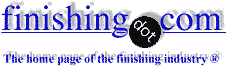
-----
Anodize Dye Releases After Bake
We machine complete a number of parts for a particular customer of ours, all undergoing a similar process sequence. Parts are made of
2024-T351. We machine the basic shape of the part, it then undergoes
MIL-A-8625 / MIL-PRF-8625
[⇦ this spec on DLA], Type II, Class II anodizing at an OSV shop and is typically dyed red or black. Part comes back to us for some post machining operations, then goes back out to OSV for MIL-C-5541, Class 3 chem film to cover the areas machined in the second operation. Given the configuration of the part, however, the entire part must be run through chem film (masking off the anodized area is not feasible). Part is shipped to our customer where it goes through a part mark process which include a 300°F bake for 15 minutes. We know this is not an ideal process from an engineering standpoint but we do not have a choice, part must be run this way. If only some corporate engineers had manufacturing experience, they would realize this process is crazy...
Our customer (down in Mexico!) claims they are baking the parts per spec, and they have had huge quantities of rejections because after baking, the dye begins coming off the anodize. Our OSV has tried just about everything imaginable to fix the problem - used different sealants, limited the anodize thickness - but the problem will only go away for a little while before coming back. I suspect it is either that they are over-etching during the secondary chem film operation, or they are not changing their sealant solutions often enough, but they consistently deny this is the problem.
I am at my wit's end here. Any ideas on what is causing the dye to release? We are unfortunately bound to this process so we need to make it work somehow.
Quality Manager - Denver, Colorado, USA
April 10, 2008
First of two simultaneous responses --
Your post begs the question--why are you machining the part after anodize?
1. Can you use a "touch up" chem film--IE: brush it on and rinse?
2. Can you completely machine it, chem film the required area, mask the required area and anodize?
- Navarre, Florida
April 11, 2008
Second of two simultaneous responses -- April 11, 2008
Domenic
I hope you are aware the
MIL-DTL-5541
[⇦ this spec on DLA] specification advises against exposing a part to 300F. But if that aspect of the product is acceptable to your customer...
I am not quite sure what you mean by the dye comes off.. fades, discolors, falls off?
If you have established that your OSV can produce acceptable product
(at least sometimes), you or they should be performing testing that will predict some form of conformance (cook some coupons in an oven
@300F for 15 minutes).
For your OSV, I would have them look at seal temperature, concentration, anodize temperature, & run time/coating thickness. You do not say that it is one color more than another, so it would appear the dyestuff is not at issue. Lastly, the cleaning of the parts prior to chem film- do you provide the parts in the same condition every time? Some aged cutting fluids will aggravate such a situation if left on the parts to excess (bake some parts after machining). How the OSV cleans the parts can effect the anodize performace if not done correctly. They should have a recipe.
If the process works sometimes, you just need to find out what aspect is out of control and correct it (some one should continue to perform periodic testing).
- Colorado Spring, Colorado
The high temperature destroys the organic black dye and dehydrates the chromate conversionn coating and stretches the underlying aluminum metal 5 times more than the aluminum oxide on top..
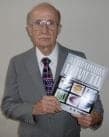
Robert H Probert
Robert H Probert Technical Services

Garner, North Carolina
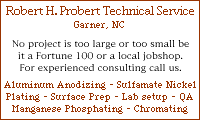
April 14, 2008
Q, A, or Comment on THIS thread -or- Start a NEW Thread