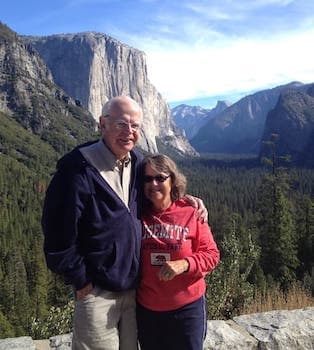
Curated with aloha by
Ted Mooney, P.E. RET
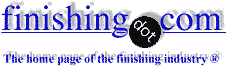
The authoritative public forum
for Metal Finishing 1989-2025
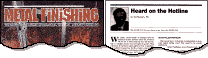
-----
Choosing the right type of process for miniature bright nickel finishing
Hi, l am making my own applied numerals and markers for my watch dials (the tiny hour indicators or numbers in some cases). These are cut out of brass and then l hand file them to a very high standard. After l will solder some tiny copper feet on so that l can rivet the part onto the dial. So far l have mastered the cutting out and hand filing.
I am now trying to establish just what type of plating process and equipment that l will need to produce a bright nickel finish on the parts - like a mirror or chrome finish and hopefully without any need to polish.
Any advice on this would be great.
Thanks
Tim Hadleigh
watchmaker - Reigate, Surrey, UK
May 17, 2008
May 22, 2008
Tim,
Because you want to plate such small parts, a vibratory plating barrel is probably the best way to go. You can move the unit to each process tank without a problem.
Bath Chemistry
soak cleaner
electrocleaner (direct current)
bright dip (if necessary)
acid dip
Bright acid copper
acid dip
Bright nickel plate (decorative)
Equipment
Vibratory plating barrel
Rectifiers (3 preferred)
Process tanks, anodes, anode bags and hooks, leads, anode and cathode buss bars
Two small filter systems
Small oil-less air blower
Sparger legs for agitation
As you price these items out, you may find it beneficial to send the parts out for plating instead of installing the plating line yourself.
Process Engineer - Syracuse, New York
May 27, 2008
Thanks Mark, I really appreciate your response.
Would the parts be touching each other in the barrel? There is a need for the parts to be completely unmarked or scratched given the nature of the business. Also, would they need polishing afterwards to achieve a mirror finish?
I am not against having a company do this for me and am only looking to do this Myself as the Swiss suppliers are all too busy.
- Reigate, Surrey, UK
Mark,
You forgot the waste treatment system and the lab!
Tim,
You want jewelry. In that I mean top-of-the-line goooood stuff. There is mirror bright and there is MIRROR BRIGHT. I've done decorative chrome auto restoration work so I think I know a little about what it would take to get there. It isn't the easiest thing to do. Big learning curve. Expect a bit of scrap(also, I think you might have to polish them to get "mirror" bright, but that is subjective). I would follow Mark's advise and develope a relationship with a good, hopefully local plater. You sound like a craftsman and I wish you the best of luck.
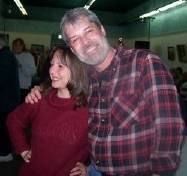
Trent Kaufman
electroplater - Galva, Illinois
May 27, 2008
Tim,
Trent is absolutely right about the learning curve of electroplating. To answer your question, yes the parts have to make contact in order to plate. The vibratory agitation within the barrel (similar to ultrasonic agitation) and the barrel design, prevent the parts from scratching. There are cathodic "buttons" on the bottom of the vibratory barrel for electrical contact. This business of electroplating is very hard for a self-start up operation, especially if you don't have any plating experience. The reason I did not mention waste treatment and a lab is because I was under the impression this was going to be a mini - scale operation. Good Luck!
Process Engineer - Syracuse, New York
May 29, 2008
These are HAND made items so I guess the quanitity is not great. Why not just rack plate these in a beaker or, better yet, make them out of nickel silver, polish and buff and be done.
Neil BellAlbuquerque, New Mexico
June 2, 2008
Q, A, or Comment on THIS thread -or- Start a NEW Thread