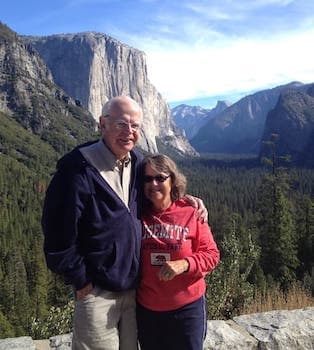
Curated with aloha by
Ted Mooney, P.E. RET
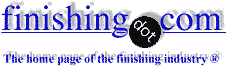
The authoritative public forum
for Metal Finishing 1989-2025
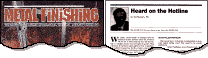
-----
Cracked hard chrome
March 13, 2008
Hi , I am a chrome plater for a major plating company , so I understand the micro-crack which occurs during the plating , but recently (after having new chrome plating solutions made ) very large cracking is clearly visible - sometimes even before grinding.
we have had the solution tested by an independent chemist , and all is well so I cannot understand why this problem is happening .
I have increased the tempeature of the solution and plated at a lower current/ surface area, which should have solved the problem , according to the many books I have read up on but with no success
.
I have noticed that it mainly happens on items such as aircraft repairs which need a very heavy deposit to bring them back to the required dimentions - (25-30 thou) . ( although I have done these jobs many times without any problems )
could the de-embrittlement have any cause to this problem ? 190/210 deg c.
many experienced and skilled people cannot work out what should be a simple problem ! could it just be a simple fact of too high deposit and a very hard plating solution ?
any thought and ideas would be gratfully received if anyone has experienced this problem before !
many thanks .
plater - Essex, UK
March 14, 2008
The last that I knew, Rolls Royce and the major USA OEM's would not let you plate that high a thickness per side. Are you talking about on a dia or pe side? Typical is sulfamate nickel, turned and then chrome plated. I agree with your opinion.
My guess is that you had impurities in the old tank that reduced the stress of the chrome plate.
I have plated 0.015 per side with 0.005 for grind using 140F, conforming anodes and a high ASF with no problem. The later years used HEEF 25.
- Navarre, Florida
March 17, 2008
Hi thanks for your thoughts , yes I agree , the required deposits needed are far too much - I measured some more of the same parts and they need 0.030 deposit - 0.060 overall ! due to the amount of base matrerial removed to remove the corrosion . these parts are under-carrage main casings ,but not for Rolls Royce - I'm sure NADCAP would not allow these parts to be plated if they were r/r parts.
I'm sure the excessive deposit required is not helping with my cracking problem . also because of the shape of the part , much more plating is required to enable the chrome to throw into the bottom corner and face . I think I'm fighting a losing battle with this job
, but it seems no-one else can plate them - or wants to .
I have increased the temp of the solution , and altered the current accordingly , conforming anode etc... I will find out tomorrow if I have been successful ! ( after 3 nights of plating !)
- Essex, UK
March 19, 2008
What you are being asked to do is like playing Russian Roulette with 5 bullets in the chamber.
I know that Boeing would not allow that much hard chrome and can not believe that any major one would.
If they will not allow a sulfamate nickel underplate, I think that they need to go to one of the high energy thermal deposition systems. Plasma is not high enough energy deposition for this use. There are several good ones from several vendors. Look at high velocity systems. They are not as expensive to use or install as a really good plating line and are great IF the operators and one or more managers are trained and allowed to do the parts correctly. No haz waste is a great advantage. No hydrogen embrittlement problems and a wide range of materials that can be used.
- Navarre, Florida
YOU CAN CHECK GRINDER IT HE SHOULD GRIND EACH PASS O.5 THOS AND COOLING SHOULD BE USED

Amman, Jordan
April 15, 2008
Q, A, or Comment on THIS thread -or- Start a NEW Thread