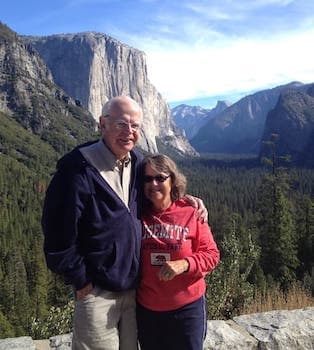
Curated with aloha by
Ted Mooney, P.E. RET
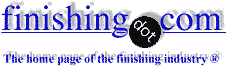
The authoritative public forum
for Metal Finishing 1989-2025
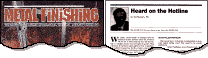
-----
Should 420 grade passivated stainless rust in a 24 hour salt spray test?
We have some passivated 420 stainless steel shafts that exhibit a thin rust stain on them after 24 hours of humidity salt test at 40C. Is this normal?
Ron BuchananCooperate Q.C. Engineering - Blackwood, N.J., USA
February 22, 2008
Ron, I wouldn't count on any 400 series martensitic stainless steel- 410, 416, 420, 431, 440A, B, or C- passing a salt spray test. They might pass, sometimes, depending on how well you passivated them and how well they're heat treated, but it's not something I'd count on. You'll notice ASTM A967, paragraph X1.11 notes the salt spray test "may not be applicable to all martensitic or ferritic stainless steels".
We use a humidity test, 105F, 100% relative humidity, 24 hours, as a test for our 440C parts.

Lee Gearhart
metallurgist - E. Aurora, New York
March 5, 2008
Thank you.
Ron Buchanan- Blackwood, New Jersey
April 14, 2008
We had better luck with citric passivation on 400 series steel than when we used nitric and dichromate. 410 still passed most of the time.
James Watts- Navarre, Florida
April 15, 2008
April 21, 2008
I used Citric on the shafts that were mentioned. It held up great compared to the examples that were posted. I believe that we are going to go with 316 stainless.
Thanks!
Ron
- Blackwood, New Jersey
Dear Ron,
I suggest you to go ahead with citric acid
⇦ this on
eBay
or
Amazon [affil links] or 20% HNO3 acid cleaning of the workpiece before you heat treat, because martensitic steels as such are not recommended for salt spray test, but if you at all require it, you can go ahead with precleaning before heat treatment, also see to it that you keep the hardening temperature above 1050 degrees C with a sufficient cycle time, normally dichromate and nitric acid passivation suits better with these steels, if surface lustre is not a matter of concern for you then try this too, after complete heat treatment including tempering passivate the part with dichromate and nitric acid solution and do the second time tempering at not more than 180 degreeC temperature, you will witness amazing results. This is my experience.
- India
May 14, 2008
Q, A, or Comment on THIS thread -or- Start a NEW Thread