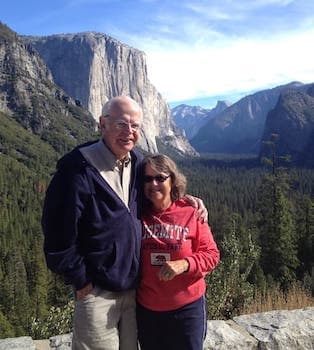
Curated with aloha by
Ted Mooney, P.E. RET
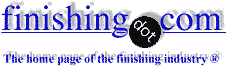
The authoritative public forum
for Metal Finishing 1989-2025
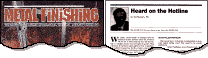

Jump to this related thread:
• Topic #21901 "Salt Spray Condensate Collection and Orientation of Parts"
• Topic #50132 "ASTM B117 Salt Fog Test Chamber Operational Q&As, Problems: Salt Spray Woes"
• Topic #58588 "Salt spray test: Can't get adequate solution flow"
• or continue with -----
Salt Spray Test Inconsistency and Scribe Marks
Q. A batch of galvanized steel coupon samples went through cyclic salt spray corrosion tests. Scribe marks were made on the surface before these samples are put inside the cyclic salt spray unit.
It was observed that red rusts start to appear after 1000 hrs or so on some samples, but oddly, the scribe marks show no red rusts. It is just as if the scribe marks are not there.
I am trying to find out why. The scribing removes the galvanization and exposes the steel underneath. I understand the zinc nearby will provide some protection to the scribed areas due to the self-healing nature of the galvanization. But I was expecting the scribed area to show red rusts first regardless. I am pretty sure the scribing is deep enough. Any suggestions?
- Baltimore, Maryland
June 9, 2021
A. Hi Peter. While awaiting replies you might find Glen Larson's comment interesting.
Luck & Regards,
Ted Mooney, P.E. RET
Striving to live Aloha
finishing.com - Pine Beach, New Jersey
A. 1000 hours is a truly exceptional number of salt spray hours for conventional hot dip galvanizing without a topcoat. Are you sure that you scribed through the various intermetallic layers - eta, zeta, delta, and gamma as set forth by the American Galvanizers Association (galvanizeit.org)? A photomicrograph of the scribe would tell you. In this great website and at the AGA website you will find all the information you could want on the sacrificial nature of zinc and what to expect in both accelerated and real world testing.
Tom Rochester
CTO - Jackson, Michigan, USA
Plating Systems & Technologies, Inc.
Thank you for your insight, Tom. Many samples are tested, some are conventional HDG and some not. Regardless, the first sign of red is not at the scribe marks, which confused me.
- Baltimore, Maryland
⇩ Related postings, oldest first ⇩
Q. When salt spray testing galvanized powder coated parts can anyone identify the critical factors that effect salt spray results. Please have data to back up information.
When scribing parts should the scribe penetrate the galvanized, please advise.
We have seen results where the galvanized coating has been eroded during the salt spray test. Is this normal?
Marc Burger- Louisville, Kentucky USA
2000
A. Marc,
Hopefully you will get more technical replies from others, but you are experiencing the exact reason why cyclical testing or prohesion testing is favored by those who coat over galvanized material.
Simply stated, the galvanization does not have a chance to "repair itself" while under constant exposure in the salt spray. In real life (field exposure), at some time the coating will dry out, allowing this repair process to occur and therefore improving corrosion resistance with galvanized material.
Glen Larson- Redmond, Washington
Marc
The s/s test requires that you scribe thru the paint film to the zinc surface. You do not cut thru to the steel. You will find that the zinc will chemically erode until red rust forms in the scribe. The performance of the paint will depend upon pretreatment. Suitable yellow chromate will give >1000 hours ASTM B117 salt spray. So will correctly applied zinc phosphate. Cleaner-coaters ("iron phosphate") depend heavily upon the final rinse used for performance but are unlikely to exceed 500 hours. Painting HDG steel is not straightforward as the zinc corrodes readily in salt and hence the paint film will be undercut from scribe or damaged areas, hence pretreat is vital for a durable finish. R
Roger Bridger- Croydon, UK
Multiple threads merged: please forgive chronology errors and repetition 🙂
How does the width of the scratch affect the corrosion results in salt spray
Q. How does the width of the scratch affect the corrosion results of painted galvanized steel in the salt spray test ( ASTM B117 ). Does anybody know of a prescribed width ? What is used commonly ?
Best regards,
Piessens Peter- Belgium
2003
A. ASTM D1654 and GM9102P describe methods of scribing. ASTM is presently reviewing D1654 for possible revisions to improve the consistency of the scribe. Studies have shown that the depth of the scribe will make a significant difference.
Cynthia L. Meade- Sylvania, Ohio, USA
Q. Thanks very much Cynthia. Currently we are scribing the galvanised panels with a stanley cutter which gives of course a very thin scribe. Corrosion results are always perfect (painted Galfan, Zn 95%/5%Al). However, when making a wider scribe (e.g. 1 mm) heavy blistering occurs around the scribe. What do you usually do for ASTM B117 ?
Best regards,
Piessens Peter- Belgium
A. Unless otherwise specified by the customer, we use ASTM D1654 which describes the scribe tool as a "straight-shank tungsten carbide tip, lathe cutting tool or carbide-tipped pencil-type".
Cynthia L. Meade- Sylvania, Ohio, USA
A. What an interesting question! I believe the damage dimension must effect the result but this is often not referred to in Standards. I have completed work in my lab which shows the effects on chromate based paints on aluminium and here we have clearly seen an effect. The ISO standards for filiform corrosion (ISO 4623-2 & EN 3665) specify damage of 1 mm width AND that the paint film at the edges should be smooth. Both factors will affect time to corrosion.
What is your conclusion?
- Filton, Bristol, UK
July 3, 2008
Inconsistent Salt spray Results between Two Test Labs
Q. Hello,
I would like to know your opinion about a strange behaviour of some continuous hot dip galvanized samples in salt spray chamber. Some samples were pretreated and powdercoated together and were sent to 2 different laboratories in order to run a salt spray test after scribing of the coating. (I know that salt spray test is not very recommended for zinced substrates, I just want to compare some samples).The results obtained after the same exposure time were very different but not only in terms of mm of delamination from the scribe: the samples tested in lab. 1 show little or no corrosion (anodic area) but a consistent cathodic delamination from the scribe, while the delamination occurred on samples tested in lab. 2 is predominantly anodic. Is it really possible to have such differences only by changing test apparatus?
Thanks!
March 12, 2012
- Berlin
A. Hi Anna,
The salt spray test is notorious for its lack of reproducibility. The only useful result that can come from a salt spray test ia a result that is relative to that of a control. With salt spray testing, there are no absolutes.
There is not enough information in your post to know for sure why the nature of the corrosion was so different in the two test cabinets, but it's probably due to differing conditions.
If you repeat the test, you can add a set of control panels for each cabinet and then examine the difference between your test panels and the control panels.
- Naperville, Illinois
Multiple threads merged: please forgive chronology errors and repetition 🙂
Evaluation of Salt Spray test results: correlation of blisters with the scribe
Q. The query is regarding the evaluation of Salt Spray results.
Salt Spray resistance Test Method being followed: As per ASTM B117
Evaluation Methods being followed:
- Blisters: ASTM D714 - 87 - Standard Test Method for Evaluating Degree of Blistering of Paints
- Scribe & Unscribed specimen evaluation: ASTM D1654 -79 A.
Our acceptance level for the Scribed specimen - Mean failure distance from Scribe: 2 mm & rating of 7.
We need to know the acceptance level in terms of Blistering (Size & Frequency) corresponding to the above scribed specimen acceptance level.
- Gurgaon, Hariyana, India
July 17, 2012
Tip: This forum was established to build camaraderie among enthusiasts through sharing tips, opinions, pics & personality.
The curator & some readers who publicly share their info will be less likely to engage with those who don't.
A. Hi Deva. I don't exactly know the answer, but my question would be: what spec are you painting to? -- because often the spec you are claiming to comply with will tell you what comprises compliance vs. failure.
Luck & Regards,
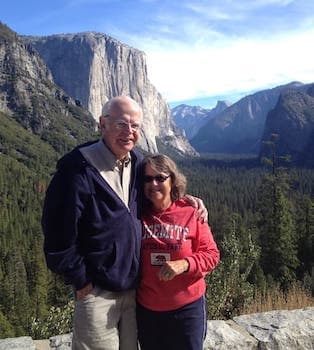
Ted Mooney, P.E. RET
Striving to live Aloha
finishing.com - Pine Beach, New Jersey
Q, A, or Comment on THIS thread -or- Start a NEW Thread