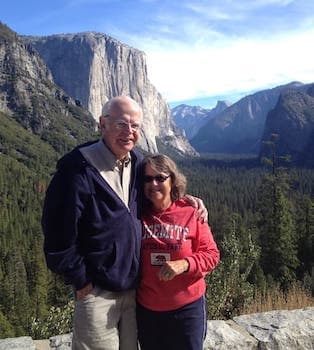
Curated with aloha by
Ted Mooney, P.E. RET
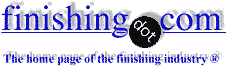
The authoritative public forum
for Metal Finishing 1989-2025
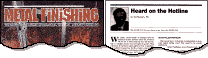
-----
The effect on HDG of sulfur in the steel
May 8, 2008
Dear Sir
What is the effect of the sulfur content (% range)in the steel composition on the galvanized materials as physically & chemically?
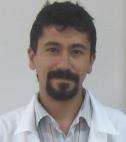
Hakan Esen, Material Engineer(BSc.)
galvanizing plant manager - Bursa, Turkey
May 10, 2008
Hi, Hakan. Abstract, general, questions are much better handled by books about galvanizing, with their highly structured tutorial format, than by a public forum. But this forum is great when you post details of your own situation and get highly directed comments on it. Please tell us what is going on. Thanks.
Regards,
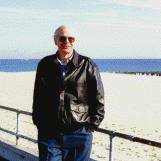
Ted Mooney, P.E.
Striving to live Aloha
finishing.com - Pine Beach, New Jersey
May 12, 2008
Dear Sir
I have two pipes that have different chemical compositions.
One of them is shiny and there seems well alloyed(good adherence)coating-after hammering we can see.
However the galvanizing of other is brittle,no adherence(Although galvanizing occurred,after hammering I saw that micrometer showed null(zero) means that no galvanizing. And sandaline effect have been also seen,but silicon content is 0,02%.
The composition is
%C:0.10 %Si:0.02 %Mn:0.40 %P:0.009 %S:0.0011
Slicon is Ok according to Sandaline curve.
%Si+(2,5x%P)<0,09(based on GA and GAA literature)
According to GA data sheet,sulfur should be less than 0,02%.
When I compare two compositions.Only difference is sulfur content.Best one(shiny and well alloyed) is 0.008%.The other(matt and brittle and thicker)is 0.011-0.019%
Can you give any fix composition for best galvanizing?This material will be used on the conveyor system as barrier.
Can you explain the sulfur effect on galvanizing and relationship between Zn and S such as behaviour of Tin for spangle formation due to intergranular property as microstructural?
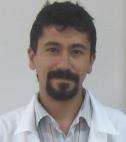
Hakan Esen, Material Engineer(BSc.)
galvanizing plant manager - Bursa, Turkey
May 15, 2008
Sir:
Most of the elements of the steel that you quote are so low that I do not expect the problems you describe. Consider however that with hot rolled steel these elements may be concentrated on the steel surface. Thus a second try at galvanizing (after the first coating has been stripped off with acid) may produce the desired bright coating with good adhesion. When steel is tested it may be tested in the core rather than on the surface. There may be other important elements in the steel including aluminum as in aluminum semi-killed steel.
If your zinc has more than 0.3% tin, I would say that you are in big trouble and can expect cracking in the stressed steel product (see the recent question (letter) relating to spangle).
Regards,
Galvanizing Consultant - Hot Springs, South Dakota, USA

Q, A, or Comment on THIS thread -or- Start a NEW Thread