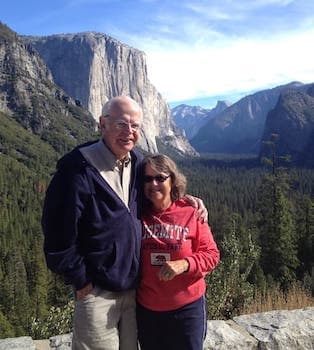
Curated with aloha by
Ted Mooney, P.E. RET
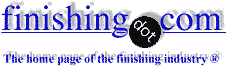
The authoritative public forum
for Metal Finishing 1989-2025
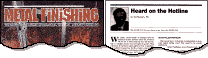
-----
Accelerated test failures of plating on Zamak 3
May 6, 2008
I am a manufacturing engineer for a fabless design house of semiconductors & optical components. Most of our products go into the video or datacomms sectors. Recently, one of our sub-contractors has been procuring die cast Zamak 3 (zinc-magnesium-copper alloy) parts with electrolytic copper and electroless nickel plating. These have to withstand 2000 hours at 85C/85%RH, but to ensure we have the appropriate plating thickness & a competent supplier more quickly, we have been using an autoclave test, (100%RH, 121C, 2 atm pressure), and we are getting blistering & peeling on parts from two plating suppliers.
It has been suggested that the autoclave test conditions are too severe for the combination of materials, that the Zamak 3 will outgas & cause the effects we have been seeing. We have also had parts distorting in the test.
Please can anyone confirm this suggestion, and tell me the maximum conditions that plated Zamak 3 can handle?
Moray Stewart-Guthriecustomer for plated parts - Burlington, Ontario, Canada
I have been involved in plating zinc-based diecastings for many years and in my opinion 121 degrees C. is a ludicrous temperature to test zinc-based diecastings at. I would think that 85 degrees C. is a severe enough testing temperature !
You don't say if the parts are being chemically milled prior to plating. For your demanding standards this is probably essential.
- Corby, Northamptonshire, England, U.K.
May 13, 2008

Q, A, or Comment on THIS thread -or- Start a NEW Thread