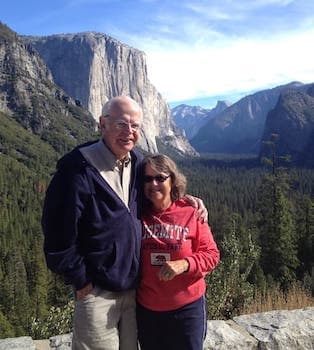
Curated with aloha by
Ted Mooney, P.E. RET
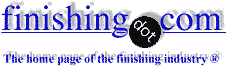
The authoritative public forum
for Metal Finishing 1989-2025
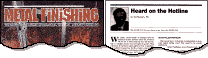
-----
What is the best type of finishing for highly reflective finish? (Nickel Chrome? Vacuum Metallizing? etc)
February 25, 2008
Dear Finishing Experts and Enthusiasts!
Hi Everyone! I have been constantly learning on the various types of finishing available and would like to gather opinions and advice on which finishing to go with for a part which we are to manufacture.
The part that we are to manufacture (using CNC Lathe) is made out of aluminium and it requires a finishing that has a highly reflective and mirror finishing, something like the finish you see on water faucets and motorcycle exhausts. (You should be able to see your own reflection when you are looking at the part). We have recently sent the parts out for nickel chrome plating as well as vacuum metallizing. The results for both finishing are listed as below:
Vacuum Metallizing:
For the Vacuum metallizing process, the finishing produced is more reflective as compared to the Nickel Chrome in the sense that you are able to see your own reflection, but at the edges of your silhouette, I can see that it is not smooth because the turning marks are blurring the edges. (Point to note: the surface of the part before sending it for finishing process is smooth, just that there are turning marks on it, which cannot be eliminated) However, you can still see your own reflection, just that the edges are not smooth as I had wanted it to be. Besides that, the finishing produced has a yellowish tint on it, not like the silvery tint I had imagined it would have. Furthermore, when you run your fingers over the part, the surface is "sticky", thus does not provide you with a smooth touch.
Nickel Chrome:
For the Nickel Chrome plating (Only 1 layer of Nickel and 1 layer of chrome is used), the part has a very nice silvery finishing but it is not reflective in the sense that you cannot see your own reflection when you hold the part in front of you. (It still looks shiny though!) Besides that, the turning marks are also very prominent and visible even after nickel chrome plating. I suppose this is because the thickness of the nickel chrome plating is much less as compared to the vacuum metallizing process. Nickel Chrome produced a very smooth surface that is very pleasing on the hands unlike the "sticky" surface produced by Vacuum Metallizing.
Now after sharing with all of you the pros and cons of each finishing, my question is, is there a type of finishing which can produce a highly reflective mirror finishing while still being able to cover up the turning marks and also produce a smooth surface that is nice to touch?
I have read some of the posts here on Finishing.com on nickel chrome plating and learned that by putting a layer of copper after the zincate layer and buffing it followed by more nickel layers and finally a layer chrome will be able to produce shiny and reflective surfaces.
1. But will it produce the surface as described above?
2. These parts are to be mass produced, so if buffing after the copper layer is required, then I assume that it would be quite time consuming. Is there a faster way to do perform the buffing operation?
3. Will the surface be as reflective as the ones produced by vacuum metallizing process?
4. If nickel chrome plating can achieve a finishing that is equivalent or better than what can be produced by vacuum metallizing, then what should be the process to follow?
5. If there are any other finishing process that can achieve the required finish, what will it be?
Any advice and feedback on this matter will be more than welcomed! Thanks to those who are willing provide a feedback in advance!
Best Regards,
TK
Buyer - Malaysia
It would be unusual if initial appearance were the only important factor in the selection of the finish, TK, but yes, nickel-chrome plating can be totally reflective. I am assuming that your nickel plating bath is operating correctly and giving you good brightness, but I don't have a way of really knowing that.
But recognize that, regardless of what coating technology you pick, you cannot get a smooth reflective surface by putting a thin coating over a rough surface. That's like being being asked to make a smooth new road out of a pothole ridden old road by laying no more than a half inch of asphalt over it. The asphalt can't correct a hole of even a half inch deep, and nickel-chrome or metallizing can't give a mirror finish to a surface with roughness.
Maybe it would be possible to burnish either the copper plating or the steel part itself in a mass finishing barrel or vibratory unit.
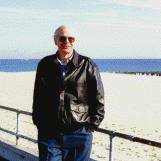
Ted Mooney, P.E.
Striving to live Aloha
finishing.com - Pine Beach, New Jersey
February 25, 2008
First of two simultaneous responses --
You can significantly reduce the tooling marks with diamond turning or similar with the proper feed and speed of the final pass or two on the lathe. This will help and not add a great amount of time to the turning operation.
You have not said what it's use will be. The reflectors on cars are bright dipped aluminum and clear anodized. You might want to talk to someone that does that process to get their views on your part.
Buffing does add a lot of time and manpower to your part.
You might also want to talk to your platers about your views of their product. A tiny bit of the problem may lie in the zincate step.
They can bright dip ( a nasty process) before plate which will make either look better.
- Navarre, Florida
February 26, 2008
Second of two simultaneous responses --
To add to Ted's comments, I would like to emphasize that you can achieve a total mirror finish using mass finishing equipment alone; however, because of oxidation you should plate the parts.
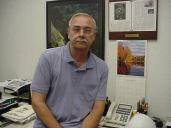
AF Kenton
retired business owner - Hatboro, Pennsylvania
February 27, 2008
Q, A, or Comment on THIS thread -or- Start a NEW Thread