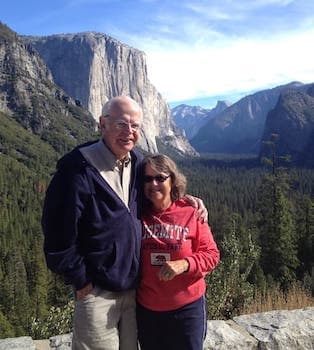
Curated with aloha by
Ted Mooney, P.E. RET
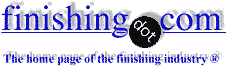
The authoritative public forum
for Metal Finishing 1989-2025
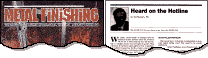
-----
Recommendations for Corrosion-Resistant plating on Case Hardened Parts?
March 11, 2008
Dear finishing experts and enthusiasts around the world,
We are looking into a project that requires the part to be case hardened to 60Rc with a minimum case depth of 1.27 mm, and we require those parts to be corrosion resistant as well. (The material of the parts is to be SCM415 - a type of case hardening steel). Besides that, please take not that the surface roughness of some features of the parts or the Ra of the parts needs to be 0.4 microns or better. I have summarized our requirements for the parts as below:
1. Parts to be case hardened up to 60 Rc (Rockwell Hardness) with a case depth of 1.27 mm.
2. Parts to be made out of SCM 415 - a type of Case Hardening Steel.
3. Parts requires a coating or finishing that will give it corrosion resistant characteristics.
4. Parts have complex geometries and has features that requires very tight tolerances.
4. Grinding will be required to ensure some features of the part has a Ra of 0.4 microns or better.
5. The commencement of the grinding process will largely depend on the type of finishing chosen. I would presume that grinding will be performed after CASE HARDENING but BEFORE the corrosion resisting finishing is applied. This of course, as mentioned previously, depends on the thickness as well as the roughness of the finishing coat.
After explaining the requirements for the parts we are to manufacture, my questions are as follow:
1. What will be the appropriate finishing that can offer corrosion resistant characteristics to parts that have ALREADY undergone the CASE HARDENING process?
2. If there is a recommended corrosion resistant finishing that can be applied to HARDENED parts,
a) then what will be the thickness of the finishing coat?
b) Besides that, will the finishing coat make the surface roughness to change a lot?
3. When should the grinding process be done?
a) AFTER Case Hardening but BEFORE finishing coat.
b) AFTER Case Hardening and AFTER finishing coat.
4. After reading through some letter at Finishing.com, I found that the phenomena called "Hydrogen Embrittlement" will occur if HARDENED parts are being treated with acid prior to plating processes, such as Zinc plating. Is this correct? If yes, then it would be great if anyone can tell me whether the Hydrogen Embrittlement will occur for the following finishing that I have listed down as below.
I did some research before I posted my questions here and would like to share my findings with all of you for your reference. Based on my research, I found out that for hardened parts, the normal process would be to apply the following finishing/plating to give the parts corrosion resistant characteristics:
a) Hard Chrome
b) Electroless Nickel Plating (EN)
c) Passivation (Not too sure about this)
d) MECHANICAL Zinc Plating
I will discuss each finishing in sections as below.
Hard Chrome
Hard Chrome can achieve extremely hard surfaces as well as exhibiting corrosion resisting characteristic. Wear resistance is also very good. Hard Chrome thickness can vary from 0.0002" to 0.050", I understand.
The disadvantage of applying hard chrome would be the decrease in its fatigue strength as mentioned here:
nhml.com/resources_NHML_Hard-Chromium-Plating.php
Question:
HC I) Can certain features of the part be covered and not exposed to Hard Chrome finishing during the Hard Chroming process?
HC II) Can this process be applied to Case Hardened parts and will Hydrogen Embrittlement occur?
Electroless Nickel (EN)
This seems like the best bet considering the requirements of our parts as it has the following characteristics:
- Uniformity of the deposits, even on complex shapes.
- Able to hold extremely tight tolerances.
- Excellent corrosion resistance.
- Low coefficient of friction
- Deposits are often less porous and thus provide better barrier corrosion protection to steel substrates, much superior to that of electroplated nickel and hard chrome
- The deposits cause about 1/5th as much hydrogen absorption as electrolytic nickel and about 1/10th as much hard chrome.
- Deposits can be plated with zero or compressive stress.
- Deposits have inherent lubricity and non-galling characteristics, unlike electrolytic nickel.
- Deposits have good wettability for oils
- In general low phosphorus and especially electroless nickel boron are considered solderable. Mid and high phosphorus EN's are far worse for solderability
- Deposits are much harder with as-plated microhardness of 450 - 600 VPN which can be increased to 1000-1100 VHN by a suitable heat-treatment
Question:
EN I) Can this process be applied to Case Hardened parts and will Hydrogen Embrittlement occur?
Passivation
A friend of mine mentioned that this process will work as well as passivation is mainly used to form a layer of corrosion resistant film on the outer surface of the parts. However, from what I have found so far, I seem to think that passivation can only be applied to Stainless Steel. Can it applied to case hardening steels such as SCM
415? Please advise or offer your comments on this finishing option.
Mechanical Plating
It seems that this method of zinc plating is one of the most common ways for applying a corrosion resisting coating on hardened parts but I am not sure whether it is suitable for our case. From what I have gathered, mechanical plating is basically mixing zinc powder and other ceramics or chemicals together with the parts and all this will be loaded into a barrel where the mixing of the contents will be done. This method will eliminate the Hydrogen Embrittlement phenomena as I have read from other posts at Finishing.com. However, I also noticed that this process is more suitable to small parts and the surface roughness is not a critical factor. For my case, the parts are generally larger than screws (some reaching Outer Diameter of 125 mm) and there are certain features of the part that requires a smooth surface with a surface roughness (Ra) of 0.4 microns or better. So I am not too sure whether this plating process is suitable or not. Besides that, the availability of suppliers that offers mechanical plating in my area is also another consideration.
Based on the 4 options above, I would think that Electroless Nickel seems to be the best option, but I have not seen it being mentioned that it can be applied to Case Hardened parts. I am not sure whether this can be done or not. Your feedback and response to my list of questions as mentioned above will be highly appreciated!
Looking forward to feedbacks and comments and please feel free to correct me if I made a mistake in some descriptions of the various types of plating.
Thanks in advance!
Best Regards,
TK
Buyer - Malaysia

Q, A, or Comment on THIS thread -or- Start a NEW Thread