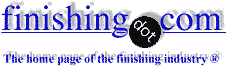
-----
Optimal Chromate Bath Dip Time
May 15, 2008
Is there an optimal time that parts should be dipped in a CR+3 chromate bath?
My plater of automotive parts does rack plating in an alkaline zinc process followed by rinses and nitric acid activation before dipping in chromate. I know that if the time in the chromate is too short I will get poor salt spray results. If all other factors are held constant it would seem the simple solution is to continue to increase dip time until the desired results are achieved, but my plater says that if the time is too long the chromate bath begins to attack the zinc. I find this hard to believe. If it is true, can anybody explain what is going on?
From the plater's point of view the main problem with long dip times is the increase in bath dumping frequency. So he wants the dip short while I want it long. What's the best compromise?
I monitor plater conformance to our company requirements - Wytheville, Virginia
May 17, 2008
Firstly, there is no "optimal" chromate dip time. Suppliers generally give a range. The ability of a conversion coating to develop the optimal film (not too thin, not too thick) is controlled by three primary factors: time, temperature, concentration. The change of any one of those would necessitate a change in one or more of the others to maintain the same film thickness. Dip time also includes transfer time. This transfer time will also have a variable for the ambiant temperature.
As you can see, by addressing only a few of the variables (I didn't include some of the changes in the chemistry of the product as it ages or the rinsing) it is impossible to just keep trying until the correct dip time is arrived at. Generally a plater, in consultation with a supplier, will arrive at the best combination of controlled variables to operate. The plater then needs to maintain control over those portions of the process.
Other causes of poor corrosion resistance in rack plating (I assume you are talking about white corrosion products) can be the use of the wrong chromate, poor rinsing, overheated drying, poor zinc deposit, etc.
You really need to talk to the plater and his supplier.
process supplier - Great Neck, New York
May 21, 2008
Thank you for the response. My plater has been in frequent contact with the chemical supplier trying to resolve the problem. I try to monitor temperature, pH, concentration, and dip time in the chromate bath.
But it is his statement that longer dip times allow the chromate to attack the zinc, resulting in contamination of the bath, that has me puzzled. Is this really true? How is it possible for the chromate to attack and protect at the same time? I am seeking to understand the process.
My forging is made of 1045 steel modified to have a .05-.07% sulfur content. Could this increased sulfur have anything to do with the difficulty my plater is having with this one part?
- Wytheville, VA, USA
Q, A, or Comment on THIS thread -or- Start a NEW Thread