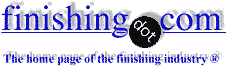
-----
Anodizing Aluminium as a Research Project
Q. I am a graduate student at LSU. I am doing a research project on anodizing Al. I am using a 12 volt battery charger ⇦ on eBay or Amazon [affil links] with a lead cathode. The Al is anodized in sulfuric acid. I used Al as the anode attached to the Al part that is being anodized. I am also using sodium hydroxide to strip the Al from any other anodizing. My problem is that I can't seem to get the part anodized. I was wondering if there is something that I am not doing or the anode needs to be a different metal. Any help would be appreciated. I know there are books on the subject, but as a college student I can't afford them.
Curtis Colson- Baton Rouge, Louisiana
2000
Treatment &
Finishing of
Aluminium and
Its Alloys"
by Wernick, Pinner
& Sheasby
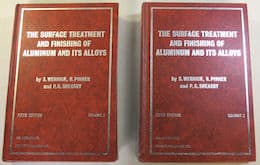
on eBay or Amazon
or AbeBooks
(affil link)
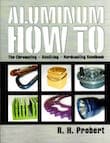
Aluminum How-To
"Chromating - Anodizing - Hardcoating"
by Robert Probert
Also available in Spanish
You'll love this book. Finishing.com has sold almost a thousand copies without a single return request :-)
The Sulfuric Acid Process"
by David LaPlantz
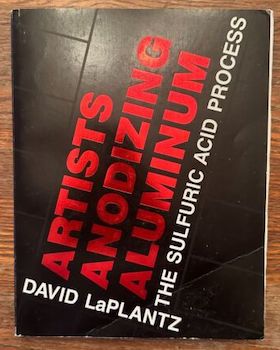
on eBay or Amazon
or AbeBooks
(affil link)
A. Hi Curtis,
People here are happy to help others--that's the whole reason for these pages! When they are slow to help it is usually for what they think is a good reason -- and your trying to proceed without books on the basis of their cost is what some people consider a good reason :-)
If the LSU library doesn't have appropriate books, where are you getting your safety info and training? What have you read or been taught about handling sulfuric acid and caustic soda ⇦liquid caustic soda in bulk on Amazon [affil link] ? What have you read about working alone in a chemical environment--where one drop of caustic in your eye means you'll never read again. I am sure that, between LSU and the city of Baton Rouge, the libraries have a number of good books with chapters on anodizing.
The second problem with you not allowing us to refer you to books is that we then have no common language, no shorthand way for us to talk; instead your question needs excruciatingly long-winded, longhand, where every word we want to use requires paragraphs of definition before we can even start communicating:
The wire or bus bar that you are calling 'the anode' is not the anode--the part that you are trying to anodize is the anode. But, is that wire or bus bar properly stripped? You say it is aluminum--if so it will itself anodize, if anodic, and thus will not conduct electricity to the item you are trying to anodize. Are you sure the polarity is not reversed?
- Do you know that cleaning, etching, and desmutting are required before anodizing, and do you know the details of how to do those steps?
- Do you understand that sealing is required after anodizing and how to do it?
- What alloy are you trying to anodize? Do you know whether the alloy you are treating can be anodized in the first place, and what voltage is needed? 12 volts is not enough for many high-copper alloys.
- What concentration is the sulfuric acid?
- What are you seeing regarding gassing at the anode and cathode?
- How are you judging whether the part is getting anodized?
- How big is it? Is it small enough that the battery charger can deliver enough ampacity -- say 18 ASF? It will never anodize with insufficient ampacity, because the sulfuric acid will dissolve the anodized layer faster than you build it.
Really not trying to give you a hard time, Curtis; but we don't want you hurting yourself nor struggling for weeks to anodize your part when there may be something wrong that is very elemental :-)
Please get back to us with questions about any words or concepts I've introduced that aren't clear to you. Thanks.
Best of luck!
Ted Mooney, P.E.
Striving to live Aloha
finishing.com - Pine Beach, New Jersey
2000
A. I will echo what Ted has said. I thought a library search was the first step of research.
Reasons:
- Lots of people go to warpig.com about home anodizing and wonder why it works poorly when they do it. Simply put, it is not a "dip it" process.
- I think that the largest failure is lack of voltage. 12 volts anodizes extremely slowly and the acid eats it off nearly as fast as it is formed. Find a proper power supply that will deliver 0 to 20 volts, variable, and an amperage of at least 15 amps per sq ft.
- The next is, temperature! It needs to be kept constant, as close to 70 °F as possible. Lower gives a harder and possibly a thicker coating and higher gives a thinner coating that is more receptive to dye, but normally no higher than 75 F.
- Agitation: it needs pumped or air agitation for the best results. Air will mist a LOT. Do you have a hood or exhaust that will stand up to sulfuric acid.
- Aluminum is an excellent cathode. I am very curious how you have your leads arranged and spacing between the part and cathode.
Have your advisor Email me a request, and a promise to return it in one month, and I will loan him a beginners book on anodizing.
James Watts- Navarre, Florida
! I am using a laboratory to do the research -- so as the safety requirements, I have it covered. I know the aluminum alloy can be anodized because it was anodized once before. I also have access to books and used them, I was just wanting some hands on input, not just someone telling me to read another book. If a battery charger won't work, what kind of power supply will? I need something that is affordable. I am getting bubbles (I believe hydrogen) from the cathode but nothing from the anode. I am keeping the temperature at 72 F. The parts that I am anodizing are small (12" X 6"). I tested the part for conductivity to see if it anodized or not. Should I use a titanium bus bar? I am using a degreaser to clean the part and sodium hydroxide to etch the Al. I was also told that a degreaser, Simple Green ⇦ on eBay or Amazon [affil links] , can be used as to desmut. I really appreciate any help, and I ensure that all safety precautions are being used. I also have 3 yr. of chemistry background. Thank You Curtis
Curtis Colson (returns)- Baton Rouge, Louisiana
2000
A. Curtis, No one is trying to insult your abilities or your facilities. We see so many people with bad (no) facilities and no experience with chemicals come here for help, and we don't know your situation until you state it. Thanks.
You say you have read books. I have 4 on strictly anodizing and another 6 with chapters on anodizing and not a single one even suggests anodizing at 12 volts, so with the minimal information you presented, we have to make assumptions.
You have not provided enough information, for at least me, to be able to trouble shoot your problem.
You say that it worked before, so the question is then, what are you doing different now?
With three years of chemistry, you know that hydrogen is evolved from the cathode. You are getting some bubbles, extremely fine ones from your part. They may be hard to see. Why the difference, well there is twice as much hydrogen as there is oxygen to start with. Anodizing is converting the surface of the aluminum to aluminum oxide. The oxygen has to come from some where, so is being largely used up, thus few bubbles.
I have no clue if simply green will work, as I have never done backyard anodizing.
There is no cheap power supply that I am aware of. At LSU, the EE department might have one or know where to borrow one.
Have you analyzed your acid bath?
Out of extreme curiosity, what is your major and the title of your research project or thesis?
James Watts- Navarre, Florida
A. I know this is small in terms of the whole scope of this project, but Simply Green and Castrol Super Clean [affil links] (both tm'ed by their respective companies :-)) If not mistaken are both caustic based solutions, they won't necessarily "degrease" a part, they will readily etch it though. I just remember these two from dealing with guys and their restoration projects.
On the topic of the anodizing in and of itself first off, James has it exactly right, 12 V is not enough, 15 V minimum and more along the lines of 17-20 V would be optimum for a "personal setup". As far as how to get a machine capable of supplying this kind of voltage...hrrrm, a PC Power Supply that runs at 115/230 can supply upwards of 12 V @ 12 AMP, so that's not sufficient, although I've seen a few people wire these together, if you go parallel you essentially only up the voltage potential if I'm thinking right (I'd have to read over this one again as to how people did it). But other than that, there is a good chance you could find a 24 V power source from maybe an old forklift? I'd imagine some of them were 24 V based, maybe a battery charger, like the heavy duty Sears brand ones? They have a switch of some sort on them that sets the voltage and also the length of charge (assuming that sets the amperage to higher levels).
I'm just trying to think of everyday sources for these types of things. I understand nobody wants to spend a few thousand dollars to get an industrial grade rectifier that they may never use again, that's only common sense. Good Luck, if I happen to run across something I'll throw it up here for you.
Matthew Stiltner- Toledo, Ohio
2000
A. Hi All,
I came across this thread while searching for info on home anodizing. There is a bloke in the UK using a 12 v 80 A starter/charger, battery acid ⇦ on eBay or Amazon [affil links] , and either Rit Dye [affil links] or acid black #2 histological stain. He claims good results, after much trial and error, that is. He uses ice water baths to maintain an acid temp. of 3° C, and an agitator for the dye bath to prevent white spots from appearing. For a cathode, he uses a strip of aluminum that is 2" x 1/8" running down one side of the tank, across the bottom, and up the other. For the connection to the workpiece, and to support it in the bath, he uses Al.welding rod.
Sincerely,
Chris Gagnon- Fredericksburg, Virginia
2001
Thanks, Chris! As James Watts alluded to in his posting, two competing reactions occur during anodizing, i.e., the formation of the oxide film and its dissolution by the sulfuric acid. Yes you can slow the dissolution by cooling the acid with ice; in fact, commercial anodizers hold the temperature to about 28 deg. F when doing hardcoating (a very thick type of anodizing). But, as I'm sure you can understand, a film built at a lower voltage by suppressing the dissolution is going to be of a somewhat different nature than a film built at standard conditions. And even still, we don't know that Curtis' alloy, as opposed to the alloy of "the bloke in the UK" can be anodized at 12 volts even at the lower temperature. It may not make sense to spend money on double wall ice-cooled tanks instead of biting the bullet and getting back on the main track with an 18+ V power supply. Old power supplies are abundant and a small used anodizing rectifier may cost less than you think; at this writing I see a 50 A 0-20 V supply for $275.
I know that Curtis may not be able to afford such a unit, but for research in anodizing he should be anodizing at the right temperature and voltage and that will mean he needs more than 12 volts. But thanks for the great ideas!
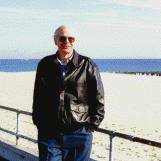
Ted Mooney, P.E.
Striving to live Aloha
finishing.com - Pine Beach, New Jersey
A. Just a word on power supplies - I am successfully using a 3-15 V DC supply that gives 25 A @15 V. I picked this up at my local electronics store for $NZ350 (about US$225).
Keep the parts small and a supply like this will be fine.
- Auckland, New Zealand
2006
Thanks Matt! 15 volts is enough for most alloys, and much better than 12 volts.
Ted Mooney, P.E.
Striving to live Aloha
finishing.com - Pine Beach, New Jersey
Q. Hi, I have a few questions about anodizing. I hope to do an anodizing process for my final lab in my AP Chemistry class. This will be all done in a controlled lab environment under a hood. I have a few questions about the process and materials though. First of all, the power supply; I have a I believe 24 V/6 amp DC power supply. will this work? also could anyone help me with the set up of the acid bath. I was going to use a 1-2 molar solution of sulfuric acid and then fashion an aluminum hook to hold the part and connect it to the positive terminal and then a piece of aluminum to the negative terminal. what is the spacing necessary...this will be a small piece of aluminum? is this a correct setup? are there any diagrams/pictures of a persons or a companies setup that I could see? thanks for any information you all could provide.
Ryan Peterson- Chanhassen, Minnesota
2006
A. Anode to cathode spacing is not critical, Ryan, so long as they don't touch and the part is not very close to the cathode at one end but very far at the other. The usual anodizing solution is 10^15 percent by weight of sulfuric acid. You anodize at approximately 15 to 18 ASF, so 6 amps should handle a surface area of one third of a square foot.
The issue to understand regarding the power supply is that bare aluminum is an excellent conductor, anodized aluminum is a very poor conductor, and partially anodized aluminum is in between. What a commercial anodizer would do is determine the surface area, then calculate the amperage from that. His rectifier would be set up to automatically adjust the voltage as necessary to constantly deliver that amperage. So when he puts the highly conductive bare aluminum part into the tank, the voltage will be very low; as the anodized film starts building, the voltage will gradually increase to maintain that amperage against the increasing resistance. If you can do this manually or automatically with your power supply you should be fine. Good luck!
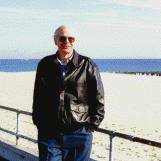
Ted Mooney, P.E.
Striving to live Aloha
finishing.com - Pine Beach, New Jersey
2006
Q. I have a 10 quart aluminum pot that I want to anodize. Can the pot itself be the anode? The square footage will be quite high (350 sq. in.). An advice would be appreciated.
Tim Robertshobbyist - Saint Louis, Missouri,
2007
Q. When enough info collected will try. Here's some thoughts on info so far. Must construct constant current generator type LM317 based. With a couple of decent transistor outputs. Total voltage would be about 12 V current, 2 A output, may take longer but as not commercial is that a real problem? Once crossed paths with bit of info stating a salt based electrolyte. Salt was not table type. Did mention a type known as metal? .Never heard or know of a source. Article did not mention mix. In this net article it states a 12 V car battery charger ⇦ on eBay or Amazon [affil links] . All types I have 'scoped Are about 14 V TO overcome initial battery resistance all have a ripple AC. Needed to knock off the deposits on the lead plates. Certainly not wanted on anodizing. It will almost certainly be confined to commercial aluminum as available here in the UK. . Have located on net couple of books intend to secure from library . When I can get to it. Anyway, any thoughts on subjects I should concentrate on? Many thanks.
graham Hunterelectronic hobbyist - London Enfield UK
July 31, 2008
A. Hi, Graham. The only points I would reiterate is that 12 volts is not enough and the electrolyte is sulfuric acid. I think you may be missing the point that the anodized coating you are trying to build is being constantly dissolved by the acid. It's not merely a matter of going slower if voltage is lower, it's a matter of perhaps not making any net gain at all. Happy trails.
Regards,
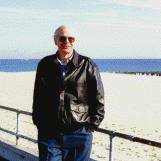
Ted Mooney, P.E.
Striving to live Aloha
finishing.com - Pine Beach, New Jersey
August 1, 2008
Q, A, or Comment on THIS thread -or- Start a NEW Thread