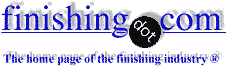
-----
Comparison of accelerated corrosion testing
2000
We currently chloride zinc plate w/clear chromate and also add a potassium silicate leachant seal to a CRS product. Process is barrel plate. We suffer from customer field failures defined as white corrosion. This is considered a rejection by our customer although we know that it is the zinc sacrificing itself rather than the steel. Accelerated salt spray testing to white corrosion results are 24 hrs or better. In a lot of cases this coating goes 48 hrs. plus.
Storage conditions are severe including long term exposure to temperature and humidity changes in a shrink wrap environment. When sweating occurs it does not readily dissipate. EDX (Energy dispersive X-ray spectrometer)residue analysis has shown traces of chlorine and sulfur on corroded parts. There is also evidence of moisture.
We have considered and tested alternative plating processes with the intention of improving long term corrosion protection while providing a decorative finish. These include: barrel nickel, barrel copper nickel, rack nickel chrome, barrel nickel w/tin cobalt alloy plating, and barrel electroless nickel. We understand that these are barrier coatings rather than sacrificial coatings. Our question is relative to the salt spray results and any assumptions and/or conclusions that can be made from them. All of these alternatives have failed at 12 hrs. to red rust. Our understanding is these alternative coatings should provide better corrosion protection yet the accelerated testing does not support it. Interpretation of these results is appreciated. Is there any correlation between the two results that can be translated to the field performance expectations? Are we comparing apples to oranges here? dissipate
John SchlosserNew Standard Corporation - York, PA. USA
2000
These other coatings should last more than 12 hours to red rust. The samples must be processed and handled correctly. I do many salt spray tests, and from my experience, there is something very wrong with any sample that fails in 12 hours. That result is equivalent to bare low carbon steel with no plating or coating. Go back to whoever prepared and tested these samples and make sure they are doing it right.
As far as white corrosion goes, you are right in saying that this is a result of the zinc being sacrificed to protect the steel. I work in the auto industry and we sometimes have corrosion specifications that state "X" hours to red rust and "Y" hours to white corrosion. The white corrosion spec is for "showroom appearance" where they do not want the customer looking under the hood at parts that have started corroding (even though the base metal is not yet affected). It is possible to pass white corrosion specifications.
We use rust-inhibitor to protect our parts while they are sitting around for assembly. The rust-inhibitor provides short-term protection since we make tubes that have no inner diameter protection. You ought to take a look at how you are storing your parts and see if you can improve the conditions.
One problem with your part is the barrel plating. It may be absolutely essential for cost purposes to do barrel and not rack, but you need to take into acocunt the loss in corrosion resistance. When you have plated parts rolling around scraping and banging on each other, you need to expect a lower corrosion resistance. Maybe your customer is used to rack-plating results and wants the same quality out of a barrel operation. Maybe you should work with them on lowering the corrosion requirements.

Tim Neveau
Rochester Hills, Michigan
Q, A, or Comment on THIS thread -or- Start a NEW Thread