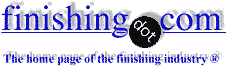
-----
Solutions to Problems with grinding thin wall hard chromed parts.
We are a small job shop with some sophisticated equipment trying to break into the aerospace field. Our problem is we are trying to I.D. grind some thin wall (.080") hard chrome plated parts about 3" in dia. The base metal is AMS 6415. We are grinding on a Kellenberger Kelvaria 4-axis machine with aluminum oxide and or silicon carbide wheels. One of the problems is after grinding we find the parts are round on the machine and when removed are no longer round. We first held them on a magnet, but after removed they would distort. We are only talking about .0003, but our total tolerance is .0007. So me made some pie jaws to hold the part with a little better result. I guess our biggest question is what is the best grinding wheel, grit size ,bond etc. to grind chrome successfully without distorting it. The part is unusual in that it is about 2.5" long and the part that is being ground is .400" on the end. The rest of the material dia. is
.125 thick pillars about a half inch apart kind of like a squirrel cage fan connected to about a 1/2" wide flange at the base. I.D and O.D. need to be concentric within .0005. We need to remove about
.015" chrome per side on I.D. only.
Thanks,
Karl
p.s. all help is welcomed
Use plating with many of our finished products - Lenox, Mass., U.S.A.
March 26, 2008
Sounds like too much chrome removal for such a delicate job. Why is it so? Maybe you need to engineer your plating process a bit to produce a more uniform plate and reduce stock removal. G. Marrufo-Mexico
Guillermo MarrufoMonterrey, NL, Mexico
March 31, 2008
This sounds like an item that would be better suited fo a internal HONE. You should be able to hold a better tolerance with a powered or manual hone. I would look into a company called SUNNEN the offer a wide variety of tools and machines to do I.D.'s
Jim Moore- Pennsylvania
March 31, 2008
April 10, 2008
Thanks for the responses. The plating is thick and is held very consistently but it's thick because we need to end up with .005/ side when finished. In response to the second letter, we have a Sunnen hone. The problem is there is a shoulder at the bottom of the grind area so the hone won't fit plus the concentricity issue is a problem.
Thanks,
Karl
- Lenox, Mass.
The hone that you are using, is it a fixed head or floating head?
It is true that a floating head hone will only follow what is in the bore. This can cause a issue with the tolerances you are triing to maintain.
We mainly use a floating hone to do a lot of internal work. Although we also use fixed hones.
The advantage of a fixed hone is that it will maintain the bore's
"trueness". There is no flex to it, it is a straight shaft. A big disadvantage is that you need several shafts for every size that you are trying to finish to. This allows you to slowly step up the diameter. With a floating expandable hone one shaft can cover several inches in diameter and make it hard to hold tolerance.
I would look into upgrading to a fixed system, this will allow you to step up the size .0005" to .001" at a time.
- Pennsylvania
April 17, 2008
Q, A, or Comment on THIS thread -or- Start a NEW Thread