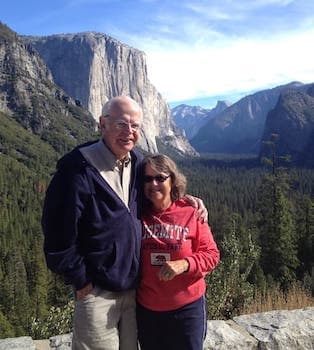
Curated with aloha by
Ted Mooney, P.E. RET
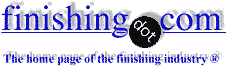
The authoritative public forum
for Metal Finishing 1989-2025
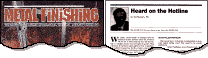
-----
Is our copper plating too hard?
Q. We acid copper plate printing cylinders. Our nominal hardness is 210-230 vickers. Our surface tester is away for repair and a recent reckless act saw our copper go, unchecked, in excess of 300 vickers. Keeping the tanks to usual specification we would not normally have a problem. Sadly, someone is determined to throw a spanner into the works and a short term check is required after polishing. Although the test must be non destructive and test pieces are not possible a file test could be used. would this work? how could we do it? Any other ideas?
Andrew BurtPlating shop employee - Worcester, England
February 25, 2008
A. A file test is not accurate enough. There are non-destructive contact hardness testers. They may be calibrated and cross-checked against a roll of known hardness. Alternatively, you can verify hardness with a conventional indenter gauge before the final polishing steps and let the finishing erase the indenter's mark. If your plating process is stable, there should be a minimal difference in hardness after polishing.
Guillermo MarrufoMonterrey, NL, Mexico
February 28, 2008
A. Hey there,
well, as you know, it is very important to maintain the hardness, and also ductility to reach good results in electromechanical engraving. Therefore I recommend to produce a ballard skin with thickness of 100 micron. Make some bending tests and a good ductility is given if you can bend the shell at least 2-3 times in each direction (radial and/or axial).
Regards,
- Mexico City, Mexico
March 1, 2008
Q. Hi Dominik,
Thanks for your reply. It is interesting you say the ballard skin should be at least 100 microns. We plate different thickness skins to get our desired progression but sometimes only 70 micron (about 100 is average). Would a thin skin be detrimental to the cell? Would different thickness skins produce a noticeable change in the engraved cell and resulting colour tone on the printed paper? Therefore would print quality be noticeably different if we plated a set skin thickness?
Thanks for your time
- Worcester, England
March 3, 2008
March 6, 2008
Hey Andrew,
it makes no sense having a ballard skin greater than 100 micron. As the higher the thickness the more difficult it is to strip off the ballard skin. Usually you choose the thickness of ballard skin with the deepest cell which you want to engrave. Minimum 50 micron you need to stripe of the ballard skin in a good way. So between 80-100 micron ballard skin is the most common use.
I recommend to you, using the ballard skin to see what's the real quality or physical condition of your deposited copper layer. If you have color tone in the printing process than you should check the following:
- Which substrate is going to be used (paper, foil etc)
- Before engraving, how is my roughness of the copper deposit?
- During engraving, diamonds in a good shape? Using cutting oil? The shoe is in good condition? Not creating damage in copper surface during engraving?
- After engraving and after chroming, how is my roughness of the chrome and the structure of the polished chrome surface? (recommended roughness for paper 0.3 - 0.4 Rz; for foil printing 0.2 - 0.3 Rz) with a nice cross structure (approx. 45° angle crossing structure)
- The printing press is correctly set up (doctor blade pressure, doctor blade angle, viscosity of the inks, printing speed, temperature etc)
- Does cylinder have "stepping" (for example, 5 color printing = 5 different cylinder, therefore each cylinder has to have a little bigger diameter to maintain the right tension of the to be printed substrate in the printing press)
The thickness of the ballard skin doesn't cause effects like you have described.
I hope I could give you some helpful info's.
Regards,
- Mexico City, Mexico
April 30, 2019
Q. Hi everyone
Our acid copper layer is too hard in the HCD areas, between 180 and 200 HV. How can I decrease the hardness to 100HV?
Bath parameters:
Cu: 60 g/l
H2SO4: 60 g/l
Chloride: 80 mg/l
Temperature: 20 °C
Thanks in advance
- Munich, Germany
? Hello Victor, has the bath had a recent analysis done on metallic impurities? What is the current density?
Mark BakerElectronics plating - Winston-Salem North Carolina USA
May 4, 2019
Q, A, or Comment on THIS thread -or- Start a NEW Thread