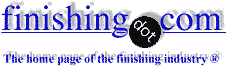
-----
Galvanizing ash or flux contamination of work
February 28, 2008
Q. Greetings from Australia. After long holdups largely related to the shocking price of zinc, the hotdip galvanizing plant that I've previously posted about is up and running.
9 metre long tanks and kettle, hot caustic, hot inhibited sulfuric, hot quad flux, lead bottom kettle with 30 ppm aluminium in the zinc, quench. First batch of 190 items wired to a frame, total weight about 1.5 tonne, 100% acceptable.
But not perfect, hence this post.
Flux is allowed to dry, so work enters zinc with not a sign of spatter. Starting about 5 seconds after immersion and lasting about 10 seconds, slight bubbling which I assume is the flux doing its work. Surprisingly large amount of white smoke.
But within seconds of the slight bubbling, we got a thin film of light coloured fines over the bath. When the work was withdrawn, this film was picked up by the top surfaces of the jobs giving a rough surface to the zinc coating on those top surfaces. The rest of each job was completely clean, as each job came up through the clear patch created by its top surface.
A quick run over with a hand grinder cleaned the roughness off, but the film shouldn't have been there in the first place.
Possibilities that have occurred to me are (a) fine dross suspended in the bath from the original meltdown and pushed to the surface by the flux on the jobs; (b) quad flux reacting with aluminium in the bath, more than would happen with triple salt flux - the great amount of white smoke suggests the possibility of aluminium chloride. The film was still on the surface of the kettle 12 hours later, with the clear areas still in it from where the jobs had come out.
But these are only thoughts about what might be the nature and cause -- I hope somebody can suggest what actually is the nature and cause, so that we can stop it happening.
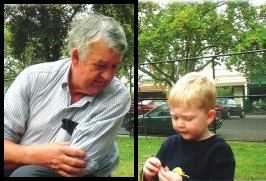
Bill Reynolds [deceased]
consultant metallurgist - Ballarat, Victoria, Australia
We sadly relate the news that Bill passed away on Jan. 29, 2010.
![]() |
A. Bill ![]() Geoff Crowley Crithwood Ltd. Westfield, Scotland, UK ![]() February 29, 2008 February 29, 2008 A. Sir: Galvanizing Consultant - Hot Springs, South Dakota, USA March 2, 2008 A. Sir: Galvanizing Consultant - Hot Springs, South Dakota, USA |
March 3, 2008
Q. Hi Geoff and Thomas
Thank you both for your responses. In our innocence, we anticipated that a clean zinc surface going in would give a clean zinc surface coming out - the concept of needing to skim while immersed hadn't occurred to us. Your advice, Geoff, goes direct to the heart of our problem.
The tanks and kettles are 9 meters to accommodate the large beams and columns that will be part of the work load. But on our first production batch we used all small items (190 of them), not long beams etc, and wired them to use the full area of the lifting frame and kettle. Paddling between the wires in such a case is just not practicable. Under other circumstances, with several large jobs on the frame instead of hundreds of small ones, skimming between the wires would be easily enough done.
My thoughts now are to both reduce the amount of flux on the work and avoid skimming between the wires, by...
(1) add a surfactant (pentaerythritol?) to the flux to get better draining and hence less flux on the work;
(2) try coming out of the flux at creep speed rather than normal hoist speed (same slow speed as coming out of the zinc) and see if that also gives less flux on the work;
(3) on small work, use only half the length of the kettle - go in clean at one end then move the frame to the other end while immersed.
Do these sound sensible intentions?
I chose to use quad flux right from the start in the light of Dr Cook's many postings and publications on the subject of fluxes, and hope to be able to stay with it (or at worst somewhere between triple and quad).
The details that Dr Cook requested about the other aspects of plant operation seem not to impact on our surface crud problem. All the maths were right, and the caustic, sulfuric and flux tanks are all run at 70 °C and are not giving any problems. The kettle has
220 tonnes zinc + 24 tonnes lead, is pulse-end-fired and held at 448-450 °C. Aluminium is added as 10 kg bars of 4% aluminium (die-casting) alloy.
Thanks again, and we'll be grateful for your comment on this post.
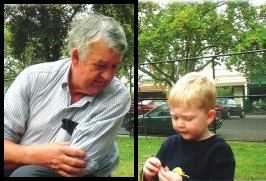
Bill Reynolds [deceased]
consultant metallurgist - Ballarat, Victoria, Australia
We sadly relate the news that Bill passed away on Jan. 29, 2010.
![]() |
March 4, 2008 ? Geoff, Galvanizing Consultant - Hot Springs, South Dakota, USA March 4, 2008 A. Bill, Galvanizing Consultant - Hot Springs, South Dakota, USA March 4, 2008 A. Bill, ![]() Geoff Crowley Crithwood Ltd. Westfield, Scotland, UK ![]() |
A. Bill,
I am always concerned about the short and long term safety and heath of workers. In your design did you put in an enclosure around the kettle? If so what type? If not, do you have a shield with a safety glass window so that during immersion into the zinc the kettle crane man (and skimmers) can get behind it to avoid zinc spatter? Do you have audio and flashing lights alarms during immersion in the zinc? Triple and quadraflux are "sleepers" in that 99% of the time there is little kettle spatter, whereas a pocket weld or lack of proper product venting will cause dangerous explosions in the kettle. In the USA while a galvanizer was dipping a heat exchange coil it blew up spattering zinc onto a worker, who, until he died was called the "tin man." Also be aware that the hollow steel tube handle of an ash skimmer shot a molten ball of zinc into a workers head, he died. I have never figured out the physics of this "rifle" handle, but it did happen and perhaps by acid cleaning the skimmer. About one third of my clients use wooden skimmers, both regular wood and fire retarded wood. They last a few hours to a few days, and there are ways to make them last longer.
My article "Accidents and Hazards in Hot Dip Galvanizing is in the journal Metal Finishing. It was NOT a well-received article by the industry, but if one worker avoided serious injury it was worth the bad feed-back.
Most accidents happen to "visitors." If most or all of your workers are new to hot dip galvanizing, perhaps you could hire a galvanizer to speed your learning curve.
Regards,
Dr. Thomas H. CookGalvanizing Consultant - Hot Springs, South Dakota, USA
March 7, 2008
March 7, 2008
A. Bill, Here are 25 year old, never published, test results of bag-house-dust (as percent).
Type Use Zn NH4Cl Pb Fe Al Cr Cd
Wet Job 4.9 19.5 .012 .135 .037 .079 .001
Wet Spin 4.5 1.1 .010 .140 .088 .002 .004
Dry Job 2.5 1.3 .013 .125 .049 .021 0
Dry Job 12.0 12.6 .120 .400 .370 .002 .001
Dry Job 33.8 33.7 1.26 1.25 .479 .004 .006
Dry Job 37.5 28.6 1.03 1.20 .432 .004 .006
Dry Sheet 4.2 21.2 .009 .045 15.2 0 .001
These data need additional duplication before publishing.
Regards,
Galvanizing Consultant - Hot Springs, South Dakota, USA
Again gentlemen, thanks for your very helpful comments.
As if anticipating your suggestion, Thomas, we were able to get the ex-foreman of a galvanizing plant that was shut down a couple of years ago, to advise on the tricks of manipulating things on the shop floor. He spent this last Friday and Saturday observing and advising, and the skimming after immersion that Geoff kindly described in detail is now described by the plant operator as "a piece of cake". I wasn't at the plant at the weekend, but believe the work was coming out quite clean.
He (the ex-foreman) also expressed surprise at the large amount of white smoke relative to what he used to get using straight triple salt, so we are adjusting the flux back a bit from quad (actually to about 3.2-salt) and dropping its density slightly. Over the months to come, we will play around with that a bit and find the best balance for that plant and type of work between the flux ratio and density and the white smoke and the flux consumption and the zinc coating thickness etc etc...
I'll bring you up to date with operating details later, if the plant owner permits me to.
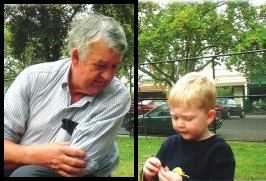
Bill Reynolds [deceased]
consultant metallurgist - Ballarat, Victoria, Australia
We sadly relate the news that Bill passed away on Jan. 29, 2010.
March 11, 2008
March 12, 2008
? Bill,
What is 3.2 flux?
Regards, Tom Cook
Galvanizing Consultant - Hot Springs, South Dakota, USA
March 13, 2008
A. Bill,
I figured out what you mean by 3.2 flux. This flux would be 0.2 units from Triple salt and 0.8 units from quadraflux. This would be a flux with an "ACN" of 1.258. "ACN" = %ammonium chloride/%zinc chloride. ACN for double salt is 0.785 (ZnCl2.2NH4Cl). For triple salt ACN is 1.18 (ZnCl2.3NH4Cl). For Quadraflux ACN is 1.57 (ZnCl2.4NH4Cl). It is not likely that a flux formulator would be knowledgeable in chemical "moles," which is why I like ACN terminology.
In 1972 I tested a galvanizer's flux who had never used anything but triple salt (ACN=1.18). The test results showed an ACN of about 0.7. During galvanizing some rejects had been brought back and only refluxed, dissolving zinc into the flux solution as zinc chloride. Thus the ACN goes to a lower value AND the pH goes UP. We added 2,500 pounds of ammonium chloride to the 5,000 US gallon flux tank and the galvanizing got much, much better (e.g. zinc coating thicknesses were greatly reduced as were drips, icicles, and many fewer rejects).
For an article in Metal Finishing, I made up a flux solution in which I put 1 kg of ammonium chloride and 1 kg of zinc chloride (e.g. ACN=1.00) and had 12 test companies test for ammonium chloride and zinc chloride (Fig. 4 in the article). NONE of these "certified" companies got a usable result for ACN, even though they charged between $50--$300/sample. I also had them test sulphate and iron and about 20% of these companies got usable results.
Your new guy (who worked for a previous galvanizer) was probably accustomed to a flux which he thought was triple salt but in reality had an ACN near or below double salt. The South African's had an ACN of about 0.5 and a baumé of about 40. I took out 3/4 of the old flux solution and added 4 tons of ammonium chloride and water and a good surfactant. I also heated the tank to 71C. The reduction of zinc used was $8,000/day (when zinc was cheap). They took me to Kruger Park on a long weekend for a look see. Your new guy will bring with him all of his good knowledge AND some knowledge that is NOT so good. For example, it is never a good idea to put zinc floor sweepings or dross or ash into the flux tank (to neutralize carried over acid). The technology is simple but you must know and understand what works.
In-plant ACN testing, in-plant iron, and in-plant sulphate testing are readily available. You need these for testing your flux and (sulphate testing) for your spray rinse water. I expect that your flux tank will become contaminated with sulphate within a year due to your spray rinse system.
Regards,
Galvanizing Consultant - Hot Springs, South Dakota, USA
March 14, 2008
A. Bill,
There are so many, many important items in constructing and operating a galvanizing plant, I am concerned, that things are likely to get screwed up fairly soon. The owners of the plant expect to make a profit above their investment and operating costs. The "floor" galvanizer that you just hired comes from a plant that was shut down a few years ago. Why?
Your owners have invested a few million dollars to build the plant (according to some of your recommendations), it is time to invest a few thousand dollars on the best galvanizing consultants you can find to make sure that it operates as you have designed.
Regards,
Galvanizing Consultant - Hot Springs, South Dakota, USA
Q. Can you brief me of in-plant testing method of sulphates in Flux & rinsing water . What are the chemicals required, what are the apparatus & what is the method.
Rajesh Mishra- Vadodara, Gujrat, India
January 4, 2009
Soft ash deposits on galvanized steel
November 13, 2019Q. Hi everyone
We have a customer who galvanizes cable ladders, they are battling with a soft ash deposit that sits on the material after galvanizing and doesn't roll off like some ash does but has to be washed off. There isn't a black spot under this ash but it is unsightly and creates an issue to have labour remove this.
Soft ash deposit:
Same deposit wiped down:
After rinsing the deposit off completely, no bare spot:
They skim before and after these ladders are dipped, flux is good SG 1175, pH 4.3, iron 1.2%; are there any suggestions to reduce or eliminate this type of ash?
Best regards
Donavan
- South Africa
November 21, 2019
A. You didn't say if you quench / passivate after HDG. If so most of this problem should get washed off in the quench tank.
But it is the galvanizers responsibility to remove it under ISO 1461.
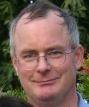
Geoff Crowley
Crithwood Ltd.
Westfield, Scotland, UK
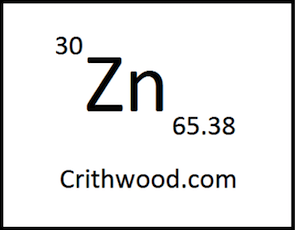
November 21, 2019
Q. Hi Geoff
Thank you for your response.
Yes they do quench in a passivation tank and most of the loose ash comes off in the quench, however this soft ash deposit as shown in the photo doesn't.
They do remove it manually but it is time consuming and didn't used to happen so they want to find out what causes it.
Looking forward to your thoughts/ suggestions.
Best regards
Donavan
- South Africa
by Larry Durney
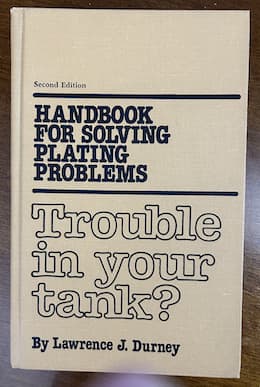
on eBay or Amazon
or AbeBooks
(affil link)
A. Hi Donovan. I appreciate your postings and certainly don't want to discourage them, but something that Geoff hasn't addressed yet but which is mentioned here constantly is: it is extremely difficult for two parties -- neither of which is actually there and doing the finishing -- to resolve the causes and effects of defects :-(
When 'something has changed' but the questioner doesn't know what it is that has changed, the first step is invariably to 'walk the line' from receiving dock to shipping dock, which is usually the first step in asking the right questions :-)
Best of luck, but please walk the line or see if someone who has can jump into the conversation. Thanks!
Regards,
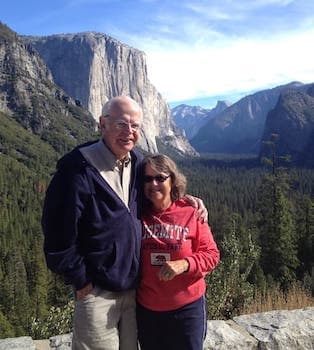
Ted Mooney, P.E. RET
Striving to live Aloha
finishing.com - Pine Beach, New Jersey
November 2019
A. I didn't pick up on the fact that the post wasn't from the galvanizer, sorry. Something sure does seem to have changed, and the sudden onset of excessive flux adhesion like this, persisting after quenching, looks likely to be a flux chemistry issue. That would be a good starting point to do what Ted suggests - walk the line - and see what changed when this started appearing. Did they top up the flux tank? Make up a new tank? Clean out the tank? Change supplier of flux? Change concentration? Change ratio (the ratio between ammonium chloride and zinc chloride - usually in ratio of 2:1, 3:1 or sometimes 4:1)
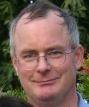
Geoff Crowley
Crithwood Ltd.
Westfield, Scotland, UK
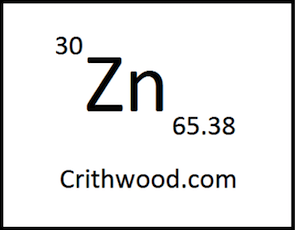
November 28, 2019

Q, A, or Comment on THIS thread -or- Start a NEW Thread