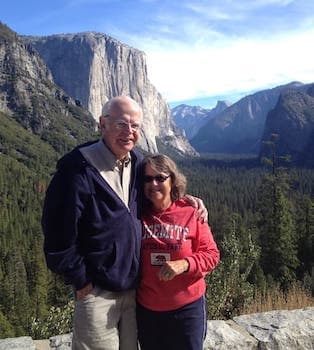
Curated with aloha by
Ted Mooney, P.E. RET
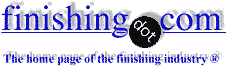
The authoritative public forum
for Metal Finishing 1989-2025
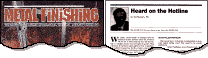
-----
Regarding thickness of raw iron material and coating thickness of zinc
for Engineers, Shops, Specifiers
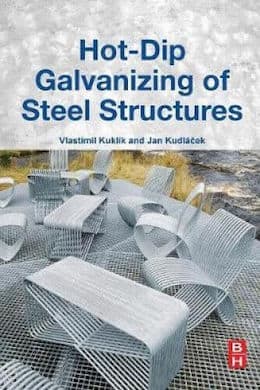
avail from eBay, AbeBooks, or Amazon
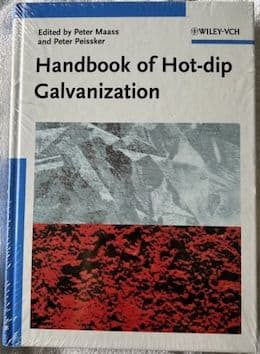
avail from eBay, AbeBooks, or Amazon
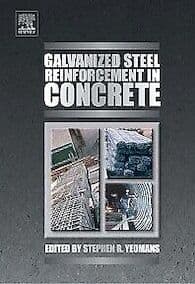
avail from eBay, AbeBooks, or Amazon
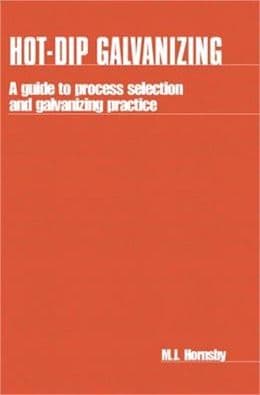
avail from eBay, AbeBooks, or Amazon
avail from Amazon
"User's Guide to Hot Dip Galvanizing for Corrosion Protection in Atmospheric Service" by NACE (1997 only rarely avail.)
avail from AbeBooks, or Amazon
(as an Amazon Associate & eBay Partner, we earn from qualifying purchases)
Q. Sir,
Can you explain the relation between Thickness of raw material use for galvanization and thickness coated on it of Zinc?
Plating shop employee - Gaziabad, U.P., India
February 20, 2008
A. In general the thicker the steel, the thicker the zinc coating from hot dip galvanizing.
This is not absolute, as there are other influences on thickness, including Steel chemistry (particularly Si and P), surface profile of the steel (shotblasting to SA2.5 will almost double the thickness), zinc temperature (not exactly linear, from at say 440 increasing temp decreases thickness, until about 470 when it starts to increase it).
Main reason for thicker steel getting a thicker coating is immersion time. Its an alloying reaction, not just a dip based coating. Thicker steels take longer to heat up in the zinc, so longer immersion time.
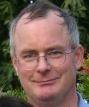
Geoff Crowley
Crithwood Ltd.
Westfield, Scotland, UK
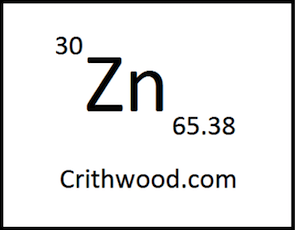
A. Geoff:
Your comments on zinc thickness versus temperature of the zinc are indeed interesting. Is your thermocouple in the zinc or attached to the outside of the kettle wall?
At your quoted temperature of 440C (824F) it is my experience that once the zinc coated steel reaches the air it freezes rapidly rather than draining, thus giving thick and sometimes lumpy coatings. Just above this temperature (e.g. 830F for most climates) gives the thinnest of all zinc coatings. Temperatures above about 830F or 840F invariably gives thicker and thicker zinc coatings as the temperature rises. At your quoted 470C (878F), extremely thick zinc coatings are produced and even kettle life is shortened. Having a deep kettle (relative to width) with sufficient heat capacity to maintain a relatively constant temperature is extremely important to get the required results of consistently thin zinc coatings. Spin and other kettles are often operated at higher temperatures for different reasons.
Regards,
Galvanizing Consultant - Hot Springs, South Dakota, USA
A. Tom,
three thermocouples, 2 in zinc 1 on kettle wall.
I wouldn't recommend anyone running kettle at 470, as you say, increased kettle wear.
We run one at 440 or 445, the other at 450 C
Done a lot of experimentation with temp vs coating thickness and that summarises results.
Agree with you about maintaining steady temp, very important wherever its set. Cycling is not good.
High temp kettles (e.g., spinning) most often ceramic as steel won't last long at 470C let alone 550C.
I've seen galvanizing as low as 435. Minimum thickness achieved at about 445-450C
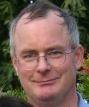
Geoff Crowley
Crithwood Ltd.
Westfield, Scotland, UK
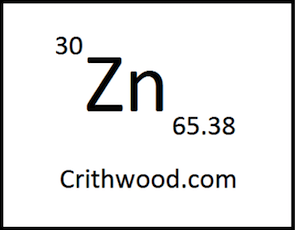
A. Geoff,
I have a hot dip galvanizing client doing 54,000 tons/year with a
"weighted average" thickness of 0.130 inches (3.3 mm thick; e.g. with a very large surface area) achieving a
%GZU = 5.4% (no credits for ash or dross). They have an enclosure around the kettle with the steel entering one end and exiting the other end of the enclosure. The suction fan is "on" all the time. Kettle temperature is maintained -2F to +1F with a zinc temperature of 828F (442 C). Temperature inside the enclosure at the top is 120 °F (47 °C). They are now considering having the suction fan "off" except during steel entry into the zinc with hopes of getting a higher temperature inside the enclosure and allowing even better zinc drainage as the steel is withdrawn from the zinc. Having the suction fan "off" except during steel entry will also predictably reduce electrical costs.
A few years ago when I was doing cost estimating for a Belgium galvanizer, I came to the conclusion that a kettle with an enclosure consumes about 20% less energy for the same amount of product.
Regards,
Galvanizing Consultant - Hot Springs, South Dakota, USA
A. The problem of fume capture and resultant heat loss is interesting. But not just for the kettle, but also for the fume filtration system.
Galv fume is hygroscopic, and its being filtered by a media that has a pore size larger than the particle size being filtered. So partial media blinding is required to get effective filtration, but no cold air containing moisture will be of any use.
So extraction from the canopy other than when fume is being generated (immersion) is bad for two reasons, filter efficiency and heat loss.
As turning the filtration on and off is a little difficult, what we do is have the fan run down to low revs (inverter control) and up to extraction speed when required. If human controlled, it would not happen, so it's controlled by logic of the dipping process. (Cross shop cranes, cross shop kettle, and canopy fixed to crane). When the crane movement indicates the start of a dip (logic of crane movements)then the fan winds up to full, then auto returns to idle after 4 mins (variable and able to be over-ridden by operator).
This avoids the high inrush current of the fan motor starting from stopped, as its already idling. Significant electricity savings, along with some saving of heat inside the canopy, and minimum cold air to the filter.
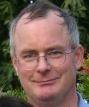
Geoff Crowley
Crithwood Ltd.
Westfield, Scotland, UK
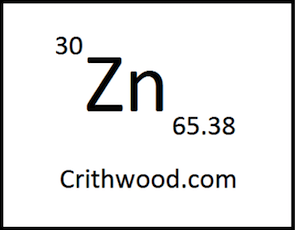
Geoff,
Is your enclosure "soft sided," does it move with the crane, and only
"form-up" all four sides at the kettle? Or in the alternative is it steel and remains around the kettle all during production? I agree fully in slow fan speed except when the steel is going into the zinc
(then full speed). I realize that stopping the fan motor fully is not a good idea.
Geoff, You are also invited to come to our ranch and catch rainbows
(four pounds in June) or tilapia in September (size is unknown just now).
Ted, You are also invited to come to our ranch to fish. finishing.com is providing a vital service to the finishing industries.
Regards,
Galvanizing Consultant - Hot Springs, South Dakota, USA
Thanks for the kind words and the invitation, Dr. Cook. I don't know when I can get to So. Dakota but it will certainly be in summer rather than in the winter :-)
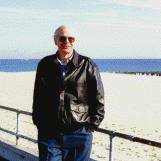
Ted Mooney, P.E.
Striving to live Aloha
finishing.com - Pine Beach, New Jersey
First of two simultaneous responses -- March 12, 2008
I've seen canopies for fume capture of many types, but ours are both similar, in steel. They are fixed to the double girder overhead traveling cranes, have doors on three sides.
Two doors on the long sides are half the height of the side, and are raised by twin chain hoists each door, hoists of 2 speeds with upper and lower limits for accurate positioning. All controlled from the operator pendant, which is on a track allowing the operator to have the pendant at any position along the kettle sides.
On the third side, (one end) there are twin doors full height hinged and manually (but rarely) opened to assist in double dips. These two doors have armor glass in them to allow viewing by the operator of the immersion.
Side doors have rubber seals (old conveyor belt is good) of about
100mm that seal against the furnace top plates. The ends have these seals to prevent splash exiting.
The long doors are best with as few seams, welds, brackets on the inside as possible. Every scratch, weld etc is a point for zinc to stick to, like metal spraying! Doors require regular cleaning to reclaim the zinc, and prevent excess weight inside the door.
Crane hoists are outside the canopies, above them, with only ropes entering through a long slot on top, also with rubber seals.
Top of each side of the canopy is a plenum chamber leading to the exit point in common on one end. These chambers have balanced orifices to equalise extraction along the length.
The exit point is a stubby ducting which matches up with another fixed on the wall of the building leading to the filter. Proximity switches tell the fan logic when to be at low or high speed. (One has three speeds, a manually invoked "turbo" speed for extra surface area material). Other proximity switches feed another set of logic that controls large displays showing dipping rate.
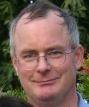
Geoff Crowley
Crithwood Ltd.
Westfield, Scotland, UK
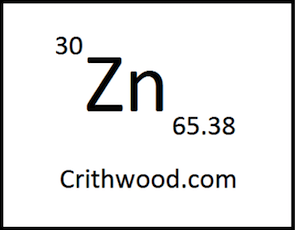
Second of two simultaneous responses -- March 12, 2008
hope the following should clarify your query
1)the surface finish of the material to be galvanized rougher the surface more coating it takes.
2)chemistry of the steel reactive material with higher silicon, phosphorus, and even carbon beyond allowable limits will produce higher coatings.
3)kettle temperature, I have been working for quite some time at 442 °C, I am pretty much comfortable with this temperature.
4)dipping time
5)withdrawal speed
best regards,
- Sharjah, U.A.E.
March 14, 2008
Dear Ameen,
Thank you for your comment about using 442 °C (828 °F) for the zinc galvanizing temperature. I presume you have an excellent kettle furnace with adequate heat capacity and that you have an enclosure around the kettle? I expect you may have a well designed and engineered plant.
Regards,
Galvanizing Consultant - Hot Springs, South Dakota, USA
March 14, 2008
Geoff,
Thank you for your detailed description of your kettle enclosure. It reminds me of one I saw in Hagen, Germany. I appreciate that you are trying to avoid another "tin" man and that you have installed equipment to keep the kettle smoke out of the workers's lungs. I regret not having published the baghouse data years ago so that owners perhaps would have installed more kettle enclosures and baghouses.
Regards,
Galvanizing Consultant - Hot Springs, South Dakota, USA

Q, A, or Comment on THIS thread -or- Start a NEW Thread