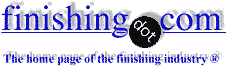
-----
Black oxide fading on small parts
2000
We are doing black oxide on steel parts. After parts are blackened they have to go through a 10% acetic acid ⇦ on eBay or Amazon [affil links] test.In order to be a success the black must not fade before 3 minutes.
The problem is:
When we blacken relatively big parts the test is a success. However, we seem to have a problem with small parts such as screws. The black fades after less than 1 minute.
What might cause the problem? How come only small parts give us a problem? Is there a way to make the black more resistant? ( not fade before 3 minutes)
veronica dewis- Florida, USA
First of two simultaneous responses--
Veronica - There may be several factors contributing to your problem, but the most common are probably cleaning -are the screws cleaned sufficiently to allow a good coating to form? Also, is the operator overloading the basket or barrel and causing the bath temp to drop for too long of a time and decreasing the actual boil time that the parts need for the black oxide to form. A good rule of thumb is to have 1 lb. of parts for each gallon of tank solution. Hope this gets you started in your troubleshooting. Good Luck.
Dan Brewerchemical process supplier - Gurnee, Illinois
2000
Second of two simultaneous responses-- 2000
Several possibilities.
It a very different steel.
It is a very different hardness.
You are probably barrel black oxiding them and it is taking part of the run time to warm up or, they are not having the same amount of contact with the solution possibly because of too much mass in a confined space or the holes are too small or partially peened closed and several other possibilities.
James Watts- Navarre, Florida
Q, A, or Comment on THIS thread -or- Start a NEW Thread