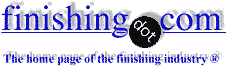
-----
How do flow rate, amp-hours and pH relate to the thickness of the Ni on a stamper?
Hi I am a student currently doing my internship at this local stamper making company and I am attached to the stamper department. I have been assigned to improve their current stamper thickness to between 290-300 um.
My question is I can see from my experimentation that there is a relationship between the flow rate of electrolyte,ampere hr, pH, [Ni] and the stampere thickness. However each time I perform a DOE the results turn out to be bizzarre and pretty random. I there anything I am totally misssing out on? I fail to understand what is preventing me from getting my favourable results. Help!
Student - Singapore
May 8, 2008
Welcome to the wonderful world of plating. Not all of the electricity goes to converting nickel ions to nickel metal. some is lost to heat formation and H2 and O2 evolution. This makes it very difficult to exactly reproduce the same result for each time you try.
Solution flow is often overlooked, but is important as it sweeps away the diffusion layer at the part which allows fresh ions to be in contact with the part.
pH is extremely important to plate rate. The lower it is, the slower the plate rate. If you allow the pH to go high, the plate rate goes up, but you get an ugly plate and the properties of the plate are not the same!
A lot of times plate rate can be faster at a lower temp, but not always. The higher temp normally allows for a more uniform plating thickness. You need to be in the proper range.(especially for a stamper)
Higher amperage means faster TOTAL deposited nickel, but it will be far less uniform, which is not good for a stamper.
If everything is optimized, only longer plating time will give you greater thickness.
- Navarre, Florida
May 9, 2008
May 14, 2008
Lalitha,
Electroforming is a complex science, but it obeys fundamental rules such as Faraday's Laws of electrolysis. Firstly, you need to have your bath operating at optimum conditions. You do not say what conditions you use or what bath it is, but assuming it is sulphamate, the optimum pH will probably be 3.8-4.2 and the temperature will be between 40 and 65C; there is a relationship between optimum pH and temperature, but it is quite complex. You also need to have the nickel concentration optimised, but this will depend on numerous variables and you should discuss this with your chemical supplier or someone who knows your process very well. The pH will affect the efficiency of metal deposition, so you need to get this right. If it is sulphamate, you must not go over 70C or the sulphamate will start to break down. The optimum cathodic current density will depend on your temperature and electrolyte flow rate. The flow rate will depend on the shape of your electroforming mandrel and the bath composition, in terms of additives. The anode and cathode areas should be approximately the same, although this is not critical - do not start trying to measure the area of your S-nickel rounds, just measure the area of the baskets they are contained in; it is better to have more anode area than less!
Once you have the bath optimised, you can start to develop your electroforming techniques. You need to have a zero stress bath, or perhaps, at the very worst, a very, very slightly tensile bath. You need to ensure the electrolyte flow into your mandrel is adequate, but this will depend on many factors - do a bit of experimentation here.
The amount of nickel deposited is directly proportional to the current and time (i.e., Faraday's Laws). The current density will affect the stress in the deposit, so you will need to know the optimum current density and the workpiece area to calculate the total applied current.
Once everything is optimised, you can start to electroform properly. I would expect the time taken to deposit a 300 micron electroform will be at least 10 hours and probably nearer 15-20hrs, depending on your operating conditions.
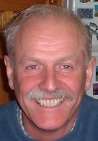
Trevor Crichton
R&D practical scientist
Chesham, Bucks, UK
Q, A, or Comment on THIS thread -or- Start a NEW Thread