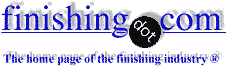
-----
Strange formation of zinc ash on galvanizing bath and in recycling unit
April 8, 2008
Dear all,
I'm working for a tube galvanizing plant and I have some questions concerning the zinc ashes. We use a double salt (ACN 0,78) and before dipping the tube is dried at 100C. When the ash is skimmed, the color of the ashes is sometimes dark grey or black. It looks like some kind of sludge and when it's cooled down the sludge hardens.
We also have done tests with a zinc recycling unit (MZR) to recycle our zinc ashes. The yield was between 50 and 70% but the residue was also a thick slurry that hardens when cooled down. It is almost not doable to remove the residue.
Does anyone know what it is and how I can overcome this problem?
P.S.
We also recycle zinc dust
⇦ on
eBay or
Amazon [affil links]
(batch galvanizing) and top dross
(continuous tube galvanizing) with success (yield between 90 and
95%). Filter tests to lower the iron content have also positive effect.
galvanizer - Oosterhout NB, Netherlands
![]() |
April 9, 2008 Sir: Galvanizing Consultant - Hot Springs, South Dakota, USA Sounds like you should join the galvanizers Association (Stitchting verzinkeri ? My Dutch is hopeless!) ![]() Geoff Crowley Crithwood Ltd. Westfield, Scotland, UK ![]() April 10, 2008 |
April 15, 2008
In response to your writing:
A switch to another flux is not an option at the moment. Tests in the past with other flux compositions (not done by me) did not bring any good. The flux layer is to sensitive for damaging when using a higher ACN number. The zinc coating on the inside has to be 56 microns so according to your story switching to another flux with higher ACN gives problems to achieve this thickness. Profiling the tube on the inside is already done and ok.
In the meantime I have done some analyzes on our zinc ashes and ash from another galvanizer who is using the same type of double salt
(same supplier).
The only difference is that they aren't a tube galvanizing plant and use 0,2% nickel. They also have a MZR and don't have problems with the residue after recycling.
Analyzing the zinc ash gives me a zinc content of 85%. Ammonium is negligible. Chlorid content about 10%. The rest is some iron, aluminium, nickel and insoluble matter. Both samples don't differ much from each other in concentrations. Only the composition of the ashes looks different. Ours looks dark grey and hard and their ash looks brown/red and is powdery.
I did another test where I put about 50 grams in a beaker [beakers on
eBay
or
Amazon [affil links] filled with distilled water and stirred for some time. Both ashes behave totally different. pH were the same, but the solution gave a spongy effect
(zinc flakes). It looks like the ashes are very hygroscopic. Compared with the ash from the other galvanizer this ash was lying as a 'dry' substance on the bottom. No zinc flakes at all.
It looks like I have to dig a little deeper in our process to find out what other reactions occur at the surface that gives different ash compositions.
With filter tests I mean filtering the recovered zinc with a ceramic filter when using the MZR. I used filters with different pore densities to filter the dross particles out of the recovered zinc. Let us call it IRF (Iron reducing filter).
I think you were confused with lowering the iron in flux solutions.
Regards,
Galvanizer - Oosterhout, the Netherlands
April 15, 2008
Sir:
It is true that if the pipes are moved lengthwise (rather than walking-beam) the rapidly rotating drive wheels rub off the flux and cause bare spots. That is why I like walking-beam so much better. It is also true that quadraflux may cause too thin of coating (for you) on the inside. Some profiles can show twice as thick of zinc 1/3 the way down (from the blow end) the pipe, as compared with the bottom end. What I like is a more active flux and tune the inside thickness using the steam blow, both with regard to time and power. In addition there are different blow heads that give a more uniform thickness on the inside.
If you say the other galvanizer uses 0.2% nickel in their flux, then it would be a health hazard for the workers unless the kettle smoke is collected properly. 0.05% nickel in the zinc gives also a good result with lower health risk.
I know you say you have double salt. Actually I doubt that. On "day one" you start with double salt, however when you reflux rejects this dissolves zinc (as zinc chloride) in your flux solution so that the ACN decreases. In South Africa they were using "double salt" but the ACN that I obtained by testing was only 0.4 (instead of 0.78) for proper double salt. I suspect you have very old flux with high baumé,' whereas the general galvanizer has a relatively new flux solution or he knows to add ammonium chloride periodically.
The zinc content of ash is extremely variable and you must specify zinc metal or zinc ion (as chloride). Ammonium IS usually low because it is quite volatile (easily changed to gas). Ashes that are hygroscopic are zinc chloride. Zinc chloride has the old name "butter of zinc."
I find it unusual that you have dross in your ash. Perhaps you kettle is too shallow and your pipe handling equipment pushes the pipes through the dross?
I respectfully suggest that you have your flux solution properly tested to determine the true ACN. This is NOT an easy task because I had 14 companies test the same sample(from a flux that I made up as having exactly an ACN of 1.00). No testing company of the 14 (most of these companies were CERTIFIED) got a usable result! I published the results in the journal Metal Finishing. Once properly tested, I suggest that you add the proper amount of ammonium chloride to your flux solution the attain ACN=0.78.
Regards,
Galvanizing Consultant - Hot Springs, South Dakota, USA

Q, A, or Comment on THIS thread -or- Start a NEW Thread