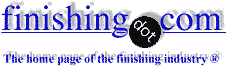
-----
Speed of crane for hot dip galvanizing
I need to know what should be the optimal speed of the crane (hoist,trolley,bridge), I need to know both the slow and high speed for galvanizing of piece goods (batch galvanizing)
Ameen Syed Roohulgalvanizer - Saudi Arabia
February 20, 2008
February 25, 2008
If your crane supplier is reputable they will know this. If you are buying a crane from one who has not sold cranes into this industry successfully then you could be buying a real problem.
The galvanizing industry is as hard on an overhead crane as any. The corrosive atmosphere, combined with arduous duty means excessive wear.
In saying all that, there are three speeds to consider, depending on your shop configuration. Long travel, cross travel and hoisting/lowering.
Of these only hoisting/lowering is really relevant to the industry specifically. (the others are important though, but for quite normal practical reasons. Recommended you have two speeds on all motions)
Hoisting/Lowering. The fast speed isn't so critical, you won't normally use it for immersion / withdrawal from zinc (or pretreatment).
Slow speed best (in my experience) at between 0.9 and 1.1 meters per minute.
Too fast and you miss out on the surface tension effect pulling surplus zinc off the work, so regulating the thickness (to some extent), and you'll get thicker coatings than you want.(perhaps surprisingly)
Too slow and you'll get longer immersion time than required, and so you'll also get too thick a coating. All costs zinc that extra coating thickness, and you get no extra for it.
At this slow speed though, your crane should be able to operate indefinitely. Some hoists have a variable speed motor to provide the
2 speeds, and the cooling fan on the motor is on the motor driveshaft. So, long periods of slow hoisting can mean next to no cooling, and leads to burnt out motors.
Make sure that your hoist motor is going to get cooled properly. Get M7 rating, no less.
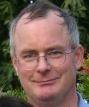
Geoff Crowley
Crithwood Ltd.
Westfield, Scotland, UK
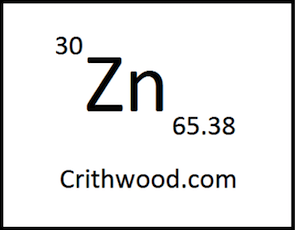
February 28, 2008
Dear Mr.Geoff.
many thanks for your answer
Regards,
- Saudi Arabia
February 28, 2008
Sir:
In the "Old Days" the up-down speeds of the cranes were 5 feet/minute and 15 feet/minute. Going into the zinc was 15 feet/minute and coming out was 5 feet/minute. A good portion of North American galvanizers now use variable speed cranes, either by controlling the AC frequency or by using "switched reluctance" (SR), the latter said to use less electricity. Thus at the kettle, typical speeds are now 0 to 10 feet/minute.
A few years ago at a pipes plant in Bogata, Columbia, I had a very interesting thing happen. They use heated double salt flux (ACN=0.8) at about 30 degrees baumé.' I wanted them to try heated quadraflux
(ACN=1.57) at 14 degrees baumé.' I took several 8 inch long sections of 1.5 inch diameter pipe (about 2mm wall thickness) and drilled a hole near the top end for a wire. By hand I took the quadrafluxed pipe over to the zinc kettle and lowered it into the zinc and left it in 1 minute and then withdrew it. The pipe went into the zinc without zinc spatter and galvanized perfectly. When I tried to put the same size pipe into the zinc with the high baumé double salt, the zinc spatter was terrific AND the pipe would NOT sink into the zinc. I had to get a rod to push it down into the zinc and had to get much protective clothing to avoid being burned. The zinc coating was thick and ugly and had a bad drip on the lower end.
Several years ago I went to a company in Montreal and saw them galvanizing 1.5 inch angle 8 feet long, held vertically with wires. The kettle was 10 feet deep. The spacing of the angles was about 2 to
3 inches. They used heated, low baumé quadraflux. Entry into the kettle was within 5 seconds. Then from the center, two workers skimmed quickly to the ends. Total time in the kettle was about 1 minute. Then the angles were withdrawn within 5 seconds except for the last 2 inches which were withdrawn slowly (to avoid drips). At the time I thought this was crazy. For my education they did one lift the "old way" by fast entry and slow withdrawal. The angles that were done by fast-in and fast-out were about 2 mils evenly coated (1 mil =
25.4 microns) whereas the fast-in and slow-out had 2 mils at the top ends and 10 mils at the bottom end.
Be aware that high baumé double salt gives much kettle spatter and causes "floaters," whereas low baumé quadraflux gives virtually no kettle spatter and the steel sinks easily into the zinc. This is the primary difference between European and North American Galvanizing. Be also aware the double salt is relatively temperature stable whereas quadraflux is not. Thus if the kettle furnace has insufficent heat capability double salt and strong preheating could be a better choice.
Regards,
Galvanizing Consultant - Hot Springs, South Dakota, USA
March 1, 2008
Dear Dr.Thomas,
Many thanks for your reply.
kind regards,
- Saudi Arabia

Q, A, or Comment on THIS thread -or- Start a NEW Thread