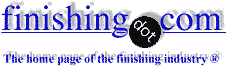
-----
Electroless Cu Plating and Electrolytic Nickel Plating resistance
Hello everyone,
I'm a new plating engineer in a manufacturing plant and I would like to ask about two subjects as stated above. We are doing electroless Cu plating on panels without holes and we are encountering uneven resistance and thickness distribution. We have tried improving the solution agitation by making it more vigorous but still we cannot get a ±5% variation from the mean. The bath compositions are Cu, formaldehyde, NaOH and EDTA. We are keeping the solution at around 45 deg C and we have tried lower temperature like 34 deg C but still the distribution is not good. Do you have any idea of what else can we do to improve the thickness or resistance distribution in our electroless Cu plating? what else do we need to consider? by the way, we have autodosing in our electroless Cu plating.
The second query is about Electrolytic Nickel Plating. We cannot meet the target current setting of 150 Amp and we are only getting 70 Amp and we found out that the rectifier we are using is only 6 V and we need 10 V. We are using nickel sulfamate, nickel chloride and boric acid in our electrolytic nickel plating solution. Is it really because the resistance is high for Nickel plating solution thats why the 6 V rectifier is not suitable? If so, is there any way that we can still use this rectifier and decrease the resistance for us not to buy a new rectifier anymore? I will highly appreciate all the help that you can extend to me and thank you so much in advance.
More power to finishing.com!
Meredith Cheng
plating engineer - Shatin, NT, Hong Kong
May 8, 2008
Hi, Meredith. Someone else will have to address the first problem for you, but I have experience in the second.
You will not be able to significantly reduce the solution resistance; been there, done that. I worked on a line nickel plating huge sheets, where 18 volt rectifiers weren't enough. What will work, if you can implement it, is placing the anodes significantly closer to the cathode. If they are presently 8 inches away and you can get them to 4 inches away, you will be in the range of being able to reduce the voltage from 10 volts to 6 volts. What fools everybody is that flat sheets require more voltage than piece parts. With piece parts there is a large "cloud" or "funnel" of current-carrying solution around the plated area, whereas with flat sheets, the rather high resistance of nickel plating solution becomes apparent.
Regards,
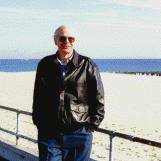
Ted Mooney, P.E.
Striving to live Aloha
finishing.com - Pine Beach, New Jersey
May 8, 2008
May 9, 2008
If the total load is 150 amps, then 6 volts should be enough.
Increase the agitation and move the anodes a tiny bit closer. Check your plating temperature, as it makes a difference. I liked 120 to 130 °F which gave a more even plating than colder temps. I would also make sure that the anodes are making very good contact as it does not take much corrosion on the hanger or the bus bar to act as a very good insulator.
Check with your electroless copper vendor. ± 5% may not be possible on all parts.
- Navarre, Florida
Q, A, or Comment on THIS thread -or- Start a NEW Thread