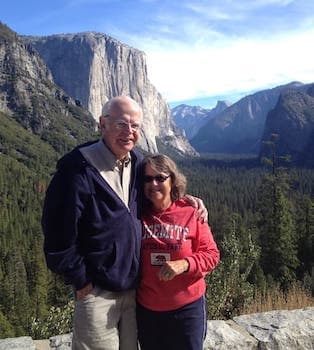
Curated with aloha by
Ted Mooney, P.E. RET
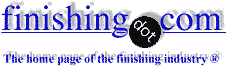
The authoritative public forum
for Metal Finishing 1989-2025
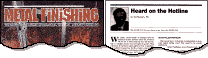
Thread 480/74
Hard chrome plating problems

Q. Hello,
I have issues with hard chrome plating:
1. Rod size Dia 550 mm - Length 5 meters - hollow rod
2. Temperature is 60-65 °C, am using heat exchanger
3. I set current to 17k
4. Chrome deposited only on two round portions with 15 micron /hours -- rest of rod comes without any chrome [zero micros)
Employee - Saudi Arabia Jeddah
May 8, 2024
publicly reply to Ammar Mukhtar
Q. Hi
Still having issues with hard chrome plating for hollow tube with Dia 550 mm- Length 4200 mm? I have tried a lot, chrome does not stick on rod.
Materials lab analysis is ok, anodes are new, use amps control with 17k, temperature vary from 60-64 °C
Ammar Mukhtar
Employee - Saudi Arabia Jeddah
May 8, 2024
publicly reply to Ammar Mukhtar
A. What is the density of the current, expressed in amperes per square decimeter (a/dm2), is observed on these details?
If we take your measurements h = 5000 mm and d = 550 mm, then the total area S will be 863.5 dm2. Given the current strength of 17000 A, it turns out that only 19.6 a/dm2 to the surface of the part, instead of the necessary 35 a/dm2. This leads to the fact that the coating develops only in areas with increased current density - at the ends and the beginning of the part.
Another potential problem affecting the process is the insufficient area of the anodes compared to the area of the part (it should be 2: 1 or at least 1.1: 1). Based on the photograph of your bath, they are difficult to see, but we can assume that they are not enough. The small area of the anodes, if so, can provoke the appearance of trivalent chromium in the electrolyte, which will reduce the roof capacity of the electrolyte, and as a result the coating will besiege even worse.
If the opportunity to conduct precipitation on the Hull cell?
- Nizhniy Novgorod
May 29, 2024
publicly reply to Nik Erm
A. I suggest lower your temp to 56-58 °C.
Since your rod is hollow, it itself is getting heated up in the process of being plated and causing the temperature to rise around the area to be plated.
Wish you good luck
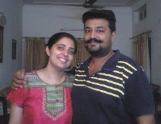
Vikram Dogra
Irusha India - Chandigarh, India
August 29, 2024
publicly reply to Vikram Dogra
⇩ Related postings, oldest first ⇩
for Shops, Specifiers, & Engineers
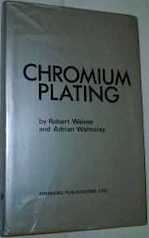
by Weiner & Walmsley (1980)
avail from eBay, AbeBooks, or Amazon
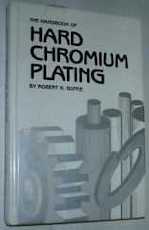
by Robert K. Guffie (1986)
avail from AbeBooks, or Amazon
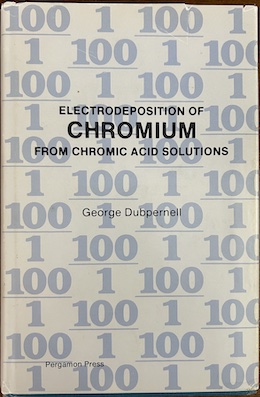
avail from eBay, AbeBooks, or Amazon
"Hard chromium plating: A Handbook of Modern Practice"
by John David Greenwood (1971)
avail from eBay
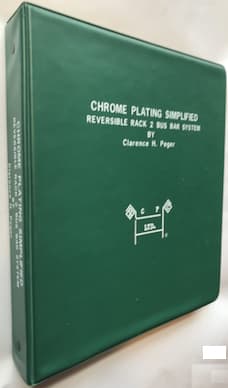
very rarely avail from Amazon
but copies are available in a few libraries)
"A Chromium Plating Bath With The Fluoride Ion"
by Alfred Perlenfein (2013)
avail from eBay, AbeBooks
(as an Amazon Associate & eBay Partner, we earn from qualifying purchases)
Q. I have following problems:
1. Hard chrome plating on case carburised SAE 8620 material develops porosities on plating.
2. Some rotors supplied , duly hard chrome plated, by sea for export had chrome plating lifted up.
3. In many cases, like plating on SS 316, plating is peeled of while plated components run with contact of rubber shell.
4. Please tell best precautions to be taken during hard chrome plating operation.
J.K. Saraswat- Delhi, Delhi, India
2002
publicly reply to J.K. Saraswat
A. About hard chroming: Make sure that the stainless steel is given a good reverse etch in a separate chrome tank reserved for this purpose, otherwise you risk contamination with nickel and trivalent chromium. Also be watchful of operating temps.; allow job to warm up in solution. About the hardened steel: this has given me grief in the past, also particularly tuftrided crank journals, steels with moly in and nodular steel and iron cranks. I have found the newer high speed deposit chromium solution a bit more temperamental regarding adhesion. I converted back to the old formula and the thou per hour trade off is, I think, worth it for less stuff ups. Just check that the rubber in contact is not chattering, or it might be screeming the plating off, like needle rollers do.
Best wishes, mark
- nsw australia
publicly reply to mark gunn
Multiple threads merged: please forgive chronology errors and repetition 🙂
Q. I am writing you concerning some chrome plating problems that we are incurring when having wrenches plated. We are an investment casting company and subcontracting our plating process. We are casting 6150 steel open end double end wrenches. We are then putting the wrenches in the vibrodyne with ceramic media for 10 hours to get a better surface finish and then sending the wrenches out to get heat treated. After returning from heat treat we then vibrodyne the wrenches once again to remove any scale on the surface of the wrench. The wrenches are then sent to a chrome plater to have copper-nickel chrome put on them. The wrenches are then baked for 6 hours to remove any hydrogen embrittlement after plating. We have sent the wrenches to two different platers and have incurred two different problems. I was wondering if you would know how to solve either problem.
Problem # 1
The wrenches have a haze or cloudiness to them along the edges and the chrome is darker and shinier down the middle. It looks as though something had ran down the wrenches or didn't dry properly. The wrench also has many pits that show through the chrome after being plated. The finish looks speckled or metallic from the pits. (This plater has an automatic line).
Problem # 2
The plating is flaking off or bubbling up after being baked. The wrench looks great going into baking, but after baking some of the plating chips off and the metals shows through. Some of the spots only go down the copper, but most spots are down to the metal. There are still minor pits in the finish with this problem, but not as many with the other plater. This plater has a manual line.
We noticed that the wrenches have less pitting going into being baked compared to the number of pits after baking. We were also wondering why this is occurring. We are trying to solve these problems ASAP. We are looking for a bright and smooth chrome finish. Do you have any suggestions? Thank you for your time and considerations.
Matt Jacksoninvestment casting - La Porte, Indiana, USA
2005
publicly reply to Matt Jackson
A. Problem one really needs a hands on inspection of process at site. But you can check out post plate rinsing for a start, The rest needs a look in person. Problem two appears to be the result of poor pre treatment practice and perhaps bad solution maintenance. At this distance this is the best one can suggest.
Regards,
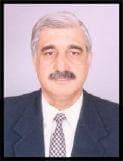
Asif Nurie [deceased] [deceased]
- New Delhi, India
With deep sadness we acknowledge the passing of Asif on Jan 24, 2016
publicly reply to Asif Nurie [deceased]
A. PROBLEM:-
1. BUBBLING:- IMPROPER CLEANING, INTERRUPTED CURRENT.
2. CLOUDINESS:- HIGH TEMP, LOW CURRENT, BATH OUT OF CONTROL.
3. PITTING:- GAS TRAPPED.
FIRST COMPONENT SHOULD BE POLISHED, THEN CLEANED PROPERLY, AFTER THAT PLATING.
1. SOAK CLEANING
2. WATER RINSE
3. ANODIC CLEANING
4. WATER RINSE
5. ALKALI NEUTRALIZED
6. ETCHING,CHROMIC ACID
7. PLATING HARD CHROME
8. DRAG OUT
9. DRAG OUT
10. DRAG OUT
11. CHROME NEUTR.
12. HOT WATER.
13. DRY.
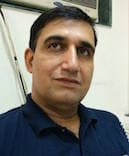
Ajay Raina
Ludhiana, Punjab, India
publicly reply to Ajay Raina
Multiple threads merged: please forgive chronology errors and repetition 🙂
Q. We have in our workshop a chrome bath with about 6000 ltr chromic acid, with 12000 Amperes available, 12V supply.
The main problems is Grey shadows in the chrome layer, and also pitting.
The chrome is also not so hard as it used to be.
The materials this appears on is regular ST52.3N and SIS 2387, all ground and polished before chrome plating.
We also do chemical cleaning and activation on the rods we chrome.
We have checked the power supplies and also the acid but we cannot find out what is wrong with this.
We would be really happy to hear from someone with deep knowledge in hard chrome plating.
Best regards,
Plating shop/hydraulic repairs - Trondheim, Norway
March 6, 2008
publicly reply to Anders Aronsen
A. Hey there,
you did not write anything about your latest analysis results. Also, are you using a catalyzed bath, then you should also consider doing an analysis.
Good Luck,
Dominik
- Mexico City, Mexico
publicly reply to Dominik Michalek
A. Hello Anders,
Do an analysis on the chromic acid for contaminants like iron, aluminium, copper, trivalent chrome. Control the anodes so they are active. I think the ratio between chromic acid and sulphate is wrong.
Read my article about chrome plating in the library here on finishing.com
Regards,
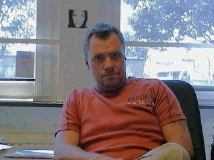
Anders Sundman
4th Generation Surface Engineering
Consultant - Arvika,
Sweden
publicly reply to Anders Sundman
A. Hi, I'm a hard chrome plater and had very similar problems when I started. The pitting could be many things, from the parts being porous, poor cleaning & etching, and even the wax used for masking.
Sometimes if your wax is dirty or contaminated, you can see rust (like pitting) through the glycerine after you have done the first part of the masking.
Also leaving work in the hot wax too long can cause pitting problems if your wax is dirty (some people de-mask in the wax tank, therefore contaminating it with chemicals and water, etc.). A new wax put an end to my pitting problems --simple but not something people think of!
As for your grey discolouration, have you had an analysis of your solution? Are the anodes clean? Is the vat stirred after being topped up (cold water sits on top and causes burning to the part)? Sounds silly, but a guy from another plating firm visited my factory and asked why I stirred the vats - then he said his parts looked grey and horrible!
The newer the solution, the brighter the finish and also the chrome is harder; but it does dull down with age -- maybe its time to renew yours ?
- Essex, UK
publicly reply to Jay Smith
A. Could be:
-shadowing from an edge
-etching too long, not long enough
-etching current too high
-plating current too high, calculate using L*D*3.1416 for 1thou an hour plating current.
-temperature too cold
Could be a number of things, guide me through your plating process and I may be able to help you.
- Perth, WA, Australia
publicly reply to Mike Hunt
Q. I'm John. We are needle manufacturers doing hard chrome plating on needles.
Since a couple of months we're facing blackness at LCD area.
What can be the reason if anyone can help?
Needle manufactures - India,Chandigarh
May 7, 2018
publicly reply to Parmod Jangra
Ed. note: While awaiting help, please send photos of these needles for posting here, by attaching them in e-mail to mooney@finishing.com. A picture is worth a thousand words. Thanks.
A. Hi John,
While pending defect part photo for ref, you may verify below possible causes:
1. Too high metallic impurities content in plating solution.
2. Too low cathode efficiency at LCD area.
3. Poor bath solution wetability.
4. Operating parameters out of control (Cr, specific gravity, pH, complexer, temperature, etc).
5. Insufficient barrel movement if doing barrel plating.
6. Inadequate post rinsing and drying.
Regards,
David
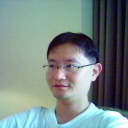
David Shiu
- Singapore
publicly reply to David Shiu
Q. We have tried to resolve this coating problem in our shop.
We are coating dia. 750 and length 2200 Steel industry Rolling Rolls.
Problem is shown in attached images.
Bath temp. 47 °C for etching and time is 30 sec.
52 °C for coating.
Solution concentration of CrO3 = 230 gm/l
And H2SO4 = 2.3 g/l
Please give us valuable suggestion.
Roughness after Shot blasting is 3 to 4 microns
- India
September 24, 2019
publicly reply to Vishal Patil
A. Main cause cold be improper working of Anodes, secondly lower current density, thirdly are you using heat transfer equipment to cool the temperature of the tank during plating operation? If not, rise in temperature could also be a cause of non plating. This can happen also due to excess etching at the particular area due to more active anodes.
Mahendra Gargatti- Belgaum KARNATAKA INDIA
November 25, 2021
publicly reply to Mahendra Gargatti
A. I am working as Production engineer in Hard chrome shop.
Our job sizes
Dia 80 x lenth 1000mm, Dia 90 x length 1000 mm.
I have faced this problem 2-3 times.
You have to increase your bath temperature between 55-60 °C. Etching temp 50-55 °C.
Also need to increase chrome concentration between 250 to 300 gm/lit.
Sulphate ranges from 3.2-3.5
- Sangli
February 16, 2024
publicly reply to Akash Pawar
Q. Dull Gray Deposit Hard Chrome?
Hi. Over the last few months we have started to develop issues with our hard chrome. We have not used the tank in quite some time other than to run monthly test pieces to ensure it is good to go when production picks up. It looks like the parts are burning but not in the high current density areas of the part but in the lower density areas or middle of the part. I just ran a test sample the other day (6" long x 2.5" diameter @ about 100 amps) and 1" on either end was shiny chrome as would be expected but the middle 4" was a thick dull gray. I am in the process of obtaining an Hull cell to hopefully help determine the cause. As I said we haven't been using the tanks, so not sure how the chemistry of the bath could have gotten out of whack. Also we send samples out annually to check for impurities and everything seems well below limits. Thought maybe the anodes had passivated but I would think that this would have the opposite effect and would not plate at all. Any thoughts or advice would be greatly appreciated.
Ron Hafemann- Kelowna B.C., Canada
March 24, 2021
publicly reply to Ron Hafemann
A. Hello Ron
You did not mention if you use a conventional Chromic-Sulfuric bath? What is the bath temperature? Do you use a stick anodes or conforming anode? What the distance from the anode to the part?
If you got a dull grey Cr plating in the middle, there is a chance that current is a little too low. Based on your data, the current density is ~300 ASF. It should be a good set point, but probably there is some current robber (fixture?). Try to run same test again with a little higher current ~350ASF --> 115 amp and verify the bath temp.
Good luck
- Winnipeg, Canada
publicly reply to Leon Gusak
Hi Leon
Thanks for the input. Yes it is a conventional chromic/sulfuric bath which we run @ 130 °F. The anodes are 3" wide and for the last test piece run, about 4-5" away. I did scrub down the anodes which did make a considerable difference which makes me think the anodes had passivated. The part went from the 4" wide band of dull grey chrome all around, to a couple of 2-3" patches of grey nodules. So heading in the right direction and will be running the same test piece tonight at higher amperage.
Cheers,
Ron
- Kelowna, B.C., Canada
publicly reply to Ron Hafemann
Q, A, or Comment on THIS thread -or- Start a NEW Thread