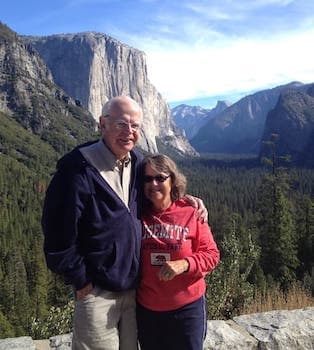
Curated with aloha by
Ted Mooney, P.E. RET
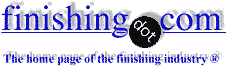
The authoritative public forum
for Metal Finishing 1989-2025
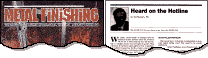
-----
Tin Cobalt plating problems Q&A
by Abner Brenner
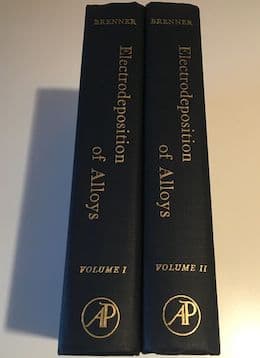
on AbeBooks
or eBay or
Amazon
(affil links)
Q. Hi sir this is from Saravanakumar M
I am working on the Tin Cobalt alkaline based plating. We have to face a lot of time coverage problem in LCD area. I use potassium tetra pyrophosphate for conductivity. I have perfect bath parameters, then I don't know how to control this kind of problem.
- Chidambaram, TN, India
November 11, 2022
⇩ Related postings, oldest first ⇩
Q. Anyone can tell the bath formula for a Bright Cobalt plating? It is used to substitute the Bright Nickel plating. Any books talking about the cobalt plating can be suggested?
Deville Yiu- Hong Kong, China
2000
A. Dear Mr Yiu,
I think you are referring to tin-cobalt plating done over Nickel plating to give a near chrome like look. It is not a replacement for Nickel. You should contact your nearest Enthone dealer for the chemistry. Regards
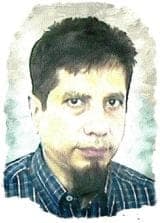
Khozem Vahaanwala
Saify Ind

Bengaluru, Karnataka, India
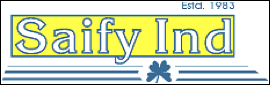
A. Nickel and cobalt are very nearly the same. Cobalt is slightly harder, slightly more magnetic, quite a bit whiter, same atomic weight and valence and etc. Any bath that you can find for bright nickel, you can substitute the same amount of a cobalt salt for as in cobalt sulphate for nickel sulphate.
Cobalt is quite a bit more expensive at the current time. Cobalt can be used in jewelry, avoiding the frequent prohibition of "no nickel". It is also unregulated, the last I knew, by EPA.
- Navarre, Florida
Multiple threads merged: please forgive chronology errors and repetition 🙂
Q. It was found that it's very difficult to deposit a Sn-Co alloy coating with a thickness of more than 5 microns (without agitation). The problem is that the deposit will become dendritic with prolonged plating duration. If you have any idea about overcoming this problem, Your help and suggestions will be highly appreciated.
Keming Chen- Loughborough, Leicestershire, UK
2002
A. Well, I could not find cobalt-tin but I did find nickel-tin and they will be close. Since it is a stannous bath, you certainly do not want to use air. My guess is that you are forming some stannic tin which is precipitating out giving you shelf roughness. My first try would be to increase filtration which will also give you more fluid agitation.
James Watts- Navarre, Florida
A. Over this side of the world, SnCo alloy plating has been used as a replacement for Hex Chrome. It looks similar to chrome but not exactly like chrome. The deposit is very thin (about 0.3 micron). I may be missing something but why do you need such a thick deposit? Air agitation is a definite no-no as suggested by Mr.Watts.
SK CheahNew Crown Hong Kong Co.Ltd. - Malaysia
A. Tin-cobalt alloy plating is quite unusual. I know the International Tin Research Institute in Uxbridge (UK) did some work some years ago with tin-nickel, but they used an alkaline bath and could only get very thin decorative deposits. If the tried to get thick ones, the deposit became very brittle and flakey.
However, none of this should deter you from trying to develop a tin-cobalt system. I would suggest you look at high tin and low cobalt compositions as one of the major problems with cobalt deposits is the co-deposition of the two phases. This leads to very high stress and poor adherence. It may be possible to use the ITRI basic system but replace the nickel salts with cobalt. There are numerous cobalt baths, based on the well known nickel formulations, that claim to deposit cobalt, but my experience is not as positive as those claimed! The baths tend to be inefficient and do not respond to additives as one would expect. Furthermore, there is the big problem with stress.
As far as dendritic growth is concerned, I would suggest you look at different levelers and brighteners. You may also find benefit from using low current densities and possibly temperatures about 40 °C. However, all this depends on your bath formulation, which you do not give.
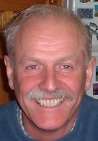
Trevor Crichton
R&D practical scientist
Chesham, Bucks, UK
----
Ed. note: Mr. Chen and readers may wish to give a listen to "The Lost Art of Tin-Nickel Plating".
Pulse plating of tin-cobalt
Se puede hacer electrodepositos de aleación estaño-cobalto mediante corrientes pulsadas, cual sería el proceso? ademas si yo deseo recubrir hierro dulce cual sería el sustrato a emplear indicado y obtener un deposito de buena calidad.
Mi situación es la siguiente desconosco el proceso de recubrir con aleación de SnCo, por lo tanto tengo interes en conocer las condiciones ideles para llevar a cabo dicho proceso. especialmente las del equipo (o rectificador) si es mejor un switches o un SCR ademas que tan restable es comprar las soluciones ya preparadas o fabricarlas insitu. muchas gracias y si fuere así en que condiciones?
-- muchas gracias. Atte: Mauricio
investigador - Medelin, Antioquia, Colombia
2004
Tin/Cobalt bath that is rapidly converting Stannous to Stannate
Q. We have a Tin/Cobalt Plating bath that is converting Stannous to Stannate at a rapid rate. I read in an earlier posting of a "Plating Reactor" to help convert back to Stannous. Does anyone know about this or who to contact about this problem?
Beth KlinglerNational Metalwares, L.P. - Aurora, Illinois, USA
2006
A. What bath are you using? Stannous is normally reserved for the Sn(II) cation whilst stannate is Sn (IV) as an anion - tin being amphoteric and all that.
However, the most common reason for tin being oxidised is because air is getting into the system -- so don't use air agitation.
A better answer can be given if we have your operating details.
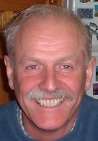
Trevor Crichton
R&D practical scientist
Chesham, Bucks, UK
A. Are you sure you don't mean that the tin is being oxidized to the stannic state? If this is what you are referring to then the most common answer is that some of this type of reaction is normal. If it is excessive it is generally due to air agitation or introducing air due to leaking seals in filter systems or finally too high an rpm for a barrel. If you are using a proprietary system (I presume) your vendor should advise you as to whether they have an additive which is compatible to the process you are utilizing which will reduce oxidation and/or a treatment additive to precipitate out the stannic tin.
Gene Packmanprocess supplier - Great Neck, New York
Tin-cobalt plating going black
Q. Hi. I put in a tin - cobalt bath.
It was plating ok
I then raised the Tin content by 30% to whiten the bath.
Now it is plating black.
What plates first: Cobalt (what colour is Cobalt?) or Tin?
How can I get the Tin to plate more of the Alloy?
- South Africa
February 18, 2008
![]() |
A. Warren, - Penang, Malaysia A. Dear Warren, Plating Engineer - Danbury, Connecticut, USA A. Hi There, ![]() Praveen Kumar plating process supplier Mumbai, India |
Q. Hi
I use SN-CO alloy bath but colour is not black, (grey) I want more black colour what do I do?
I use sulphate bath.
- Istanbul, TURKIYE
October 17, 2008
Q, A, or Comment on THIS thread -or- Start a NEW Thread