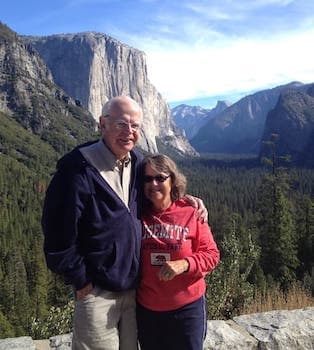
Curated with aloha by
Ted Mooney, P.E. RET
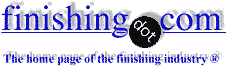
The authoritative public forum
for Metal Finishing 1989-2025
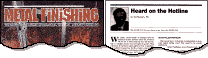
-----
Fluxing and the other galvanizing problems
Q. Dear Sir/Madam
The color of fluxing also changed due to carrying of Fe+2 although we have two rinsing baths.In our laboratory, we tried to add NH4 into the fluxing bath specimen.Our baumé is now 29 Be and our total salinity is 465 g/l at RT.(We utilize Ni-contained fluxing agent)We are heating the flux up to 50 °C and also stirring to prevent the precipitation of salt by the means of compressed air. Neither picklings proceed nor fluxing work
The other problem is degreasing, because there is still oil remaining especially around the welding area(I think our customers use the welding spray that is not water based for preventing of the welding strips.
and our chemical supplier always say that "only according to pH you can keep the quantity of the degreasing. I do not agree with them, instead of this phenomena, we have to find the free acid.
In brief,Do you have any suggestion on the subject of the working range of acidic degreasing, fluxing,pickling, rinsing?
Thanks a lot....
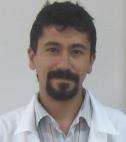
Hakan Esen, Material Engineer(BSc.)
galvanizing plant manager - Bursa, Turkey
February 13, 2008
A. Dear Hakan,
Your letter has affected me very much. Your owners have spent a few million dollars to construct a galvanizing plant and now it is time for them to spend a few thousand dollars to train your people how to operate it. You need an honest, scientific, on-site consultant that sells knowledge, not products. Only with good scientific knowledge can your galvanizing plant make money, without it you will have a large daily loss. To delay obtaining the needed operational procedures is a terrible money loss.
finishing.com is an excellent BEGINNING. If you "click" on the SEARCH ENGINE, then SEARCH FORUMS & ARTICLES at finishing.com under "hot dip galvanizing flux" you will get 70 "hits." Under DEGREASING you will get 457 "hits." I did not try "acid Pickling," but I expect many "hits." Once you read all these letters and responses, some of which are scientific and true while others are not so good.
Regarding your specific questions: Fe+2 in solution is green. Fe+3 is an orange precipitate. NH4 does not exist by itself. Perhaps you mean NH4Cl (ammonium chloride; a white solid) or NH4OH (ammonium hydroxide; a clear liquid). A baumé of 29 (measured at room temperature) is very high and not even on my latest table that I just constructed. The highest I have is 25 deg baumé and for double salt this is about 425 grams/liter; for triple salt it is about 475 grams/liter; and for quadraflux is about 520 grams/liter. (I am just now working up the data, which will be accurate +-1 or 2 grams. This table goes from 8 deg. baumé to 25 deg. baumé which covers ALL the needed concentrations. I also did zinc chloride.) "Total salinity" is not a proper term. Likely what is meant is total dissolved flux. I am not a proponent of nickel containing flux for health reasons. I like caustic cleaning and most galvanizers use between 8% and 12% (sodium hydroxide) ⇦liquid caustic soda in bulk on
Amazon [affil link]
. For pickling 10% sulfuric or 17% HCl is common. Galvanizing can tolerate some oil and grease and it burns at the kettle as yellow fires as the work goes into the zinc. I have purified and corrected flux solutions so that the black (bare) spots on welded areas galvanize perfectly. Your chemical supplier is wrong in saying "only according to pH you can keep the quantity of degreasing." Actually you need to titrate the strong and weak caustics in your caustic and titrate the free acid in your pickle tank. (Which acid do you use?) (And what type of degreasing do you use? Is it caustic soda ⇦liquid caustic soda in bulk on
Amazon [affil link]
or phosphoric acid?)
Regards,
Galvanizing Consultant - Hot Springs, South Dakota, USA
A. One point about grease and oil.
While it's true that it burns off in the zinc, not really causing any problems at the zinc kettle, the fume it creates can cause problems downstream.
It depends on what system of fume capture and treatment is used.
If you use a bag filter type capture, then oil vapour can cause real problems. It blocks the filter media so that a high pressure drop across the media means poor filtration and then poor extraction.
Of course if no fume extraction systems are used, this might not be a problem.
Scrubbers are not very good with this type of dust, but they don't like oil vapour either. Builds up on the cyclones reducing efficiency.
On flux concentrations:
Its amazing how many systems of notation for strength there are. SG, baumé, Brix, Bolling, API, or %. Can make it confusing for us engineers to understand the chemistry!
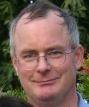
Geoff Crowley
Crithwood Ltd.
Westfield, Scotland, UK
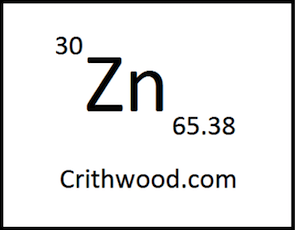
Q. I use degreasing that contains Phosphoric acid at about 8-12%.and after galvanizing there is still bare spots and/or ungalvanized areas.I think it can be related excess aluminum(%0,04)that sometimes oxidized by the means of air blowing or burning of potatoes.and also related not enough preheating.When the materials are dipped without preheating, Zinc ammonium chloride does not adhere the surface and this results in ungalvanized area.
what are the optimum range on the subject of Al content,Zinc chloride and ammonium chloride amount in the flux solution, preheating degree(C)..?
Best regards..
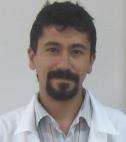
Hakan Esen, Material Engineer(BSc.)
galvanizing plant manager - Bursa, Turkey
A. Sir:
Your aluminum in the zinc of 0.04% is MUCH TOO HIGH. Stop adding aluminum (LOCK IT UP) until you are BELOW 0.007%. This will usually take at least several weeks. At 0.04% I expect nothing except black (bare) spots. Check the baumé of your phosphoric acid degreaser. I was under the assumption that acid degreaser was only a few percent in phosphoric acid. Actually I do not like preheating. I like low baumé quadraflux at 160 F (71C) with no preheating of the product prior to entry into the zinc.
If you look at my response to letter 47904, you will get more knowledge regarding flux use in Europe and North America.
Again I say to you "...spend a few thousand dollars..." on the right galvanizing consultant and learn what to do. Time is money and your %GZU must be very high. This is the zinc consumed divided by product galvanized times 100% (no credits for ash or dross). If you could post your %GZU it would be interesting.
My experience with bag houses is that a flux with low ACN plugs them and flux with higher ACN does not. The change-over seems to be about ACN=1.
Regards,
Galvanizing Consultant - Hot Springs, South Dakota, USA
I agree with Tom, your Al too high.
Get it down as he says - and there's no easy way except dilution with clean zinc. There are many "old wives tales", with things like potatoes (smells like roast dinner!) etc, but they don't work.
We run about 0.001 %Al.
Excess causes bare spots.
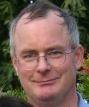
Geoff Crowley
Crithwood Ltd.
Westfield, Scotland, UK
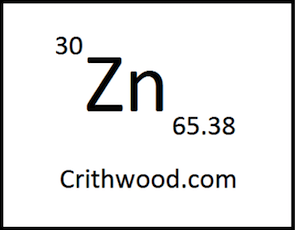
A. Sir:
Most (but not all) of my clients using quadraflux and IQM use between 0.0005% and 0.001% aluminum in their zinc. This requires daily small additions of aluminum depending on production (e.g. actually depending on the number of times the kettle is skimmed as 95% of the added aluminum goes out with the dry skims).
Regards,
Galvanizing Consultant - Hot Springs, South Dakota, USA

Q, A, or Comment on THIS thread -or- Start a NEW Thread