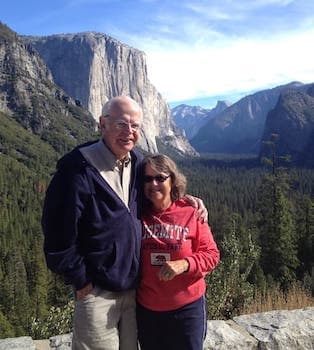
Curated with aloha by
Ted Mooney, P.E. RET
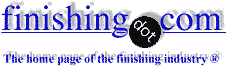
The authoritative public forum
for Metal Finishing 1989-2025
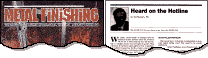
-----
How to differentiate between galvanized steel and the usual cold rolled after powder painting ?
March 15, 2008
Dear all;
Away from chemistry, we had a logistical problem when somebody mixed parts in the stock.
I'll summarize the problem to be short:
we have parts similar in design/shape & we need to separate them into two categories:
Category A: made of galvanized steel (factory-galvanized) & then coated with pure-polyster powder (for outdoor applications)
Category B: made of cold rolled ungalvanized steel (Black iron) and painted with epoxy-polyster powder (for indoor applications)
Please advise if there is any possible method to do so?
Thanks for your valuable time..
Product designer - Cairo, Egypt
First of two simultaneous responses -- March 18, 2008
You don't say if the galvanized parts are post manufacture hot dip galvanized or made from galv sheet?
There's s difference in the coating thickness that might be a way to tell these parts apart.
Assuming post manuf. HDGalv... Measure total coating thickness (galv
+ PC) and the parts with the thicker coating are galvanized.
If in galv sheet (much thinner zinc) this method might not differentiate.
To measure the total thickness, use magnetic system of measurement.
(various branded handheld devices available)
Another way - assuming that the bare steel parts are pretty identical: weight them. Galvanized parts heavier by about 6-8%
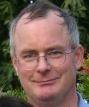
Geoff Crowley
Crithwood Ltd.
Westfield, Scotland, UK
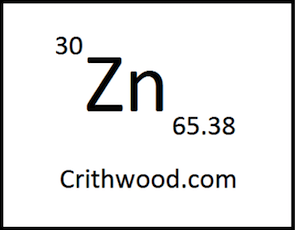
Second of two simultaneous responses -- March 19, 2008
probably with the help of elcometre you can,
the materials which are galvanized and powder coated shall have more coating as long as your powder coating is homogeneous.
regards,
- Sharjah, U.A.E.
Geoff,
Is the net zinc usage of 6% to 8% (plus 0.4% for ash and 0.6% for dross equals a gross zinc usage of 7% to 9%) what you expect for the average of many galvanizers or your gross zinc usage? Using quadraflux and IQM the net zinc usage is normally 3% to 5% resulting in a gross zinc usage of 4% to 6%. Economically this is a VERY important issue!
Ameen,
In the magazine Metal Finishing I published an article on magnetic thickness gauges in which I made about 200,000 tests using about 30 different gauges. For hot dip galvanizing, the most accurate gauges were made in the USA and Germany. They were the "banana" type and in a single measurement were accurate and precise. These gauges use a permanent magnet and must be calibrated on an attached coating. In an electronic gauges the principle is a variable core transformer (which is the non-magnetic coating and base steel) and a thin plastic unattached film is used for calibration. The electronic gauges gave poor precision on galvanized coatings.
Regards,
Galvanizing Consultant - Hot Springs, South Dakota, USA
March 21, 2008
Tom,
I was assuming that the galvanizing in question would be of the most likely gross Zn usage, not any specific thickness, as there was no info to assume any different.
I think there are relatively few galvanizers using Quadraflux, and based my assumption on that.
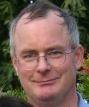
Geoff Crowley
Crithwood Ltd.
Westfield, Scotland, UK
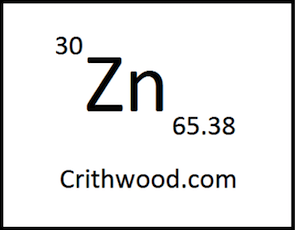
March 21, 2008
Q, A, or Comment on THIS thread -or- Start a NEW Thread