amperage will fall as the coating insulates. In Aluminum How-To, I list the alloys that Boeing and Lockheed prefer at only 20 volts; all others sholud get 40 volts.
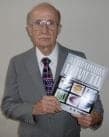
Robert H Probert
Robert H Probert Technical Services

Garner, North Carolina
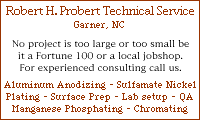
May 30, 2008
July 4, 2008
Dear Lee
If you process parts to Boeing spec's you are required to ramp per the spec. If you are not ramping correctly at the very least you are in violation of the specification and it could have impact on your product and thus failed test's. If there is not specification requirements than following your procedure will narrow down the possibilities of why you have failed tests
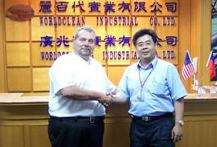
Drew Nosti, CEF
Anodize USA

Ladson, South Carolina
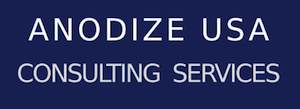
Q, A, or Comment on THIS thread -or- Start a NEW Thread