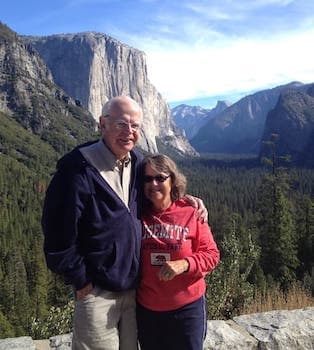
Curated with aloha by
Ted Mooney, P.E. RET
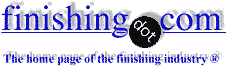
The authoritative public forum
for Metal Finishing 1989-2025
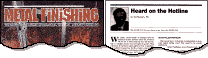
-----
Alternative pickling solutions for copper & brass
Quickstart: Heated dry acid salts (sodium bisulphate) may be the best pickling solution. Hydrogen peroxide can be added to the pickle, or as a subsequent step, to provide brightening. Proprietary solutions rather than home-brew are often used. Acids other than sulfuric-based might be used but are probably much more expensive and some might interfere with wastewater treatment.
Q. Good morning,I have read your response. I would like to know what concentrations of sulfuric or even phosphoric acid should be used for pickling brass? Could hydrogen peroxide improve its effectiveness? In what doses, if ever, and at what concentration? Would 35% be okay?
Thank you
- Italia / Siena
November 16, 2023
9th Edition, Vol. 5
"Surface Cleaning, Finishing & Coating"
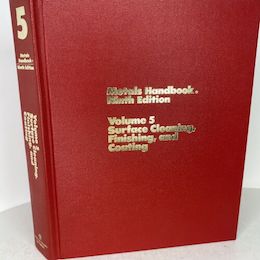
on AbeBooks
or eBay or
Amazon
(affil links)
A. Hi Marcello. 35% sounds very high to me for sulfuric acid; 15-20% is more conventional for pre-plating activation, but it depends on exactly what you mean by pickling (the actual condition going into pickling, the desired condition coming out).
Hydrogen peroxide is an oxidizing agent, and to my experience is often used for brightening copper or brass after pickling rather than being used in the pickling. But here in the USA, finishing shops tend to use proprietary processes rather than formulating from commodity chemicals (for example, peroxide is expensive and it deteriorates quickly, so we usually purchase it as a proprietary with effective inhibiting and stabilizing agents already in it).
ASM Metals Handbook vol. 5, "Surface Finishing, Cleaning, and Coating" has a nice 17-page chapter on 'Cleaning and Finishing of Copper & Copper Alloys' ⇨
I don't know how big your brass parts will be, but can you use a pickling pot and do some experimentation before committing to designing the process line?
Luck & Regards,
Ted Mooney, P.E. RET
Striving to live Aloha
finishing.com - Pine Beach, New Jersey
A. Hi Marcello,
We use a solution of sulfuric acid at 40 to 50 mls/l and sodium dichromate at 22.5 to 30 g/l.
It works fine at ambient temperature and 3-5 mins immersion.
Best regards,
Mark
- A dull grey rock in the Irish Sea
November 21, 2023
A. I wonder in the context what "pickling" means, what the goal is. Are we looking to create an etched surface finish? Just remove tarnish?
Just removing the tarnish can be done with citric acid.
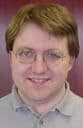
Ray Kremer
Stellar Solutions, Inc.

McHenry, Illinois
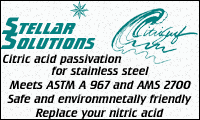
November 22, 2023
⇦ Tip: Readers want to learn from Your Situation 🙂
many readers skip abstract questions.
Q. What can be used to produce an acid-free pickling solution for copper, brass, sterling and gold?
Edward Demanskyart metals instructor - Bangor, Pennsylvania, USA
March 19, 2008
A. What are you trying to accomplish? Why don't you wish to use an acidic product? Would you be willing to use one which contained carcinogens? Would you be willing to use one which was highly corrosive but was alkaline? What do you need?
Gene Packmanprocess supplier - Great Neck, New York
Q. Trying to find a pickle solution that will not burn holes in students' clothing.
Edward Demansky [returning]art metals instructor - Bangor, Pennsylvania, USA
A. Dear Edward,
Most jewelers and metalsmiths use heated "Sparex No.2"
⇦ this on
eBay
or
Amazon [affil links] safety pickle for precious and copper base metals. It is mixed with water and used hot. A heated crock pot is ideal for this solution as it has a lid to slow evaporation. It can be purchased at most larger jewelers supply houses in 2-1/2 lb containers. "Sparex 2" is dry granular sodium bisulphate and is mixed with water for use.
Good luck & Best regards,
alloys & refining - Alden New York USA
Alternative to sulfuric acid for pickling brass
⇦ Tip: Readers want to learn from Your Situation 🙂
many readers skip abstract questions.
Q. We use a sulfuric acid solution to pickle brass ammo casings. I'd like to find an alternative to the use of sulfuric acid. Is there anything out there I could use?
Dale PittmanProject Engineeer - Kansas City, Missouri, USA
February 20, 2014
? Hi Dale. We appended your inquiry to an earlier thread which suggests a proprietary acid salt. But we need to ask why. Does the sulfuric not reliably deoxidize the brass? Does it not leave the brass bright enough? Might phosphoric acid work, or do you have phosphate discharge limits that would be a problem? Thanks.
Regards,
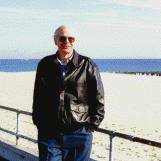
Ted Mooney, P.E.
Striving to live Aloha
finishing.com - Pine Beach, New Jersey
Q. Yes, this does deoxidize the brass well, but I would like to get way from this material as a safety issue, rather than a process issue. Do you know of anything? Thanks.
Dale Pittman [returning]Project Engineeer - Kansas City, Missouri, USA
A. Hi Dale. Please try the dry acid salt 'safety pickle' mentioned by Jim; but here's the thing, and just my personal opinion ...
There are materials which really ought to be avoided when possible:
- cyanide, which will always be difficult to treat and which offers strong potential for fatally poisoning someone if there is a knowledge slip-up anywhere
- hydrofluoric acid, which can cause horrible life-threatening burns from a small exposure, and which can be anesthetizing to conceal it's early damage
- chromic acid, which is carcinogenic, and dries to a powder which tends to spread everywhere
- cadmium, lead, and mercury because they are biocumulative poisons such that any amount at all is considered bad.
While sulfuric acid can be dangerous, especially concentrated acid in drums at full strength, everything in the world is dangerous -- which leaves the question about what is safer and in what way, and what new troubles might it bring, like disrupting waste treatment.
Regards,
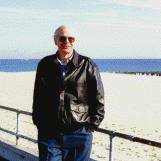
Ted Mooney, P.E.
Striving to live Aloha
finishing.com - Pine Beach, New Jersey
Q. I understand that, which is the reason why engineering is a trade off between better, cheaper, faster; pick two. What I want is to get to is a safer alternative than handling concentrated sulfuric acid, which is dangerous to ship, offload at dock, transport through the plant, store in a particular area, transport through the plant again, store at the machine, then pick it up and pour it into the machine. Which is the only place where it becomes 'safe'.
Which brings me back to the original question; is there a safer alternative to sulfuric acid?
Project Engineeer - Kansas City, Missouri, USA
A. Hi again. You're probably right. I was sprayed on the head with concentrated sulfuric acid when an operator felt that one-handed operation of a drum pump would be okay; I was fortunate enough to have a clear-headed co-worker get me instantly washed down, so it burned enough to hurt but no scars; but it could have been much worse!
Dry acid salts like sodium bisulphate have been suggested, as that is the conventional replacement for sulfuric acid, although they're operated hot, and probably more people in metal finishing shops have been severely injured by hot solutions than by acids. Acid salts, being dry, address some of your safety concerns, and one of the hydrogen atoms has been pre-neutralized with sodium, addressing some other safety concerns.
Phosphoric acid, or mixes of phosphoric & glycolic acid are commercially sold as brass cleaners. Sulfamic acid is the principal ingredient in many copper & brass polishes; and citric acid ⇦ this on eBay or Amazon [affil links] , operated hot, might have merit. So I think it's possible to get away from sulphate as the anion if that's wanted, but those other anions have the possibility of chelating or complexing dissolved metals and causing waste treatment issues that we don't have with sulphates.
I doubt that you'll find affordable highly concentrated liquid acids of any anion that are safe in the way we are talking about anyway. So, short of dry acid salts, one further potential solution is to buy and store the sulfuric acid at a lower strength like battery acid strength if you can find it affordably and pure enough to not mess up your processing or wastewater treatment (usually lead isn't a concern for battery acid but is a concern for metal finishing plants_.
Best of luck!
Regards,
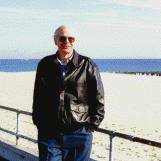
Ted Mooney, P.E.
Striving to live Aloha
finishing.com - Pine Beach, New Jersey
Q, A, or Comment on THIS thread -or- Start a NEW Thread