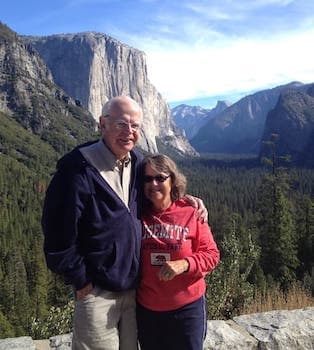
Curated with aloha by
Ted Mooney, P.E. RET
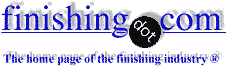
The authoritative public forum
for Metal Finishing 1989-2025
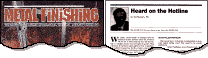
-----
How to reach very high hardness for 410SS?
Sir,
I want to increase surface hardness of a part to minimum 1000HV3.
What material and hardening process to be used?
Now I tried with SS 410 - liquid nitriding is done. We had achieved the hardness but surface finish is very rough. We have to maintain the surface roughness value below 4 microns.
We seek your guidance.
Employee - coimbatore, INDIA
October 26, 2021
A. Hi Madhavan. I am not a metallurgist so I am not sure of the applicability of the Quench-Polish-Quench process to SS410 as opposed to high carbon steels. But the process does address the issue of surface roughness, so you might want to view "The Kolene® QPQ℠ Process" in our on-line library.
Alternatives for 1000HV3 and above include hard chrome plating or titanium nitride coating.
Luck & Regards,
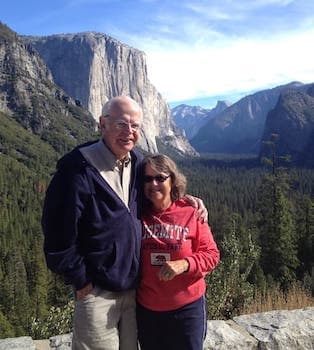
Ted Mooney, P.E. RET
Striving to live Aloha
finishing.com - Pine Beach, New Jersey
October 2021
⇩ Related postings, oldest first ⇩
Q. Dear Sirs,
I am a supplier quality engineer.
I have one component the surface hardness should be over HRC38 and the raw material is SS410. Through the normal quenching & temper process, the hardness cannot meet our requirement (only HRC35-37). Current austenitizing temperature is 1020 °C. the quenching temperature is 850 °C and the temper temperature is 270 °C. The quenching media is oil.
Do you know where the problem is? Would you please give me some suggestion to help us reach HRC38?
Thanks and best regards
Johnny
Supplier Quality Engineer - Hong Kong
May 26, 2008
A. Hi Johnny,
Your processing sounds a bit unusual. Do you mean you austenitize at 1020 °C then allow to cool to 860 °C for quenching? If so, don't do it. You should be quenching from the austenitizing temperature (1020-1050 °C). That gives 40-41 HRc as-quenched. As the tempering temperature is increased to around 450 °C, secondary hardening will progressively increase the hardness to around 43 HRc. Around 450 °C a rapid drop in hardness begins, as the tempering reactions overtake the secondary hardening reactions, and you'll lose about 13 HRc units going from 480 °C to 550 °C.
This is not just a surface-hardening action - it is through-hardening on sections up to around 300 mm.
I suggest you quench some parts from 1020-1050 °C then do trial tempering over a range of temperatures to see just what happens.
Also, be aware that the carbon content is significant. Spec is 0.15% max, and the hardness values I've quoted apply to around 0.10% which is a typical carbon content. But if you happened to have, say, 0.14% carbon then the hardnesses would be about 2 HRc units higher than what I have quoted above.
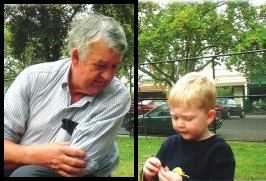
Bill Reynolds [deceased]
consultant metallurgist - Ballarat, Victoria, Australia
We sadly relate the news that Bill passed away on Jan. 29, 2010.
May 29, 2008
Q. I'm service engineer and following are my 2 questions in manufacturing of machine spare GUIDE RODS.
What is the hardness range of SS410, or what max. hardness can be achieved?
What is the complete heat treatment cycle to get max hardness?
asst manager edd - RAJKOT GUJARAT INDIA
February 25, 2012
A. I am not sure that I would trust a free answer from a total unknown. Just taking it to the max. hardness will severely compromise some of the other desired characteristics of the metal.
ASM has good reference manuals for this. A university engineering department should have them.
- Navarre, Florida
February 28, 2012
Hi Dharmendra. To expand on James' suggestion, I think you need to tell us more about these "guide rods", because people will be reluctant to post a process sequence which makes SS410 too dangerously brittle for the application :-)
Regards,
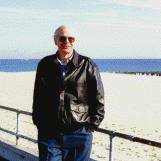
Ted Mooney, P.E.
Striving to live Aloha
finishing.com - Pine Beach, New Jersey
![]() |
A. 410 is a funny stainless steel. Depending on the carbon content, you MIGHT be able to harden it per AMS2759/5, the standard aerospace heat treat specification, to Rockwell C 40 or more. We find we have to specify the hardening capability of the 410 we buy when we purchase it. ![]() Lee Gearhart metallurgist - E. Aurora, New York March 7, 2012 A. Good afternoon: - St Louis, Missouri March 7, 2012 A. ASM Hand book can be referred to. - Rourkela, India March 9, 2012 |
Q. Dear sir,
I have a query, we have to supply a shaft for vertical pump. Max shaft dia. is around 230 mm and length is 3000 mm, MOC is SS410. Now I am not sure whether to suggest hardening up to T or H condition. Though T condition allows higher percentage elongation I am tilting towards it but the client is insisting for H condition. Could anybody please suggest me up to what diameter H condition is possible or achievable.
Some link or additional reference would be helpful.
Thanks & Regards
- Pune, India
April 9, 2012
Q. For valve gates in SS 410 material the hardness req'd is 190-235 BHN. After oil quenching & double tempering (625 & 680 °C), we get about 245 BHN. How to further reduce the hardness to around 200 BHN max.? What cycle of HT would be correct?
R G Pandit- Chennai, TN, India
May 29, 2015
Induction Hardening of SS410
Q. Can SS410 be hardened through induction and air cooled, or it has to be through hardened?
mukul ajmeraproduction - Vadodara, India
December 16, 2015
Q. Which hardening process is required to get hardness up to 85 HRC for a 5 mm thick SS410 sheet used as a brake disc?
Kaustubh patil- Pune, Maharashtra, India
October 3, 2017
October 2017
? Hi Kaustubh. Do you have a sound reason to believe that is possible? (Please introduce yourself and the situation). Several competent metallurgists on this thread seem to imply that it isn't. Good luck.
Regards,
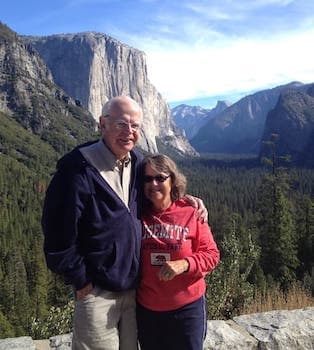
Ted Mooney, P.E. RET
Striving to live Aloha
finishing.com - Pine Beach, New Jersey
Q. I HAVE A COMPONENT PIN IN SS410 OF 14 X 30 MM LENGTH AS PER STANDARD NORMS IN HARDENING & TEMPERING HARDNESS SHOULD ACHIEVE IN 45-50 HRC, BUT ACTUAL NOT GO BEYOND 35-40 HRC. CAN ANYBODY SUGGEST WHAT TO DO ACHIEVE 45-50 HRC HARDNESS FOR SS410?
VIJAYKUMAR MALKHARESHREE GANESH ENGG WORKS - PUNE, Maharashtra, INDIA
October 29, 2017
? Hi Vijaykumar. I think Lee has answered your question. But I'm prompted to ask a question of you in return: in what references are you finding those 'standard norms in hardening & tempering' that you refer to? Your values seem in excess of what the other responders on this page have suggested is practical. Thanks.
Regards,
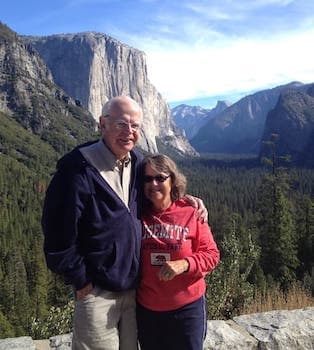
Ted Mooney, P.E. RET
Striving to live Aloha
finishing.com - Pine Beach, New Jersey
Q, A, or Comment on THIS thread -or- Start a NEW Thread