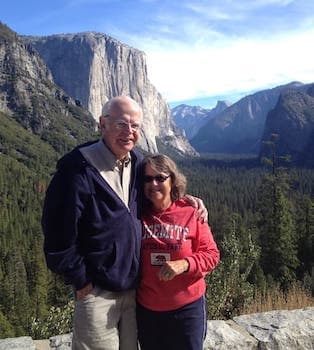
Curated with aloha by
Ted Mooney, P.E. RET
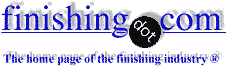
The authoritative public forum
for Metal Finishing 1989-2025
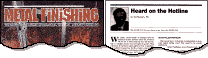
-----
Nightmare: Blisters when plating Pot Metal!
Q. I work in a small shop where we do a lot of old car parts. As many know most of the older emblems and trim are made of Pot Metal. We have serious issues with dealing in Pot Metal and have thought to just discontinue doing it all together. We get discolorations in the plating in all phases of triple chrome plating, blistering in the plating process in all levels that varies from just a few blisters to just horrible. Finishing the part to a smooth surface is not really an issue anymore. We have that down, but it seems if we plate more than once it is just never the same. Any help with how to deal with Pot Metal during the plating process would be greatly appreciated.
Dayna GomezPlating Shop Employee - Beloit, Wisconsin
March 15, 2008
A. Hi, I've never heard of the term "pot metal", but I assume its a zinc die cast?
I had problems when I first started chrome plating - ( private jobs for friends' cars, etc... don't tell my boss ! :-)
I had exactly the same problems you are having, and it was a simple problem to rectify - I was using too high a sulfuric acid between stages! Use 1% sulfuric acid and I guess your problem will be solved - because of the zinc content, any acid concentration that is too high will attack the zinc , causing a smutty surface, therefore causing your blistering problems; even a sulfuric acid rinse tank would be enough to cause you problems if there is too much acid in there.
Hope this helps, it worked for me!
- Essex, UK
March 18, 2008
A. You have not given enough information to figure out where the problem is. For the most part it is in the first copper plate. If you are not using a cyanide copper then you are already at a disadvantage. If you are using cyanide copper make sure that your bath is up to snuff. Most of the time it is a lack of free cyanide. But don't make any additions until you have it analyzed. Do not over clean the parts in your electric cleaners just give them a good soaking and scrubbing in your hot soak. Then rinse and a quick dip in your dilute acid bath and rinse thoroughly in a clean rinse before going into your cyanide copper. If you see little black speckles after about ten minutes then go back and do the whole process over again scrubbing the black specks off. If they speckle again then you have some kind of junk in the casting that has reacted in it over the years. I call it junk because nobody knows what it is. There are no experts that can tell you either. I have been doing pot metal for over thirty years and I have talked to other custom platers from all over the country and we all agree, it is just junk. At this point all you can do is put an heavy acid copper plate on it and hope it bridges enough over the junk to give you a good base to copper buff. Even then you might end up with small hard blisters, but at least you can color it out and proceed to put your nickel chrome on it. Sometimes that is all you can do. Pot metal is the most challenging stuff for any custom chrome plater. Once you think you have it figured out it screws up again. Heck, sometimes it will screw up on you and you strip it and do it again and it comes out perfect. You just have to try and find that sweet spot in between the junk. After all that you still have to figure how to not starve to death.
Frank DeGuire- St. Louis, Missouri, USA
March 20, 2008
A. The problem is that pot metal is supposed to be zinc die cast but it got its name from the fact that other available metals with a melt point at or below zinc often found their way into the pot. Therefore, a lot of pot metal contain lead. It is generally the lead which causes poor adhesion (blistering). If you examine the blisters this can be confirmed by seeing that the copper is peeling from the basis metal.
Generally, processing is similar to that for nickel plating leaded steels, a fluoboric acid pre dip. Lead is not soluble in sulfuric or hydrochloric acid and the processing through them leaves a smut on the surface. Lead is soluble in fluoboric acid.
- Great Neck, New York
March 20, 2008
A. I don't think lead in the casting causes the blistering. I regularly nickel plate lead parts by putting a cyanide copper plating on them first. Plus I have used lead solder (not lead free solder) to repair some pot metal parts and if anything the adhesion is better on the lead. I think the "junk" as I call it may be magnesium. The areas that blister usually have a black smut leaching out of the surface after cyanide copper plating. In some cases I have seen what looks like very fine white puffs on polished pot metal where there is no sign of aged corrosion such as pitting. But when I try to put cyanide copper on the part it starts a very fine fizzing and black leaching followed by blistering in the area of the white puffs. I have seen polished magnesium parts fizz and turn black in cyanide copper in just a few seconds. So I am only assuming the white puffs might be magnesium. But since I am not positive , I will just keep calling it junk.
Frank DeGuire- St. Louis, Missouri, USA
March 22, 2008
A. We do a lot of "pot metal" plating as well and we find that a pre-dip dilute fluoride bearing acid salt prior to a CuCN strike really helps.
Make sure that your CN bath is within parameters and try using "live" entry. Also, make sure your CN does not have Chrome contamination which happens if you use the same racks the whole way through your plating process. Chrome will cause blistering. Seems to effect pot metal more than steel for some reason.
You can remove chrome with sodium hydrosulfite
⇦ this on
eBay or
Amazon zincaffil links] (3g per 100gallons or so.) Then you have to remove the sulfur or your tank may start plating "red" in the HCD areas.
Acid Cu, buff, Nickel/Chrome plate.
Good luck!
- Middletown, Pennsylvania
March 28, 2008
A. To add to the very good information Jim posted, sodium hydrosulfite is an excellent chrome reducer for alkaline solutions, do not use this product in an acidic tank i.e. nickel.
Sodium hydrosulfite is considered a highly reactive material and is considered a flammable solid - reacts with moisture!
Some suppliers have non hazardous chrome reducers, some sell ones based on a blend of non hazardous materials and sodium hydrosulfite. Make an informed choice on what materials you prefer to deal with.
For the nickel tank sodium metabisulfite is utilized.
- Great Neck, New York
April 1, 2008
April 9, 2011
Q. I am trying to restore some antique pot metal parts.
Sometimes it is easy sometime is not. I see blisters after the coating
sometimes in copper sometimes after nickel
The problem is more frequently seen as the part is more damaged.
Doesn't matter if you polish it to a mirror finish it will blister
I would like to know what is the reason for this.
I suspect that is due to tiny pits inside the metal that carry solution from one tank to another creating a blister.
Any idea would be appreciated.
Thanks.
Plating shop - Bucaramanga Santander Colombia
A. After cleaning the organic soil, try a dip in 30% fluoboric acid followed by a copper fluoborate strike, then your regular plate.
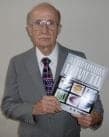
Robert H Probert
Robert H Probert Technical Services

Garner, North Carolina
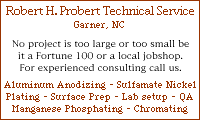
April 11, 2011
A. Really good & interesting posts. But also important is to consider the pre-pre-treatment, if I shall call so :-) But over-polishing prior pre-treatment and plating is quite common and can also cause blisters after parts has been plated.
Regards, Dominik
- Melbourne, Australia
April 14, 2011
May 9, 2011
Wow! This thread has been going on for three years. I still believe the "junk" as I call it in my earlier posts is the cause of the blistering. The pits in the metal usually do have very small capillaries running in them which can hold cleaning solutions and acid wash.
But I am still a firm believer that the "junk" that I mentioned earlier is the culprit. I know chromium contamination is bad for copper and especially nickel plating solutions. But if all the cleaning processes before plating are done correctly I don't think there will be any chrome solution left on or in the racks coating.
When polishing pot metal the whole idea is to polish out as many pits as possible. Sometimes while polishing a part you will try to chase a pit out and suddenly find a bunch of pits under the one you were chasing. That is not careless polishing. You are just trying to do the best you can and by the nature of the job it just backfires.
Plating old pot metal parts has always been one of the most difficult plating processes and as time goes on and the parts keep getting older it will be more difficult.
- St. Louis, Missouri, USA
Q. I too am having problems with pot metal. The part plates perfect EXCEPT in one or two spots it peels off down to bare pot metal. I'm using an alkaline or flash copper plating for my strike plate followed by acid copper.
Some parts are perfect and no problems. I try to do each part exactly the same and most parts plate good, some blister.Any suggestions?
- Belfast, Maine, USA
March 16, 2012
Q. Same as my other colleagues, we experience the same problem with pot metal and sometimes blistering also in some cast aluminum parts. Our plating process is the normal or regular one: repair the pieces, pass those to the polisher, then to the plater. First thing he will do is go to the caustic soak that we just changed for a better one (so called "soak 140") to remove all the compounds from the polishing. From there to clean water rinse. Then we etch/acid dip. Then to the non-cyanide copper -- and that's when our nightmare begins: BLISTERING AND MORE BLISTERING (after the copper strike and when not after the nickel)
My question is what are we doing wrong, or if there is a new solution to help our problem? We appreciate your comment, thank you. Gracias,
RUDY MELLADO- TIJUANA B.C. MEXICO
October 7, 2013
A. If you simply take a piece of heavily pitted pot metal and grind it smooth then polish it ready for plating you need to have another set of eyes look at it. What you will see if you make note of where the large pits were is a dark spot. Every one of those dark spots, which used to be a pit, will be a blister if you try to plate over top of the material.
The least invasive way to get rid of the blister potential is to sandblast out the dark material, but then you have a crater. You can copper plate and then solder the crater, then copper plate again and buff before nickel and chrome plating.
When I was polishing, it infuriated me to no end when parts I had polished would come back after copper plating full of blisters and had to redo them from the start so I had things straightened out with the sandblaster and made sure he knew what the heck his job was.
- Calgary, Alberta Canada
April 23, 2015
Plated 45 year old diecast tail lights haven't blistered yet.
Q. I am restoring a Riley Elf which has chromed diecast rear tail lights which were badly blistered. Recently I was fortunate to obtain new (out of the box) replacements. These new tail lights are not blistered at all.
The car was built in 1968, i.e., 45 years ago and the new lights (still in the Lucas boxes) were presumably made around that time also being kept in the boxes on the shelf in effectively the dark.
Why have these new tail lights not blistered given the lapsing of time?
I'll be interested in the reason(s) if known -- many thanks
- Nelson, New Zealand
January 12, 2016
![]() |
A. They haven't blistered because they haven't been exposed to the elements: rain, snow, ice, salt, road debris, harsh cleaners, etc. ![]() Jeffrey Holmes, CEF Spartanburg, South Carolina February 3, 2016 February 4, 2016 A. Hi Geoff ![]() Geoff Smith Hampshire, England |
Q. to active the zine or pot medal do I use for the bath. And what does the ph need to be?
Corey swiftElectrofinishing - Kent, Washington, USA
February 6, 2019
A. Hi Corey. Your question is a bit vague for me. Is this a new production job, or a single troublesome antique piece to be re-worked? If the latter, are you sure there is no trace of old plating? Three readers have suggested that fluoride activation followed by cyanide copper with a hot lead is probably required. Is this something you are familiar with, and trained & equipped to safely do?
Please try to introduce yourself and the situation because, as you read above, it is very unlikely that there is a "general" solution to this difficult problem. Thanks. Good luck.
Regards,
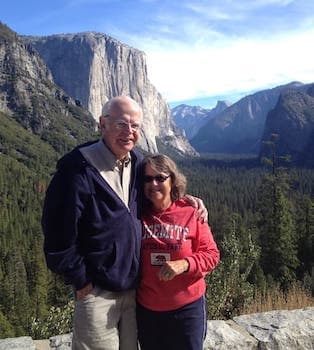
Ted Mooney, P.E. RET
Striving to live Aloha
finishing.com - Pine Beach, New Jersey
February 2019
A. "Pot" metal is a loose term that describes a wide range of mixed metals, most usually containing lead. Lead forms insoluble salts in most acids, especially sulfuric and HCl, so after cleaning the organics off, dip thru 20% fluoboric acid, then most people copper strike in cyanide. I have always wanted to strike in zinc cyanide but have never been able to talk anyone into it. Striking in copper fluoborate would be even better way to cover up the lead. As Ted Mooney says, send us more details.
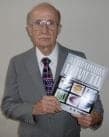
Robert H Probert
Robert H Probert Technical Services

Garner, North Carolina
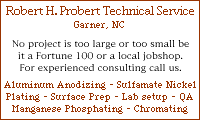
February 8, 2019

Q, A, or Comment on THIS thread -or- Start a NEW Thread